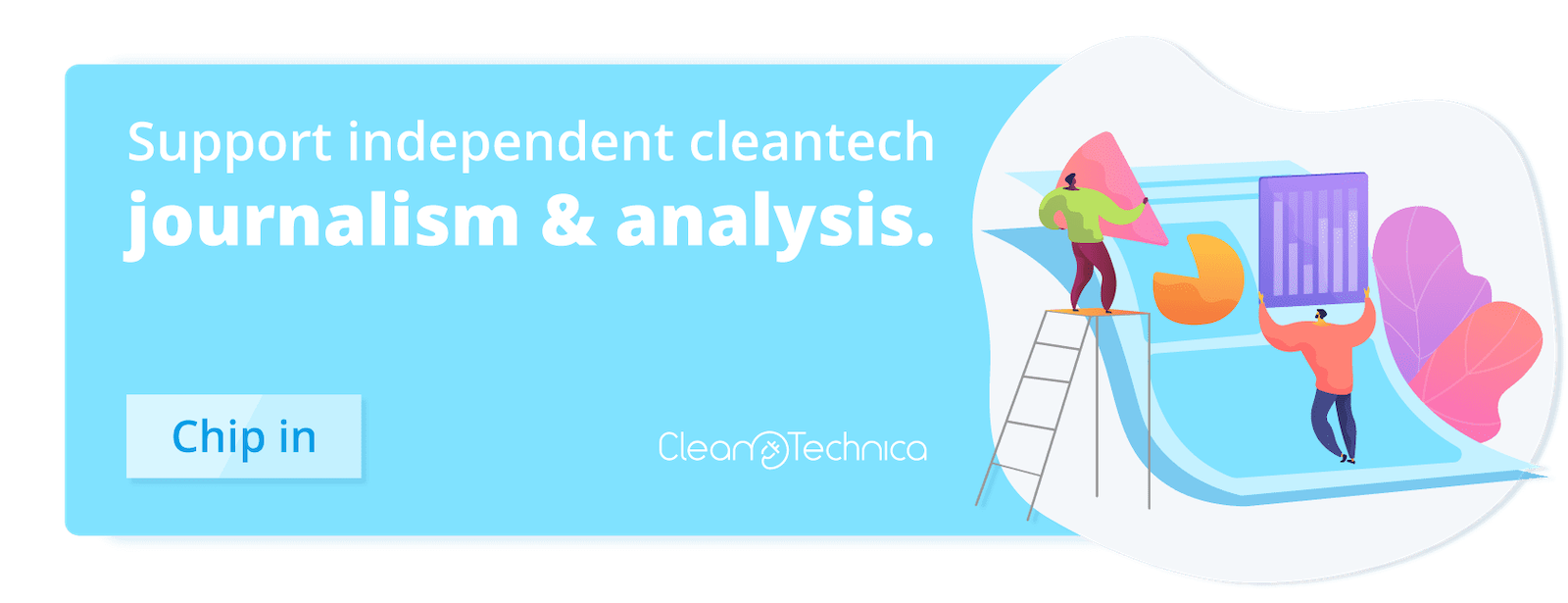
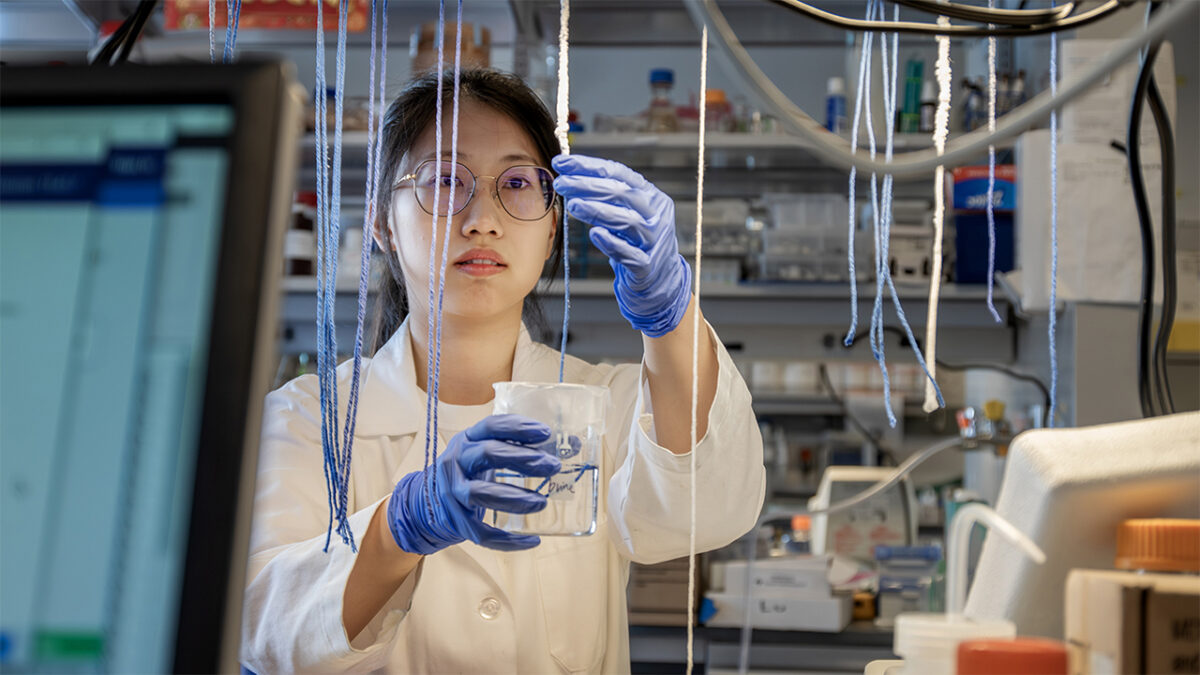
Meiqi Yang, graduate student in civil and environmental engineering and one of the study’s lead authors, works on a string-based technology that extracts lithium salts from a brine solution. (Photo by Bumper DeJesus, via Princeton University)
A vital component of the batteries at the heart of electric vehicles and grid energy storage, lithium is key to a clean energy future. But producing the silvery-white metal comes with significant environmental costs. Among them is the vast amount of land and time needed to extract lithium from briny water, with large operations running into the dozens of square miles and often requiring over a year to begin production.
Now, researchers at Princeton have developed an extraction technique that slashes the amount of land and time needed for lithium production. The researchers say their system can improve production at existing lithium facilities and unlock sources previously seen as too small or diluted to be worthwhile.
The core of the technique, described Sept. 7 in Nature Water, is a set of porous fibers twisted into strings, which the researchers engineered to have a water-loving core and a water-repelling surface. When the ends are dipped in a salt-water solution, the water travels up the strings through capillary action — the same process trees use to draw water from roots to leaves. The water quickly evaporates from each string’s surface, leaving behind salt ions such as sodium and lithium. As water continues to evaporate, the salts become increasingly concentrated and eventually form sodium chloride and lithium chloride crystals on the strings, allowing for easy harvesting.
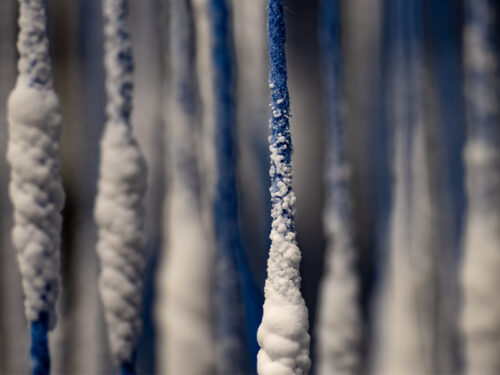
Salts form on the surface of the strings. (Photo by Bumper DeJesus, via Princeton University)
In addition to concentrating the salts, the technique causes lithium and sodium to crystallize at distinct locations along the string due to their different physical properties. Sodium, with low solubility, crystallizes on the lower part of the string, while the highly soluble lithium salts crystallize near the top. The natural separation allowed the team to collect lithium and sodium individually, a feat that typically requires the use of additional chemicals.
“We aimed to leverage the fundamental processes of evaporation and capillary action to concentrate, separate and harvest lithium,” said Z. Jason Ren, professor of civil and environmental engineering and the Andlinger Center for Energy and the Environment at Princeton and the leader of the research team. “We do not need to apply additional chemicals, as is the case with many other extraction technologies, and the process saves a lot of water compared to traditional evaporation approaches.”
Limited supply of lithium is one obstacle to the transition to a low-carbon society, Ren added. “Our approach is cheap, easy to operate, and requires very little energy. It’s an environmentally friendly solution to a critical energy challenge.”
An evaporation pond on a string
Conventional brine extraction involves building a series of huge evaporation ponds to concentrate lithium from salt flats, salty lakes, or groundwater aquifers. The process can take anywhere from several months to a few years. The operations are only commercially viable in a handful of locations around the world that have sufficiently high starting lithium concentrations, an abundance of available land, and an arid climate to maximize evaporation. For instance, there is only one active brine-based lithium extraction operation in the United States, located in Nevada and covering over seven square miles.
The string technique is far more compact and can begin producing lithium much more quickly. Although the researchers caution that it will take additional work to scale their technology from the lab to an industrial scale, they estimate it can cut the amount of land needed by more than 90% compared to current operations and can accelerate the evaporation process by more than 20 times compared to traditional evaporation ponds, potentially yielding initial lithium harvests in less than one month.
Compact, low-cost, rapid operations could expand access to include new sources of lithium, such as disused oil and gas wells and geothermal brines, that are currently too small or too dilute for lithium extraction. The researchers said the accelerated evaporation rate could also allow for operation in more humid climates. They are even investigating whether the technology would allow for lithium extraction from seawater.
“Our process is like putting an evaporation pond on a string, allowing us to obtain lithium harvests with a significantly reduced spatial footprint and with more precise control of the process,” said Sunxiang (Sean) Zheng, study coauthor and former Andlinger Center Distinguished Postdoctoral Fellow. “If scaled, we may open up new vistas for environmentally friendly lithium extraction.”
Since the materials to produce the strings are cheap and the technology does not require chemical treatments to operate, the researchers said that with additional enhancements, their approach would be a strong candidate for widespread adoption. In the paper, the researchers demonstrated the potential scalability of their approach by constructing an array of 100 lithium-extracting strings.
Ren’s team is already developing a second generation of the technique that will enable greater efficiency, higher throughput, and more control over the crystallization process. He credits the Princeton Catalysis Initiative for providing critical initial support to enable creative research collaborations. Additionally, his team recently received an NSF Partnerships for Innovation Award and an award from Princeton’s Intellectual Property (IP) Accelerator Fund to support the research and development process, including ways to modify the approach to extract other critical minerals in addition to lithium. Together with Kelsey Hatzell, assistant professor of mechanical and aerospace engineering and the Andlinger Center for Energy and the Environment, Ren also received seed funding from the Princeton Center for Complex Materials to better understand the crystallization process.
Zheng is leading the launch of a startup, PureLi Inc., to begin the process of refining the technology and eventually bringing it to the wider marketplace. Zheng was selected as one of four researchers in the inaugural START Entrepreneurs cohort at Princeton, an academic fellowship and startup accelerator designed to foster inclusive entrepreneurship.
“As a researcher, you know firsthand that many new technologies are too expensive or difficult to scale,” Zheng said. “But we are very excited about this one, and with some additional efficiency improvements, we think it has incredible potential to make a real impact on the world.”
A string of collaborators
Ren said the breakthrough discovery was made possible through an extensive collaborative effort between research groups at Princeton and the University of Maryland.
For example, working with Liangbing Hu, the Herbert Rabin Distinguished Professor in the Department of Mechanical Engineering at the University of Maryland, inspired the researchers to use and treat the fiber material to maximize the technology’s efficiency.
Ren’s research team also turned to Howard Stone, the Donald R. Dixon ’69 and Elizabeth W. Dixon Professor of Mechanical and Aerospace Engineering, and Fernando Temprano-Coleto, an Andlinger Center Distinguished Postdoctoral Fellow working with Stone, to understand and model the fundamental fluid mechanics and transport processes that underpin the strings’ impressive lithium-harvesting capabilities.
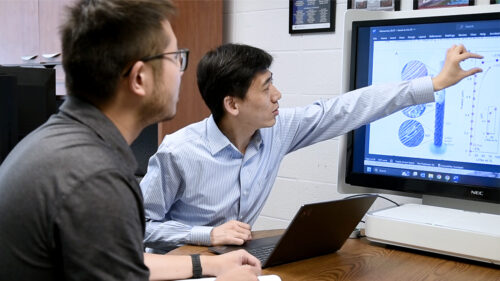
Ren (center) examines data with Sean Zheng. (Photo by Bumper DeJesus, via Princeton University)
“Once you can arrive at a mathematical description of the process, not only can you understand what you’ve already observed, but you also gain predictive power,” said Temprano-Coleto. “With a model in place, you can start to play with the variables to optimize the process and understand how it will perform under different conditions.”
Ren’s team tapped into the materials characterization expertise of Nan Yao, professor of the practice at the Princeton Materials Institute, and the unique facilities available at Princeton’s Imaging and Analysis Center to characterize the materials’ structure and spatial arrangement. Yao is the center’s director.
“It is difficult to detect an element like lithium using traditional characterization techniques because it is so light, with only three electrons involved to emit a very weak X-ray signal,” said Yao. “Fortunately, at the Imaging and Analysis Center, we have a suite of high-end, cutting-edge instrumentation that enabled us to collect the information we needed.”
Yao and Guangming Cheng, an associate research scholar in Yao’s group, worked with the lead author Xi Chen, former associate research scholar in civil and environmental engineering in the Ren lab who is now an associate professor at Tsinghua University, to use an advanced technique known as electron energy loss spectroscopy alongside scanning transmission electron microscopy to characterize the spatial arrangement of lithium and sodium along the strings. Their work revealed that lithium and sodium separated from each other vertically along the string as well as radially, with sodium crystallizing primarily on the surface of the interwoven strings and lithium concentrating in the center. The discovery could inform ongoing efforts to increase the efficiency of the existing approach.
“Each of our collaborators contributed a critically important piece to our work, from uncovering the fundamental processes behind the high efficiency of our technology to characterizing the final materials,” Ren said. “We could not have accomplished our work without the expertise of everyone on the project.”
The paper, “Spatially Separated Crystallization for Selective Lithium Extraction from Saline Water,” was published online Sept. 7 in Nature Water. In addition to Ren, Zheng, Hu, Temprano-Coleto, Stone, Yao, Cheng and Chen, study authors include Meiqi Yang of Princeton University and Qi Dong of the University of Maryland.
By Colton Poore, Andlinger Center for Energy and the Environment, Princeton University
I don’t like paywalls. You don’t like paywalls. Who likes paywalls? Here at CleanTechnica, we implemented a limited paywall for a while, but it always felt wrong — and it was always tough to decide what we should put behind there. In theory, your most exclusive and best content goes behind a paywall. But then fewer people read it! We just don’t like paywalls, and so we’ve decided to ditch ours. Unfortunately, the media business is still a tough, cut-throat business with tiny margins. It’s a never-ending Olympic challenge to stay above water or even perhaps — gasp — grow. So …