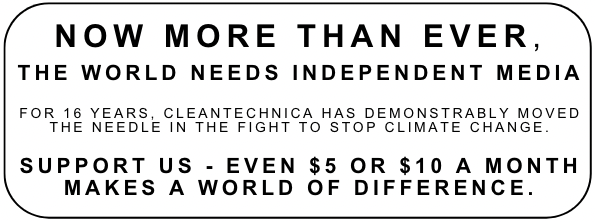
Sign up for daily news updates from CleanTechnica on email. Or follow us on Google News!
Key Takeaways:
- Trucks won’t all be electric immediately, so don’t build charging for 100% electric
- Design charging microgrids for standardized increments of capacity
- Analyze all sites and design increments that are good enough
Gaining the benefits of electric trucks, including significantly reduced maintenance and operations costs and increasing market share, doesn’t have to start big. In fact, the best way to start is small, within the constraints of the grid, leveraging buffering batteries and onsite solar to enable a portion of the fleet at the depot or visiting truck stops to be electric immediately. Adding capacity to the microgrid, often aligned with the ability of utilities to add grid connections and approval for larger solar arrays, can be integrated with increases in electric fleet sizes.
As the authors — Rish Ghatikar and Michael Barnard, experts in sustainability, transportation, and strategy — explored in their diagnosis of the challenges of truck charging, there are overlapping concerns which can heavily slow down deployment of megawatt scale charging solutions to accelerate truck electrification. That led to the simplifying policy of depot and truck stop microgrids with solar, battery storage, power management, and charging systems.
The target audiences for this material — major logistics firms like Walmart which own and operate many depots, owners of significant numbers of truck stops, and likely turn-key vendors of microgrids for truck charging — must consider not only the solution of a microgrid, but an approach to charging-based microgrids that is optimal given the challenges and constraints to charge electric trucks.
A key challenge of installing charging systems with an optimal mix of power levels is that a grid connection capable of delivering a megawatt or more of power to each of several charge points for heavy trucks simultaneously can take years to be approved and delivered. It requires the utility to restructure the grid from the truck stop to the secondary distribution substation and likely to the primary distribution substation. It can require new wires capable of delivering the higher power required. It will require a very significant scale of transformer at the truck stop.
A second key challenge is that there won’t be that many trucks to charge initially, so high capital costs would need to be serviced until truck and charging throughput volumes increase.
The authors propose a design principle, which is to plan for optimal capacity, start with small build-outs, and incrementally add charging, generation, and storage capacity to the microgrid as more demand is anticipated, likely in two to three subsequent increments. The corollary to this is that the components chosen for the microgrid must be amenable to this, something explored more fully in the next action article on microgrid component modularity for truck charging.
A small starting point can be achieved with a suitable grid connection in months, not years. One of the authors, Barnard, explored this with a hypothetical truck stop in the article Dirt Cheap Batteries Enable Megawatt-Scale Charging Without Big Grid Upgrades Right Away, inspired by the announcement by EV battery giant CATL of $56 per kWh LFP batteries deliverable in the fourth quarter of 2024. Such microgrids ensure power is available to trucks when needed.
Truck stops already consume a good deal of electricity for the pumps, air pressure hoses, repair services, restaurant facilities, climate control, etc. They have much more grid-connected load than the average residence, typically capable of delivering 360 kW or more of power. That’s used well under maximum potential power and energy demand levels, as they are overbuilt to avoid challenges and enable later growth. Further, there are peaks and lulls over the day, with typical rush points when many trucks arrive simultaneously, along with other truck stop customers.
The figure below is a simplified example of what battery buffering at a truck stop can achieve. The flat line near the bottom is a constant draw of about 80% of maximum power from the grid over 24 hours. The bright colored, tall and peaky line is the charge of a 1.5 MWh capacity battery pack. The dashed lines are trucks charging.
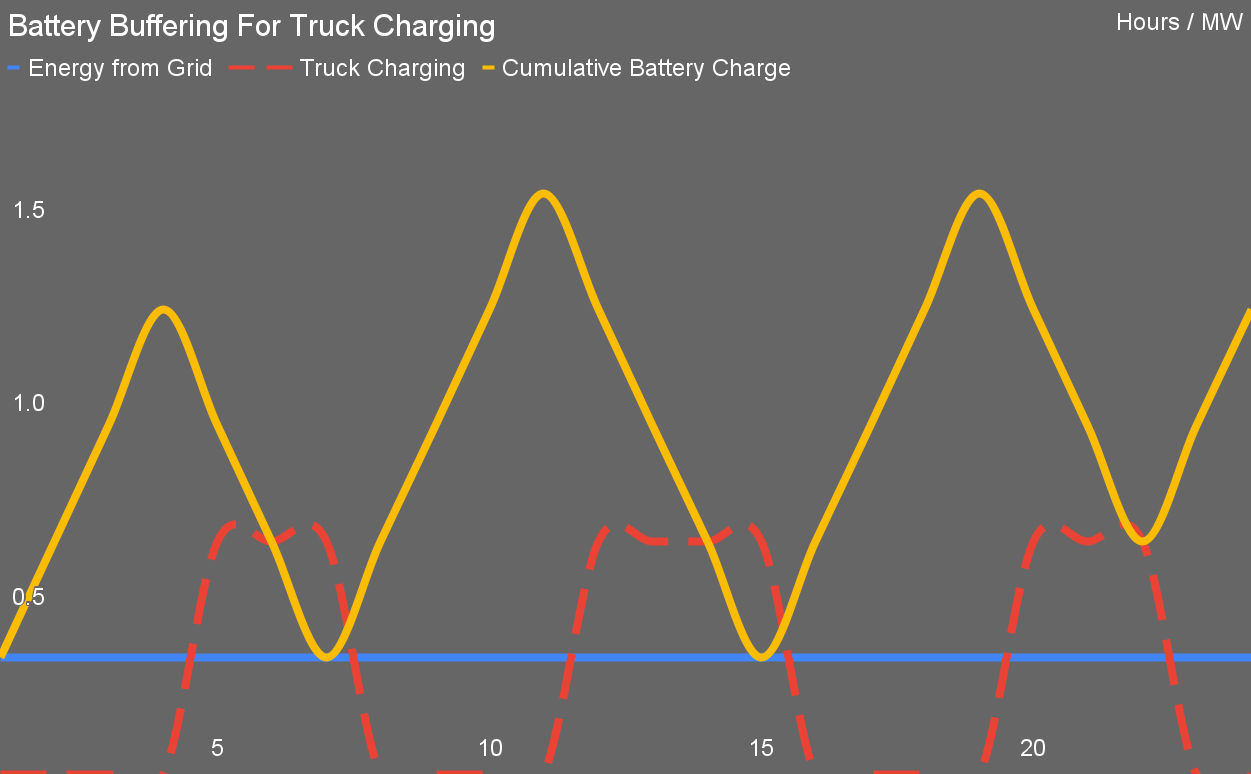
Over the 24 hours, the battery’s charge goes up and down, but demands from the grid remain constant. When a truck rolls in needing its 1 MWh battery charged, it will likely be at 20% charge and wish to get to 80%, the normal procedure for the fastest charge for the highest range with the lowest battery degradation. Batteries charge more slowly from 80% to 100%, so recharging from 20% to 80% is optimal for normal use and increases battery lifespan.
600 kWh is sufficient for a Tesla Semi to drive 300 miles before recharging is again required, and for other current models of trucks like the Nikola, about 270 miles. That’s five to six hours of driving time, half of the permitted driving time for a driver in the US per day.
This simple model with a relatively inexpensive buffer battery at the rapidly lowering battery costs we’re seeing serves 10 semi trucks a day from one or two megawatt-scale chargers, sufficient for initial truck volumes in most cases for most truck stop locations in the first year of electrification of trucking.
Obviously this simplified model doesn’t account for other electricity demands in the truck stop, including the increasing numbers of electric cars that will undoubtedly want to quickly charge and move on as well. However, this scale of power demand, 360 kW, typically takes 1-3 months to install, so adding it to the existing solution isn’t significantly expensive or time consuming.
Typically it takes less than a year to put in a power connection sufficient for double that power draw — 720 kW. A slightly bigger battery would enable over 20 trucks to be charged in rush periods.
Of course, it also makes sense to add solar panels on all rooftops and canopies, including parking lot shading canopies constructed to maximize local generation, as well as nearby fields, when available, that can be leased for the purpose. This too can be done in stages as the microgrid expands. This can eliminate daytime power demands from the grid entirely, and over time provide local grid stabilization, demand management, and net metering returns of energy to avoid utilities from having to purchase more capacity.
Conceptually for a truck stop, as shown in the illustration below, a first increment would put solar panels on the drive through truck fueling canopy and the truck stop building. A pair of megawatt-scale chargers would replace two fuel pumps or be added to the end of the fueling canopy. A battery-electric storage system sized for the required capacity would be built in an appropriate place on the lot. The second increment would add solar panels on canopies over the car park, adding shade amenity and some car charging, more megawatt-scale chargers and more battery capacity. The third increment would include a solar farm in a nearby field, when available, and more megawatt-scale chargers, more battery capacity, and finally an upgraded grid connection. Collectively, solar generation and battery energy storage with microgrid energy management collectively function as a distributed energy resource. Note that in the diagram, BESS is an abbreviation for battery energy storage system, a commonly used acronym in the space.
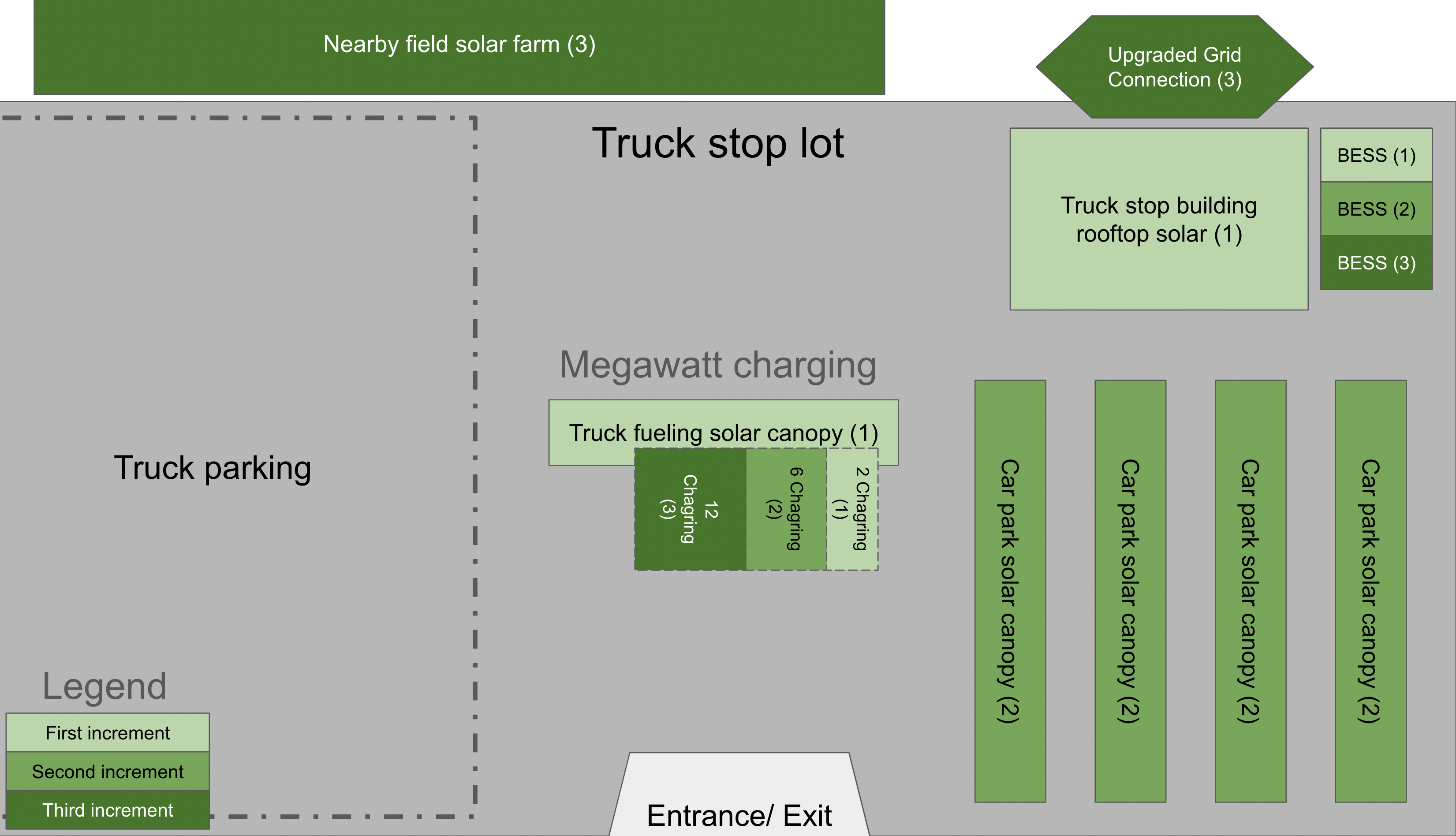
The pattern for depot charging will be different of course, shown conceptually in the illustration below. A typical depot pattern of nighttime parked fleets and daytime deliveries can minimize the need for megawatt-scale charging. Depot vehicles usually have shorter service day mileage than long haul trucks and so will require fewer kWh of charging each day. Also these vehicles have longer dwell times, and slower charging levels can meet the charging needs. A buffer battery may need to have a higher capacity to shift more electricity from solar generation into the nighttime, as an obvious example of distributed energy resource sizing optimization.
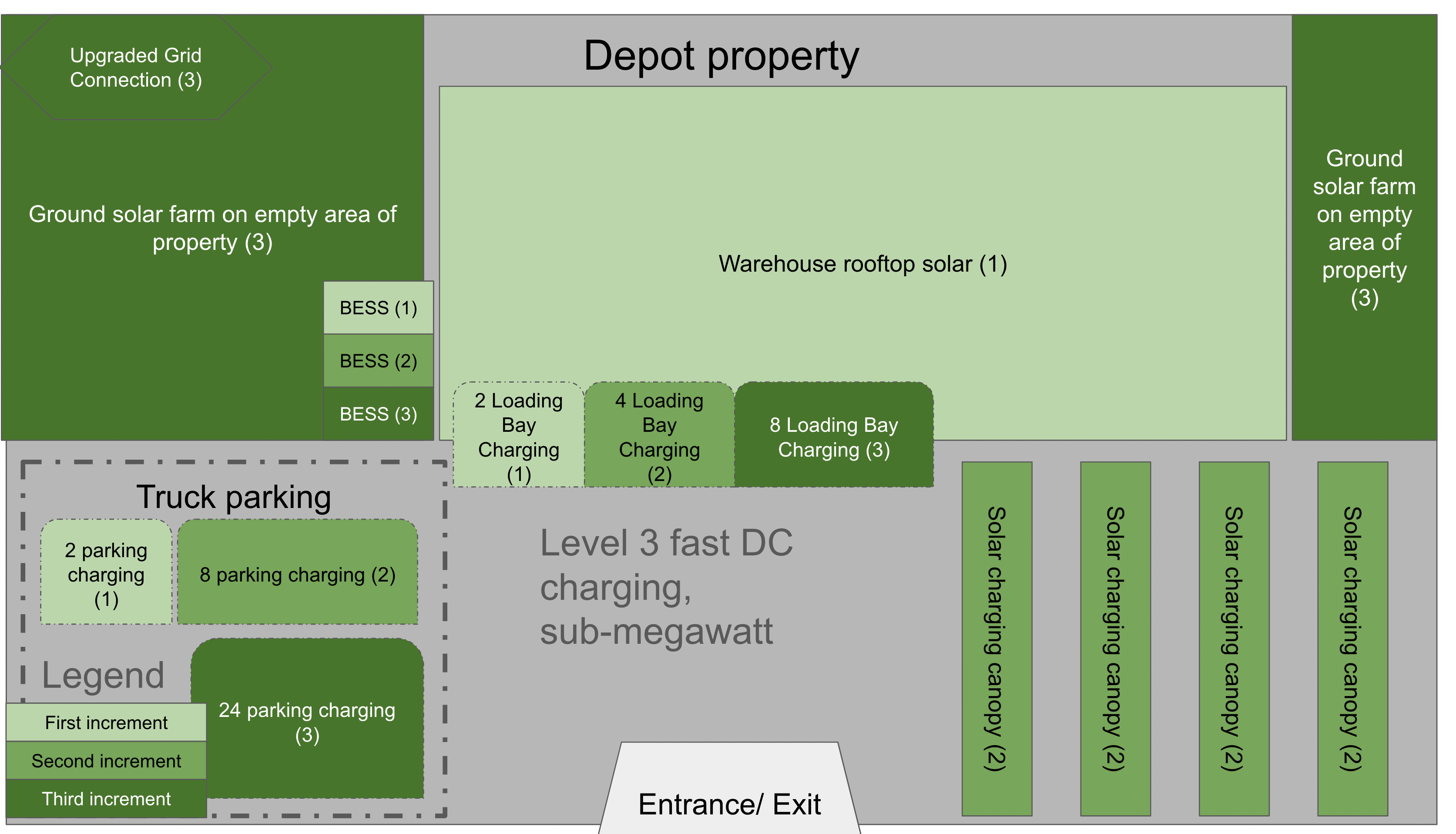
Conceptually, the first increment of depot charging would have warehouse rooftop solar, an appropriately sized battery, some parking Level 3 or even Level 2 charging, and some loading bay Level 3 charging for top ups. The second increment would add more parking and loading bay charging and solar canopies with Level 2 charging for light vehicles including delivery vans and employee vehicles, as well as additional battery capacity. The third increment would complete loading bay charging potential, include all truck stalls with chargers, put additional solar on empty fields on the property and finally upgrade the grid connection.
When land and electric expansion is possible, megawatt charging stations for microgrids must be designed to incrementally scale with power systems capable of high power loads, which may involve reinforced grid interconnections or integration with on-site energy generation and storage solutions. To support high power demands and reduce grid dependency, such microgrid truck charging must use sustainable distributed energy sources such as solar panels and energy storage. Use of solar panels and energy storage systems aligns with sustainability targets for fleet operators looking to lower carbon footprints and meet their environmental, social, and governance plans. Such solutions not only offer microgrid resiliency (to operate in an islanded mode), it can also reduce long-term operational costs by using lower-cost renewable energy and energy management services. The costs of microgrids for trucks at both depots and stops depends on the number and types of chargers installed and magnitude of distributed energy sources, site size, and electrical interconnection, to name a few.
Any sizing and electrical connection needs must be optimally designed to ensure adequate sizing based on local freight operational needs. Any lower sizing of charging strains freight logistics’ confidence in electric truck charging to meet their operational needs. Conversely, higher sizing of charging strains grid power procurement from utilities or grid operators and increases operational costs for microgrids.
What’s been observed in electrifying fleets that follow this pattern is that total productive hours for drivers can actually increase. In many cases, a depot truck’s first stop in the morning is a gas station nearby, and lineups for gas pumps are a fact of life. Driving to the gas station, fueling, and then driving to the first delivery point is replaced with driving straight to the first delivery point. Fleets are finding up to an hour of additional delivery time in a day with battery-electric vehicles that are already charged when drivers show up to work.
For a major organization considering a series of microgrids, standardization of the components, sizes, and vendors is key. There will be a Pareto optimum size for likely three or four increments over time, and the authors’ recommendation is that each is a standardized size, power, capacity, and components mix that is repeated multiple times. No site is unique. Creating a simple menu of three to four sizes of charging microgrid to pick from and a simple sizing algorithm avoids what Flyvbjerg terms the uniqueness bias and will accelerate deployment, reduce risks, and reduce costs. More details on differences in sites and the key requirement for standardized modularity are in the next article.
Obviously, a small initial increment will mean faster planning and construction time, and lower capital costs, matching expenditures more closely to increased revenue.
The next action for the target audiences is to consider the locations that they have under their control, and rank them by volume. Either develop the expertise in house or hire an external consulting firm to develop an initial microgrid capacity increments set that make sense for your business and volumes. This will inform later actions and may be adjusted.
Previous articles in this series:
About the authors:
Rish Ghatikar has an extensive background in decarbonization, specializing in electric vehicles (EVs), grid integration, and demand response (DR) technologies. At General Motors (GM), he advanced transportation electrification energy services, as part of a broader climate strategy. Previously, at Electric Power Research Institute (EPRI), he focused on digitalizing the electric sector, while at Greenlots, he commercialized EV-grid and energy storage solutions. His work at the DOE’s Lawrence Berkeley National Laboratory spearheaded DR automation to support dynamic utility pricing policies. An active climate advocate, Ghatikar advises on policies and technologies that align the grid with transportation and energy use for sustainable growth.
Michael Barnard, a climate futurist and chief strategist at The Future Is Electric (TFIE), advises executives, boards, and investors on long-term decarbonization strategies, projecting scenarios 40 to 80 years into the future. His work spans industries from transportation and agriculture to heavy industry, advocating for total electrification and renewable energy expansion. Barnard, also a co-founder of Trace Intercept and an Advisory Board member for electric aviation startup FLIMAX, contributes regularly to climate discourse as a writer and host of the Redefining Energy – Tech podcast. His perspectives emphasize practical solutions rooted in physics, economics, and human behavior, aiming to accelerate the transition to a sustainable future.

Chip in a few dollars a month to help support independent cleantech coverage that helps to accelerate the cleantech revolution!
Have a tip for CleanTechnica? Want to advertise? Want to suggest a guest for our CleanTech Talk podcast? Contact us here.
Sign up for our daily newsletter for 15 new cleantech stories a day. Or sign up for our weekly one if daily is too frequent.
CleanTechnica uses affiliate links. See our policy here.
CleanTechnica’s Comment Policy