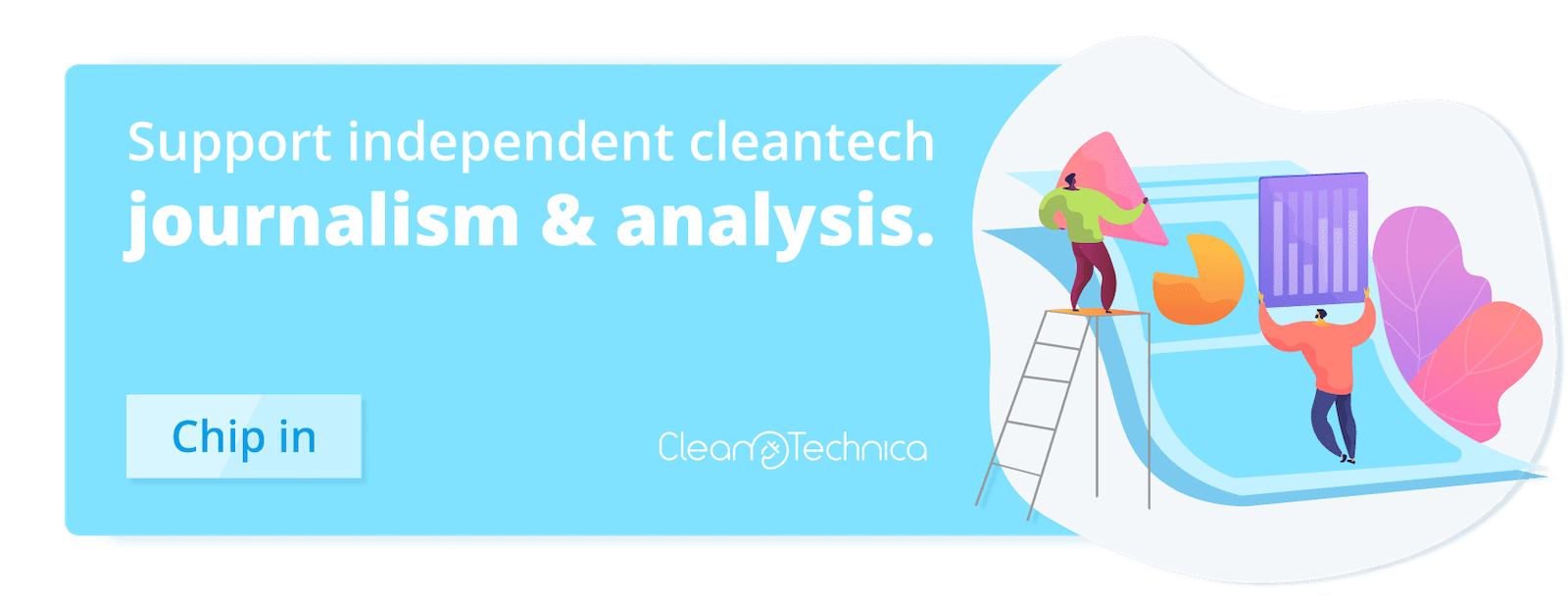
Now that the electric vehicle transition is rolling full steam ahead, automakers are scrambling to get their hands on enough EV batteries to fill the demand. That means lithium, lithium, and more lithium. Opening up new supply lines is one key strategy, but attention is also focusing on next-generation manufacturing technologies that squeeze every last bit of zero emission value from the soft, silvery-white metal.
Better EV Batteries: Look Ma, No Solvents
The latest development in EV battery technology comes from Oak Ridge National Laboratory (ORNL), which is part of the US Department of Energy’s sprawling network of research facilities, in a public-private partnership with the US energy storage firm Navitas Systems.
The research team took aim at the conventional, slurry-based method for applying lithium to the electrodes of EV batteries. The slurry method is effective as far as it goes, but the slurry itself is a stew of toxic solvents that carry the risk of health and environmental impacts. The slurry method also involves added expenses, including drying and cycling back into the process.
Instead of trying to reduce toxic solvents in the lithium slurry, the ORNL research team ditched it altogether, in favor of the new dry processing method.
The new method involves creating a compact powder-based material. That’s not as simple as it sounds, but the payoff could be huge in terms of the stretching out the lifespan of EV batteries and improving their performance.
“This eliminates the solvent while showing promise for delivering a battery that is durable, less weighed down by inactive elements and able to maintain high energy storage capacity after use,” Oak Ridge reported earlier this week (see more of our Oak Ridge coverage here).
“Such improvements could boost wider EV adoption, helping to reduce carbon emissions and achieve U.S. climate goals,” the lab added.
The Dry Processing Difference, Eventually
Don’t hold your breath for the new slurry-free, non-toxic lithium-ion EV batteries of the future. The ORNL team is still in the early phase of the R&D process. However, the dry processing method is already known as a space, time, and energy-saving manufacturing method. The lab also cites lower start-up costs and improved efficiencies in waste disposal as benefits.
The lead researcher on the Navitas side, Bryan Steinhoff, explains that manufacturers can ditch bulky coating and solvent equipment if they switch to the dry processing method. “If you can use a dry process instead, you can reduce your footprint by up to 40 or 50%, saving hundreds of millions of dollars,” Steinhoff says, referring to the cost of new gigascale EV battery factories.
ORNL also points out that dry processing is compatible with other electrode manufacturing equipment.
Understanding How Better EV Batteries Work
Knowing what works is not the same as knowing why it works, though. Understanding the why is the next step before dry processing can applied to EV batteries for the mass market.
In the current phase of the research, the ORNL team analyzed dry-processed electrodes manufactured by Navitas and reported their results in the Chemical Engineering Journal.
Check out their work under the title,”High-throughput and high-performance lithium-ion batteries via dry processing.” For those of you on the go, the short answer is that dry processing enables manufacturers to pack more active materials into the electrode.
The thicker electrode is relatively easy to fabricate and could lead to gains in loading performance, but that leads to the long answer. The thickness of the electrode could be a limiting factor in terms of power. In the next phase of the research, one focus of attention will be the polytetrafluoroethylene binder for the lithium powder.
“A main goal for this project is to develop or identify a better binder for the dry process, because the current binder is not very stable for the anode environment,” explained Oak Ridge Jianlin Li, co-leader of the team, along with Runming Tao of ORNL.
Safer Manufacturing For Lithium-Ion EV Batteries
Stay tuned for more on that. Meanwhile, the ORNL team has good company elsewhere in the world of EV battery research. In March, for example, the journal Nature Communications published a study on EV battery dry processing from a research team in Korea under the title, “Ultrahigh loading dry-process for solvent-free lithium-ion battery electrode fabrication.”
The Korean team observed that conventional EV batteries are made with an “expensive organic solvent [that] evaporates very slowly.” They estimated 78% of the cost of producing electrodes is related to drying and recovery steps.
In particular, they name-checked the solvent N-methyl-2-pyrrolidone, noting somewhat alarmingly that it is “is not only toxic (known to cause male infertility) but also flammable.”
More Lithium For The USA
The Korean team reported promising results for a dry powder made with carbon nanotubes and polyvinylidene fluoride, so stay tuned for more on that as well.
Meanwhile, US policymakers are determined to revive the nation’s moribund lithium industry, but obstacles abound. For example, a proposed open pit lithium mine on federal land Nevada has encountered stiff headwinds, including opposition from local tribes. A new Appeals Court ruling appears to have cleared the way for construction to begin this summer, but it’s not a good look for fans of zero emission electric mobility.
A less contentious approach may be coming soon. The US Department of Energy has been focusing attention on producing lithium from geothermal brine. That approach would sharply reduce the surface footprint of lithium extraction.
The challenge is to come up with an economical brine extraction method that can compete with environmentally destructive but less expensive methods. The firm Controlled Thermal Resources believes it has discovered the magic recipe, by combining the value of lithium with the value of geothermal energy.
The firm began work on its “Hell’s Kitchen Lithium and Power” project at the Salton Sea region of Imperial Valley, California in 2021.
In a visit to the Hell’s Kitchen project earlier this year, California Governor Gavin Newsome highlighted the potential for “Lithium Valley” to feed the thirst for EV batteries in the US and beyond.
“Experts believe Lithium Valley could provide enough lithium to meet all of America’s future demand and more than one-third of global demand – supercharging the transition to zero-emission vehicles,” the Governor’s office explained.
On the same trip, US Congressman Raul Ruiz (D-CA25) suggested that California’s collaborative approach avoids the acrimony sparked by the Nevada lithium mine, including the participation of tribal stakeholders.
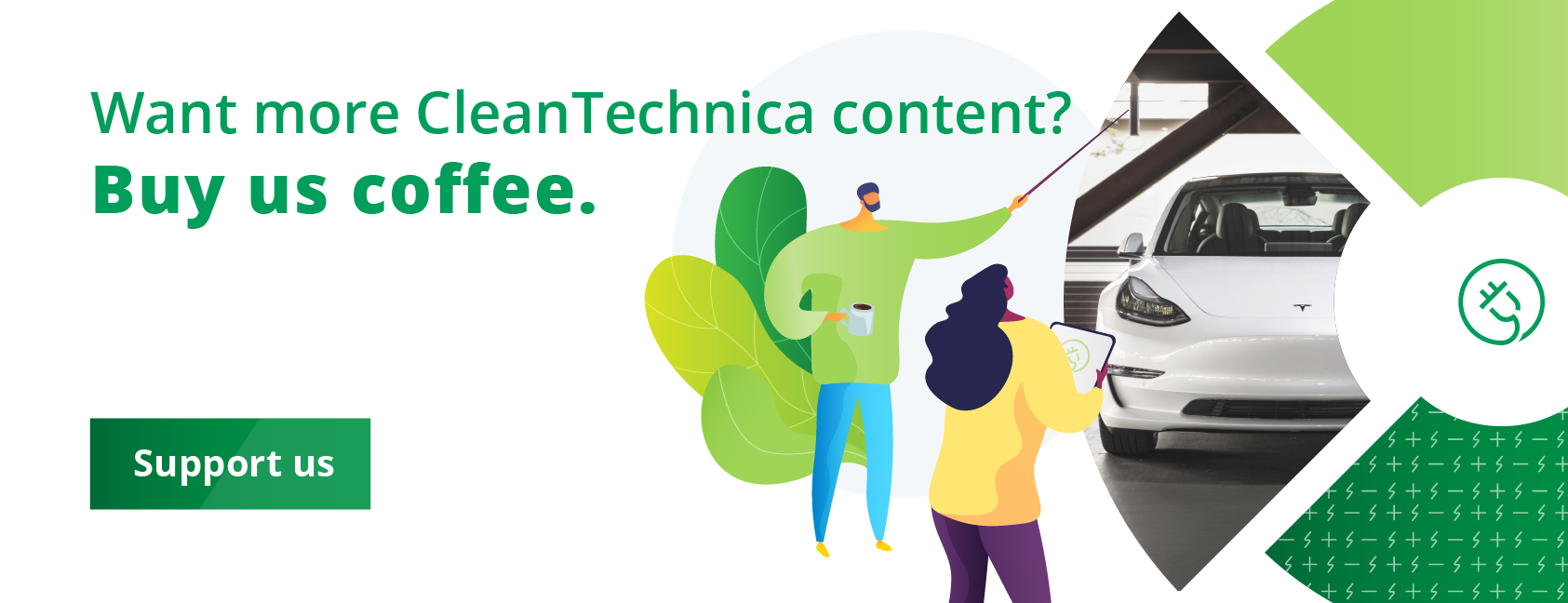
That viewpoint was endorsed by the Chairman of the Torres Martinez Desert Cahuilla, Thomas Tortez, Jr., who took note of “the Governor’s commitment to strengthen Tribal communities with Tribal inclusion, meaningful person-to-person dialogue with a timeline, considering Tribal communities as active participants in clean energy transitions and in collective decision-making with a determination to succeed.”
“Lithium extraction and geothermal power are a step in the right direction, but let’s ensure Tribal cultural protections and fair distribution of clean energy benefits, avoiding disproportionate negative impacts on Tribal communities,” he emphasized.
Find me on Threads @tinamcasey. Also Post @tinamcasey, or @TinaMCasey on LinkedIn and Spoutible, or @Casey on Mastadon, or Twitter (for now) @tinamcasey.
Photo: New dry processing method for fabricating lithium-ion EV batteries courtesy of Navitas Systems via Oak Ridge National Laboratory.
I don’t like paywalls. You don’t like paywalls. Who likes paywalls? Here at CleanTechnica, we implemented a limited paywall for a while, but it always felt wrong — and it was always tough to decide what we should put behind there. In theory, your most exclusive and best content goes behind a paywall. But then fewer people read it! We just don’t like paywalls, and so we’ve decided to ditch ours. Unfortunately, the media business is still a tough, cut-throat business with tiny margins. It’s a never-ending Olympic challenge to stay above water or even perhaps — gasp — grow. So …
Sign up for daily news updates from CleanTechnica on email. Or follow us on Google News!
Have a tip for CleanTechnica, want to advertise, or want to suggest a guest for our CleanTech Talk podcast? Contact us here.
Former Tesla Battery Expert Leading Lyten Into New Lithium-Sulfur Battery Era:
CleanTechnica uses affiliate links. See our policy here.