
According to the International Energy Agency (IEA), global energy-related greenhouse gas (GHG) emissions hit an all-time high in 2022, reaching 4.1 gigatons of CO2-equivalent. Carbon dioxide emissions are a major cause for concern in the fight against climate change, but CO2 is not the only GHG the industry must address.
Methane, for example, is a significant GHG across oil and gas production – accounting for 57% of operational emissions in the natural gas sector. IEA data suggests there could also be substantial underreporting of methane emissions, which is particularly concerning given that methane’s potency at trapping warmth in the atmosphere is approximately 28 times more than that of CO2.
Other gases are far more potent still. Nitrous oxide (NOx), for instance, has a 300 times stronger heat-trapping ability than CO2. While it only amounts to 6% of the world’s GHG emissions, its potential to make considerable contributions to climate change at lower levels of emission means that it is not to be ignored.
Oil & gas: Scope 1, 2, and 3 emissions targets
In 2022, oil and gas operations were responsible for 15% of global energy-related Scope 1 and 2 GHG emissions, while the use of oil and gas products by end users (Scope 3 emissions) contributed to a further 40%.
As this data from the IEA indicates, much of the oil and gas industry’s GHG emissions originate from sold products. Indeed, according to analysis by GlobalData, Scope 3 emissions account for 75% of the average emissions of the world’s top 18 oil and gas companies, followed by 13% for Scope 2 and 12% for Scope 1.
While eliminating Scope 3 emissions entirely would require net-zero products, which is difficult to achieve, it is possible to reduce them through renewable fuels, offsets, and carbon capture technologies, for example. Nevertheless, the focus for most companies in the sector is currently on Scope 1 and 2.
Analysis by GlobalData shows that of the 28 major oil and gas companies around the world, most have set targets for Scope 1 and 2 emissions, with less than half announcing any ambitions to address Scope 3 levels. For the Scope 1 and 2 targets, most of the more ambitious companies are aiming to achieve reductions of between 40-50% by 2030.
Improving refinery efficiency for reduced CO2 and NOx
Achieving these plans will require a wide range of strategies, from lower-emission fuels during operations to investing in new technologies such as carbon capture and storage solutions. Adapting operational and maintenance processes to improve energy efficiency will also play a pivotal role in achieving targets.
In 2020, refining activities accounted for the largest proportion of emissions within the US oil and gas value chain (41%). Refineries are therefore expected to be a key focus for energy efficiency improvements in the coming years. Within the refinery, fired heaters have the highest fuel consumption, translating to high emissions and operating prices. Of particular concern are catalytic reformers, steam methane reformers (SMR), and ethylene furnaces.
According to Integrated Global Services (IGS), addressing fired heater performance at refineries, petrochemical and chemical facilities can lead to emissions reductions of up to 25% for NOx and 15% for CO2. The table below shows the average fuel savings and emission reductions that can be achieved for a variety of fired heater types used across refineries and industrial sites.
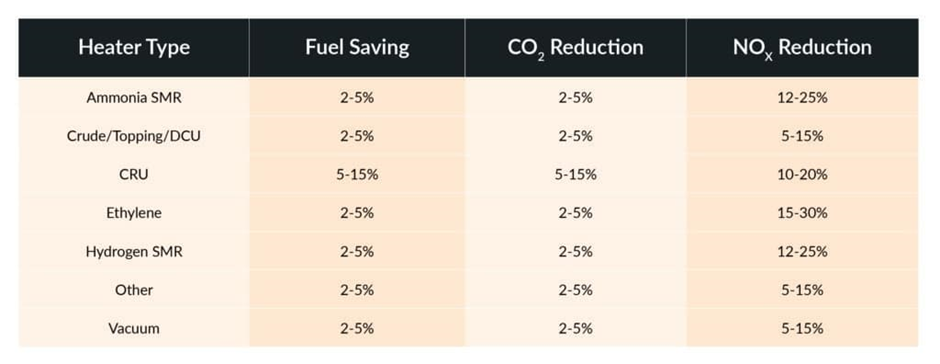
IGS is a key partner to the world’s leading energy and industrial companies, helping plants around the world solve a range of engineering-related challenges that directly impact on the efficiency, sustainability, and reliability of their equipment’s performance. Plants partner with IGS to evaluate their fired heater and understand the opportunities for fuel savings, capacity increase, and emissions reduction. The evaluation estimates the results that can be achieved with the application of one or several innovative technologies: high-emissivity Cetek coatings, Tube Tech cleaning services, and Environmental SCR (selective catalytic reduction) solutions.
Cetek coating can be applied onto the refractory, process tubes, or both, depending on the type of heater and its design and operating parameters. This helps to solve the challenge of poor heat transfer by maximising radiant absorbed duty to improve efficiency. The Tube Tech robotic convection section cleaning system achieves a 90%+ clean area, removing fouling build-up to restore fired heater performance without the safety risks associated with manual/man entry cleaning. If the fired heater has an adjacent selective catalytic reduction (SCR), environmental screens and ammonia mixing systems can significantly improve its performance and catalyst life.
Improving furnace efficiency is an essential strategy in reducing the significant energy input required by refining operations. To access specific case studies and learn more about how IGS can help you reduce emissions by optimising your equipment’s efficiency, please download the whitepaper below.
Sign up for our daily news round-up!
Give your business an edge with our leading industry insights.