Sign up for daily news updates from CleanTechnica on email. Or follow us on Google News!
As momentum for electric vehicles accelerates in the U.S., a skilled and trained auto manufacturing workforce will be necessary for a successful transition.
Policies like the Inflation Reduction Act and Bipartisan Infrastructure Law have helped deliver more than $154 billion in investments into building electric vehicles and components. By 2035, EVs could potentially account for 71% of U.S. car sales; and are expected to increase to 80% to 100% by 2050. But there are many unknowns about how this transition will impact U.S. auto manufacturing workers.
Nearly 900,000 workers are responsible for manufacturing large auto parts or systems and assembling final internal combustion engine vehicles at original equipment manufacturers (OEMs) and Tier 1 suppliers, according to data analyzed from the U.S. Bureau of Labor Statistics (BLS). These vehicles are powered by burning gasoline as opposed to EVs, which rely on electric motors and battery packs instead of internal combustion engines and components like fueling and exhaust systems. As components within powertrain systems are expected to be the source of the greatest manufacturing differences between the two types of vehicles, it’s expected that there will be significant implications for these workers.
Key Differences Between Internal Combustion Engine and Electric Vehicles
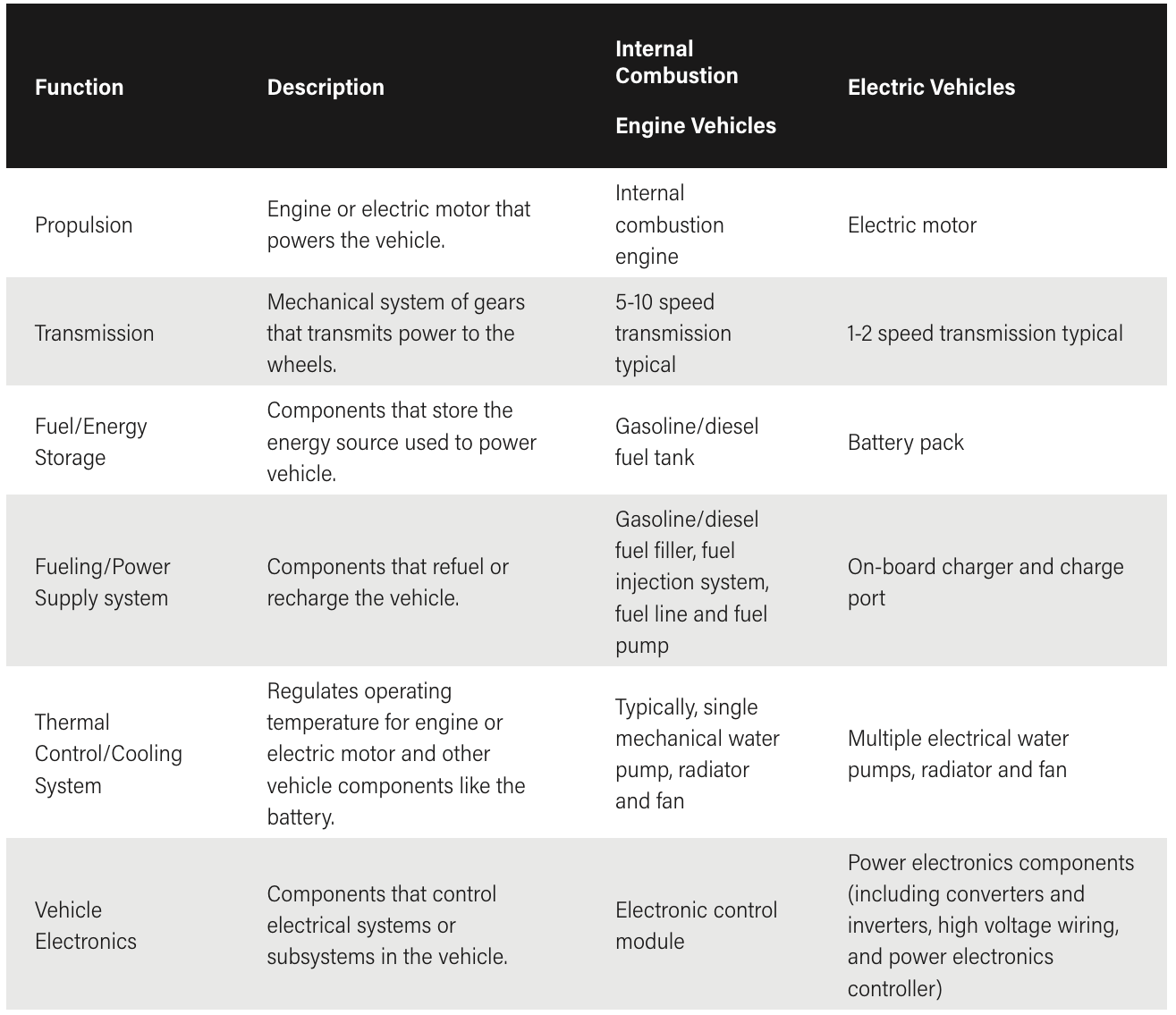
Many questions among the auto workforce are therefore emerging:
- What types of occupations are expected to see disruptions?
- Which new occupations will EVs and their associated components or technologies require?
- How will training requirements be updated to ensure that manufacturing workers gain new skills?
- Where will in-demand jobs in the EV supply chain be located: in legacy auto manufacturing communities or in burgeoning centers of automotive innovation, like the Battery Belt?
Here are four ways the EV transition will impact demand for manufacturing skills and labor, including job quality considerations such as fair wages, safe work environments and work-life balance. These insights can help shape the policies and strategies that drive a domestic EV supply chain, while ensuring that auto manufacturing communities — both legacy and new — see the creation of high-quality, community-sustaining jobs.
1) Key Manufacturing Differences Will Transform Many Auto Industry Jobs
Supply chain jobs that are linked to parts only relevant to internal combustion engine vehicles such as engines and fuel injection systems, may have the greatest risk of displacement as more EVs are produced. Of the more than 886,000 workers at OEMs and Tier 1 suppliers — firms that manufacture large parts or systems and assemble final vehicles — close to 58,000 workers focused on gasoline engines and engine parts manufacturing are likely to experience the most severe employment impacts. Fifty-seven percent of those workers are located in Michigan, Ohio, Indiana, Tennessee and Kentucky.
On the other hand, Tier 1 firms that manufacture non-powertrain components (like steering, suspension, and other interior components) that are common across all kinds of vehicles may experience low or no impacts.
In between, there are some suppliers who are likely to witness medium disruption and will need to readjust their workforce. For instance, the shift towards electrification will significantly impact machine tool manufacturers. EVs require fewer as well as different powertrain components, which in turn require different machine tools for manufacturing those components.
The Biden Administration has already announced $15.5 billion in investments dedicated to retooling manufacturing facilities, with an emphasis for creating good quality jobs and supporting facilities with strong ties to auto manufacturing.
Auto Manufacturing Employment Disruption Risks During the Transition to Electric Vehicles
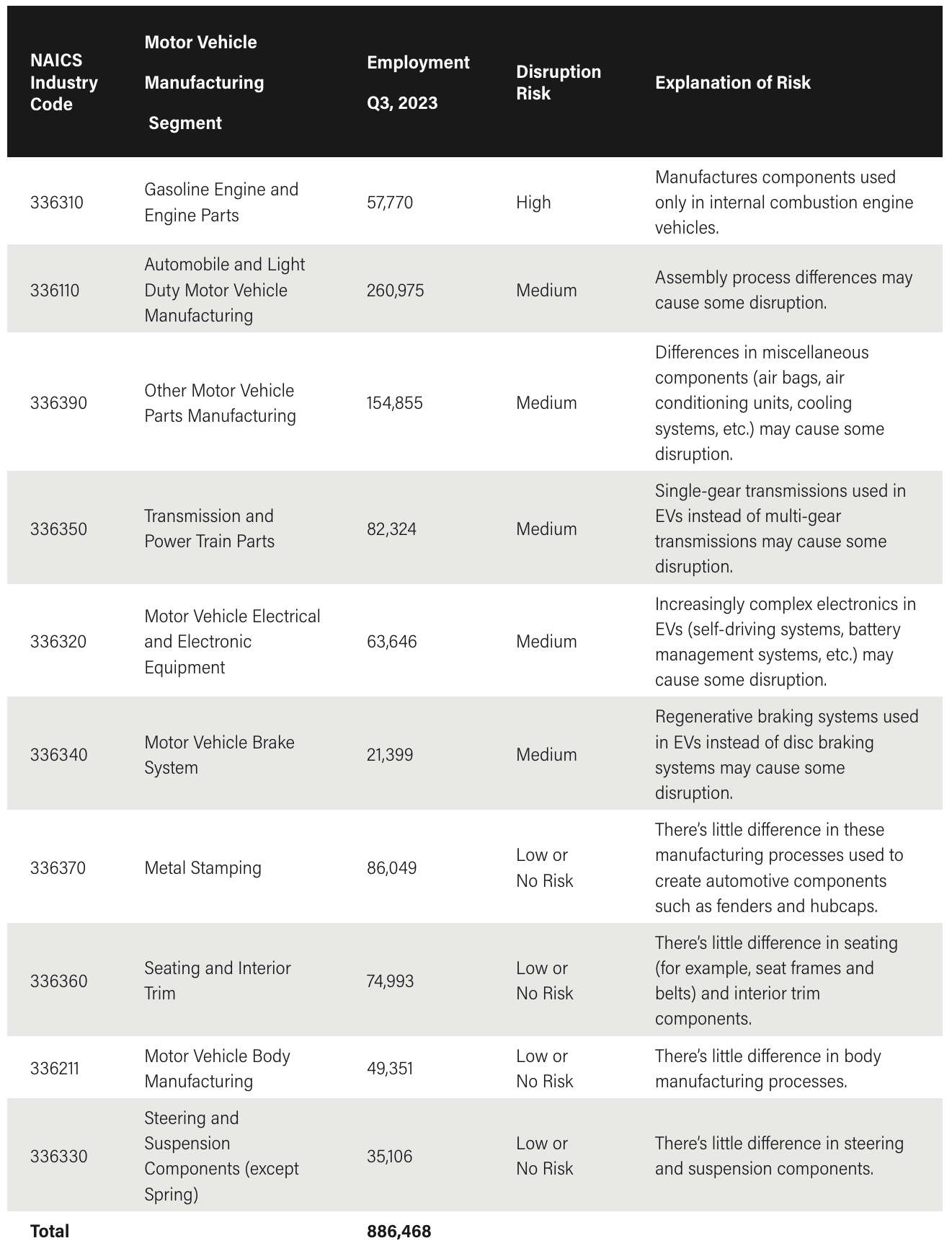
Job disruptions at Tier 2 and Tier 3 firms that are further down the supply chain (for instance, tire manufacturing or paint and coating manufacturing), are also likely to be limited or not see any impacts at all, as many of these parts may be agnostic to how the vehicle is powered. These companies are also more likely to supply other industries beyond the automotive industry. This could vary across different firms depending on how heavily their production is tied to vehicle parts.
As the market for internal combustion engine vehicle components — from gas tanks to fuel injectors — shrinks, suppliers of those parts will have to choose how to embrace the EV transition and adapt their workforce to new product lines. Small-to-medium sized businesses with lower profit margins could find it more difficult to convert their production lines for the EV industry or diversify to other sectors than larger companies. Furthermore, uncertainty about how quickly the growing market for EV parts will overtake internal combustion engine components can cause businesses to be unsure about any workforce changes they will need to make. Recent trends also point towards other considerations. For example, how will hybrid vehicles fit into this new vehicle market? Regardless, workers who are transferred to new products will require retraining.
Meanwhile, EVs are likely to generate growing demand for jobs related to the design and development of various EV models, manufacturing of batteries to power them and charging stations to keep them running on the road. As software and power electronics use increases in vehicles, occupations in computer and engineering fields will play a pivotal role in their design and development.
Similarly, the opening of new battery manufacturing facilities will generate significant new jobs. The BLS estimates employment in this industry and other industries associated with vehicle electrical equipment manufacturing to increase by 17% between 2021 and 2031, making it one of the fastest growing manufacturing industries. Currently, the battery manufacturing industry employs 52,500 workers, according to the BLS. An analysis by WRI and BW Research Partnership estimate that 13,400 of these workers are involved in the manufacturing of vehicle-related batteries, based on Motor and Equipment Association’s assumption that 27% of employment in the battery manufacturing industry is related to the vehicle supply chain. Employment in battery manufacturing is poised to increase significantly due to the investments taking place in battery component, cell and pack manufacturing.
Scaling up battery manufacturing will require more engineers who can design and test batteries as well as more assemblers, technicians and other production workers to operate machines and transport materials safely. A recent employer-focused battery industry workforce needs assessment conducted by the Center for Automotive Research highlights that employers expect hiring to increase by more than 20% by 2026 with roles like engineering, technician, and manufacturer/assembler in high demand.
Furthermore, a 2022 study by researchers at Carnegie Mellon University finds that the labor intensity of manufacturing EV powertrains may be greater than internal combustion engine vehicle powertrains once accounting for battery manufacturing. There is also growing recognition that assembly-related labor hours for EVs are greater than for internal combustion engine vehicles.
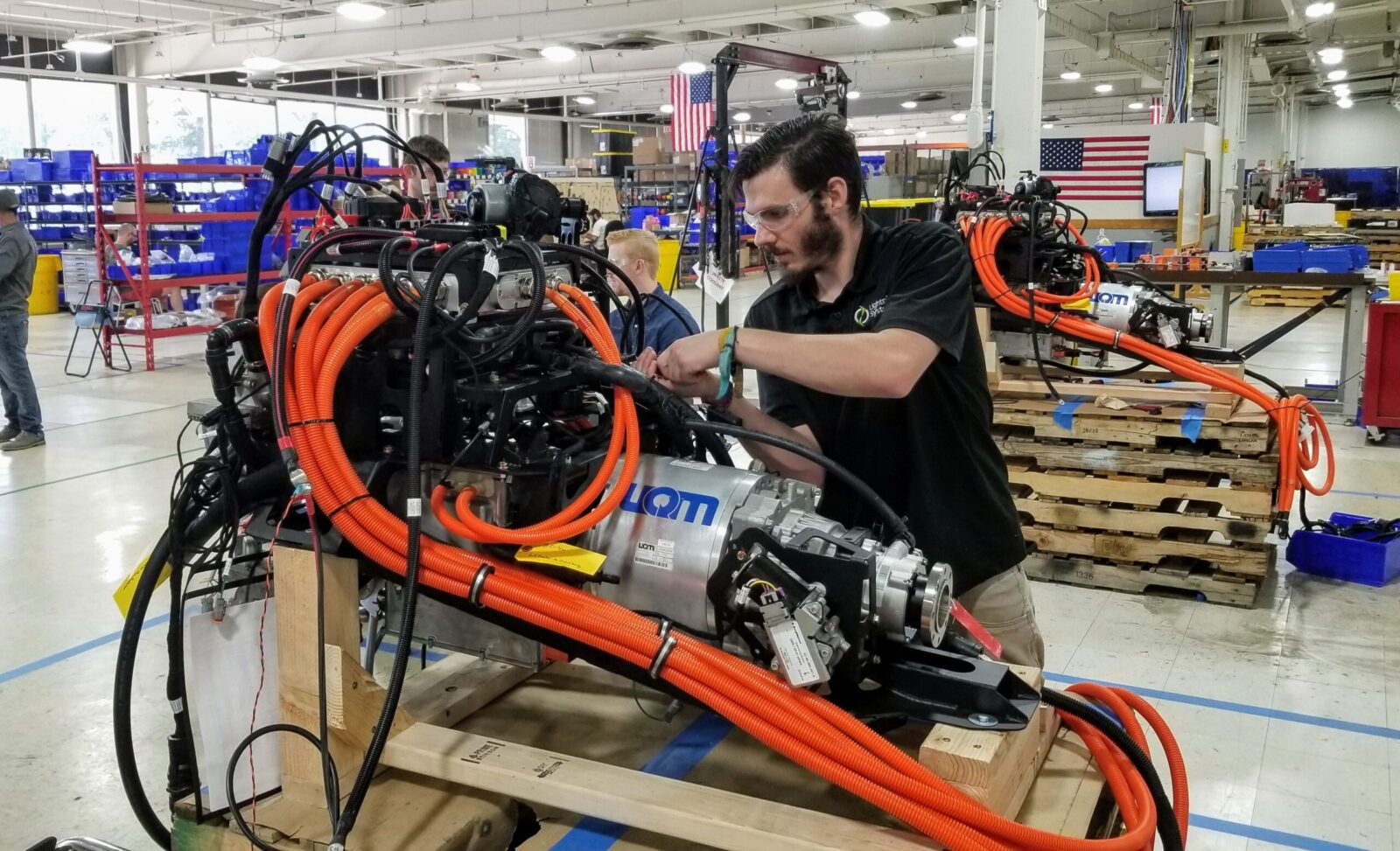
2) The EV Transition Will Increasingly Require New Digital, Advanced Manufacturing and Specialized Skills
The transition to EVs will shift the auto industry from a completely mechanical production process to an electrochemical production process. These technical demands mean that workers with technical and digital skills will be increasingly needed to interact with human-machine interfaces, analyze and manage data, and utilize specialized knowledge of vehicle technologies and systems thinking. Chemical skills and safety-focused skills including the ability to handle hazardous EV components or parts are some other noticeable gaps.
More specifically, some prominent skill gaps that downstream employers (for example, cell and pack manufacturing, vehicle applications like assembly or disassembly, and battery recycling) are concerned with include chemical engineering and materials science, battery chemistry and competency with battery management software systems. Other closely related skills including testing and quality control, managing automated tools and data analysis for process control will also be in high demand.
Workers’ perspectives also point toward the need for different training considerations. Another Carnegie Mellon University study, which interviewed production workers and technicians across different U.S. auto firms, shows that while there are overlaps in the range of skills required for both EV and internal combustion engine vehicle operators and technicians, production practices used by EV manufacturers may increase the demand for select skills like complex problem solving and safe chemical handling. Cross-cutting skills and precision and engineering skills associated with electronics and electrical components are other emerging requirements that are likely to increase.
3) Artificial Intelligence Vertical Integration Will Likely Impact Workers and Their Needed Training
Increasing use of artificial intelligence in the automotive supply chain and vertical integration are already contributing to workforce disruption and are likely to become a larger issue in the EV transition.
Robots and machines are already on the factory floor around the world, with most automotive factories leveraging some degree of automation at nearly every stage of vehicle production. Now AI is poised to play a bigger role throughout the automotive value chain as the industry transitions to EVs. Within automotive manufacturing itself, automakers are beginning to use AI to streamline the research and development process for new vehicles, minimize design and development time, and identify and correct flaws during the manufacturing of the vehicles. For EVs, AI is being used to predict battery maintenance and project its lifespan. This will help drivers know when they need to replace the battery while also enabling car manufacturers to improve research and development.
The automotive industry will increasingly need workers with AI skills, machine learning and data analysis, and will be competing with other industries such as software and semiconductor for talent. AI technologies could also increase automation and replacement of certain jobs.
Automakers are also vertically integrating by moving battery and other components like motors in-house in order to have more supply chain control and retain intellectual property. This is an outcome from the many supply-chain disruptions that resulted from the COVID-19 pandemic, a materials shortage and weather disruptions. It’s also in contrast to decades of practice where automakers handed control over vehicle development and production to different suppliers who would produce everything from steering controls to semiconductors and electronic components for multiple vehicle manufacturers.
Tesla for example, has adopted an approach of sourcing raw materials directly, building its own batteries and engineering its own software. As other automakers follow Tesla, they will need to significantly build capabilities and in-house expertise in battery technologies, inverters and electric powertrains.
At the same time, vertical integration can potentially lead to less business for automotive suppliers.
All these trends interact with one another and cannot be looked at in isolation. More importantly, all of them have workforce implications and any subsequent recommendations should account for their impact on workers and their needed training.
4) Job Quality and Fair Compensation Are Key to Ensuring an Equitable and Just EV Transition
With more EV manufacturing poised to take place in the U.S., supercharged by policies like the Inflation Reduction Act and the Bipartisan Infrastructure Law, there are concerns about job quality and union negotiating power.
Jobs in the automotive industry were once a ticket to the middle class, with high pay and good benefits. However, in the last few decades, U.S. auto workers have witnessed a significant decline in wages, working conditions and union bargaining power. This has been accompanied by foreign-owned automotive companies setting up manufacturing plants in Southern states to take advantage of cheaper, non-union labor.
Between 2001 and 2022, Michigan saw a 43% drop in both motor vehicle parts manufacturing and motor vehicles manufacturing employment. During the same time, employment in these two industries in Alabama increased by almost 3 times, while in Kentucky, employment levels fell by 28% between 2001 and 2011, until increasing again by 59% in 2022. In 2022, these two non-union states accounted for 12% of motor vehicle and vehicle parts manufacturing employment in the country.
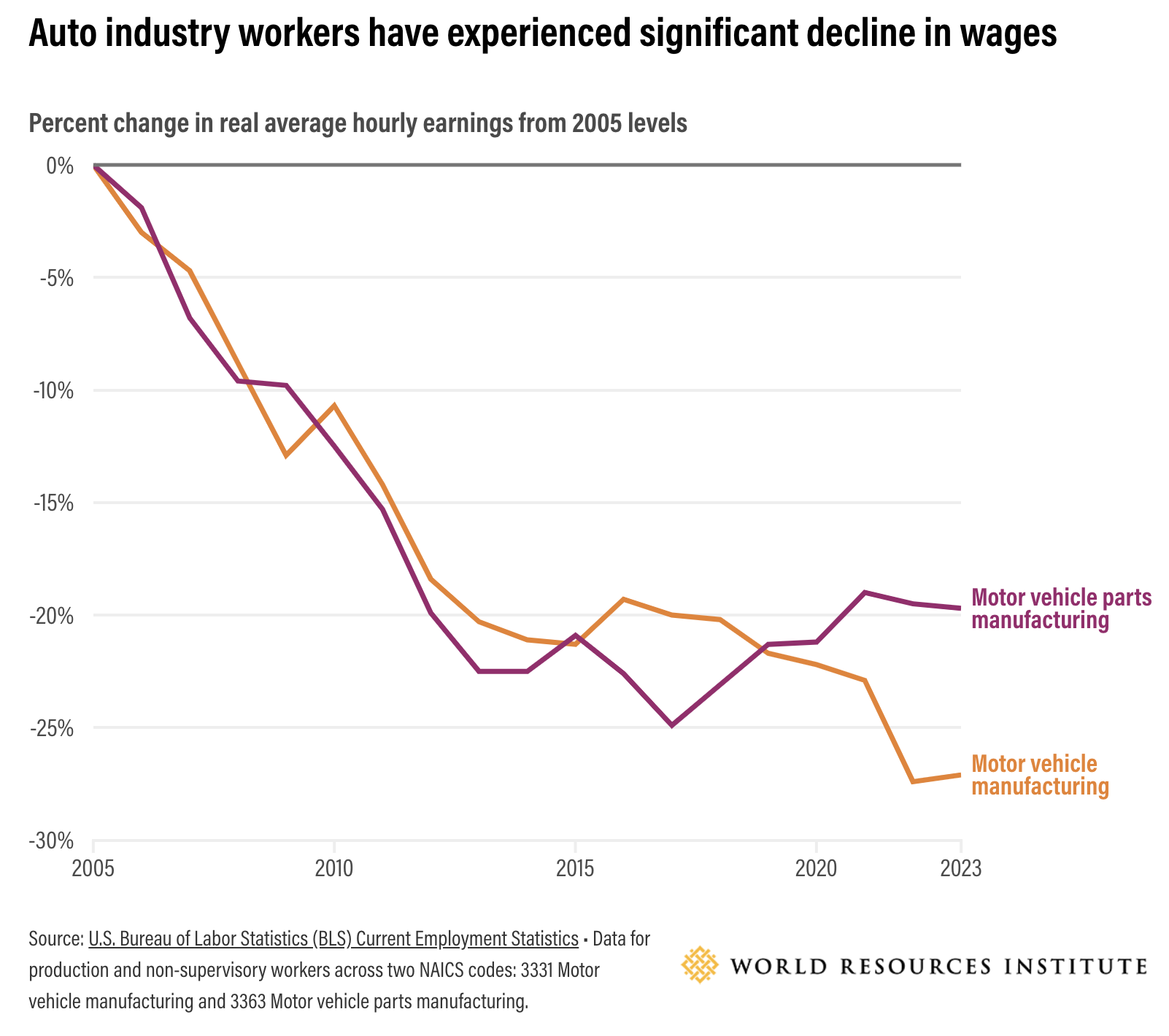
The switch to EVs is reinforcing these regional patterns.
Approximately, 50% ($85.6 billion) of announced private EV investments has happened in just five Southern states — Georgia, Tennessee, South Carolina, North Carolina and Kentucky — which are also what’s known as right-to-work states, making it harder for workers to form unions and collectively bargain for better pay and working conditions.
Automakers are also increasingly turning to joint ventures and partnerships, especially with South Korean companies for battery production, which raise additional questions about long-term job quality and the process of union negotiation in those plants. In 2022, when the EV battery joint venture facility between GM and South Korean LG Energy Solutions opened in Lordstown, Ohio, the starting hourly wage for workers was $15.50, which was roughly half the top pay of a GM assembly worker.
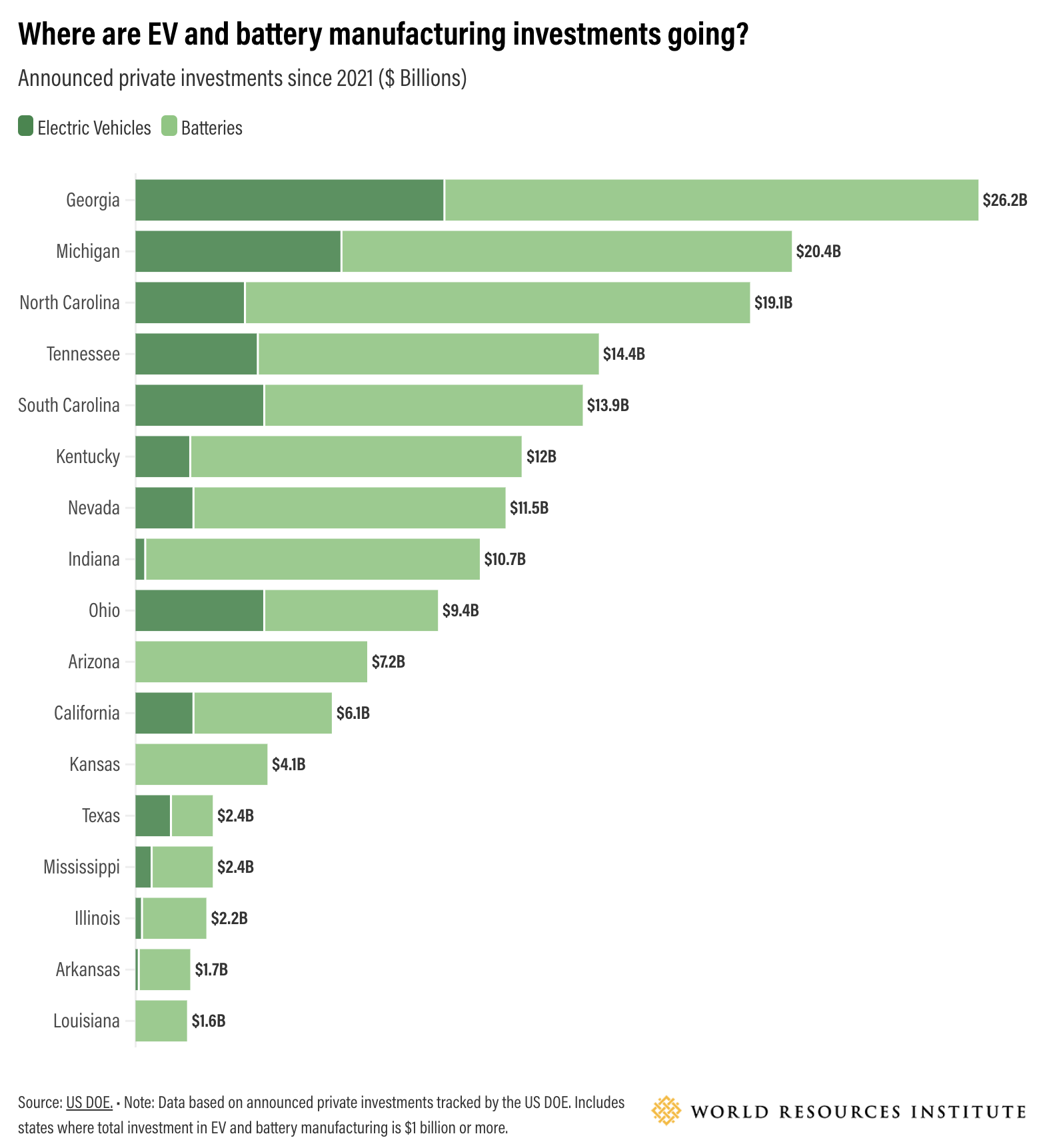
The United Auto Workers (UAW) contract negotiations that reached agreement in the fall of 2023 between the union and the Big Three automakers —GM, Ford and Stellantis — highlight that reversing the negative trajectory is achievable. All three contracts include a 25% wage increase over 4.5 years of the contract, the reinstatement of cost-of-living allowance and a shortening of the number of years it takes for employees to move to a higher pay grade.
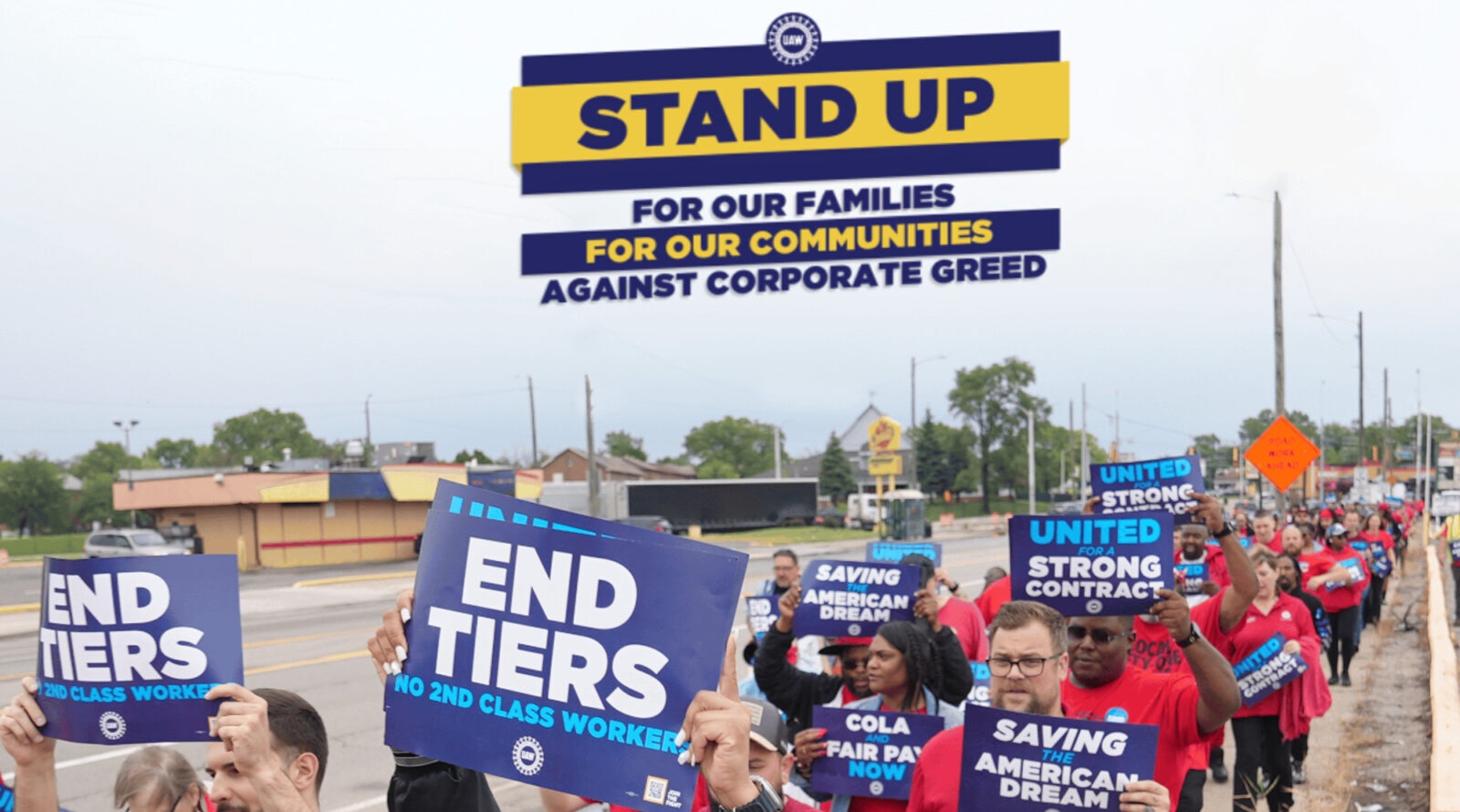
Since then, more automakers outside of the Big Three have announced raises for their workers. Union campaigns are also currently underway at Mercedes-Benz and Hyundai factories in Alabama, while Volkswagen’s Chattanooga, Tennessee plant recently voted to become the first non-Big Three automotive assembly plant in the South to unionize.
The EV transition underscores that good climate policies will not necessarily align with good labor policies unless a concerted effort is made to ensure that workers and unions have a seat at the table. UAW’s ability to organize non-union and foreign automakers like Tesla and Toyota, especially in Southern states, can potentially improve job quality for a broader group of autoworkers while also ensuring a level-playing field for GM, Ford and Stellantis.
A Skilled Workforce Is Necessary for the EV Transition
A successful EV future in the U.S. will require the availability of a skilled workforce that capitalizes on existing skills as well as bolsters workers with new skills.
The EV transition is a tremendous opportunity to improve the prospects for workers and local economies across the country. It will require comprehensive planning and coordination that includes everything from upskilling programs and apprenticeships to internships, university and community college partnerships and better outreach to younger generations. Many stakeholders — including employers, trainers, workforce program designers and community-based organizations supporting workers and learners — will need to coordinate to avoid duplicating efforts, identify and address gaps, and leverage lessons learned from comparable workforce growth in other sectors.
In the coming months, WRI will continue its research into the EV transition and its impact on workers, including which new occupations and their associated components will be required, whether existing auto workers will be able to transfer their skills to EV manufacturing, and the implications for developing workforce education and training programs.
By Devashree Saha, Rajat Shrestha, Nate Hunt, and Evan Kim. Courtesy of WRI.
Have a tip for CleanTechnica? Want to advertise? Want to suggest a guest for our CleanTech Talk podcast? Contact us here.
Latest CleanTechnica.TV Videos
CleanTechnica uses affiliate links. See our policy here.