Sign up for daily news updates from CleanTechnica on email. Or follow us on Google News!
During concrete day… errr … week … errr … verging on two weeks this time, I’ve explored a lot of carbon emissions solutions for the full value chain of the gray glue that ensures our buildings don’t collapse, our bridges stay up, and our underground working chambers don’t pancake. We have to solve this problem, as it’s about 10% of global carbon dioxide emissions, and a bit of the methane emissions as well.
I started with some potentially promising startups, Brimstone and Sublime. Yeah, brand names aimed at venture capitalists, not at the cement, concrete, or construction industries. Brimstone didn’t seem to have a handle on mineral supplies, prevalence of the required chemical components in common rocks or the actual need for cement supplements. Sublime is distinctly using less mature technical avenues, but ones that might use half the power and be able to work against a broader range of materials, including recycled concrete and electric arc furnace slag. Brimstone is unlikely to be a winner, but Sublime is at least in the running, not that it means its approach will necessarily be able to scale or be economic.
Sublime is just one of a raft of firms and organizations trying to exploit electric arc furnaces in different ways to reduce cement emissions. Sublime is trying to reactivate the lime. Cambridge Electric Cement is recycling cement from concrete to displace limestone and its electric arc furnace emissions, in the process creating new lime for new cement. Carbicrete uses the slag in factories to manufacture molded cement pieces by mixing the slag with aggregate and forcing carbon dioxide in to accelerate a natural process. Germany’s DRI-EOS is playing with input chemistries with the limestone adders to try to make the resulting slag into a more directly usable cement substance. Giants Halcim, BASF, and ArcerlorMittal are all using the slag in various aspects of the cement value chain.
A further exploration of cement decarbonization solutions didn’t find any magic bullets, but maybe some magic BBs. Basalt was suggested multiple times, but has a sixth of the lime as limestone, costs more per ton, takes more energy to decompose into lime and carbon dioxide, and would leave behind absurd masses of low-value waste. Burning waste vehicle tires for limestone kilns struck me as a terrible idea, but apparently it’s being used a lot in the USA, Europe, and Japan. Epoxy cements were suggested by many, but are roughly 3-4 times as expensive, along with significant work flow challenges for job sites. Fiberglass to replace rebar and wire mesh was brought up, but it has limitations which I’ll explore in a separate piece. Hoovering lime out of the sea would be like hoovering carbon dioxide out of the air, an enormously energy-intensive and expensive process.
Just electrifying heat would be hugely advantageous from a climate perspective, but it runs into operational costs and the burner box blinders on cement operators heads that makes them look for something cheap to burn, even old truck and car tires, rather than accepting that electricity is just fine and indeed the future.
Then it was levers that could avoid cement entirely. A big one was China’s slowing infrastructure build-out. Another big one was engineered hardwood, aka mass timber. So too was software to optimize the basics to avoid over-ordering. Then software to shave walls down to minimum thickness for the required strength. Then software to try 10,000 alternative designs to find the lowest material designs that met the brief. This is by far the biggest lever to pull.
Most recently, I dug through the gritty world of supplementary cementitious materials, or SCMs. I found that we’re probably at peak replacement of cement with SCMs already, and using coal plant fly ash and blast furnace slag for the most part, with a side helping of pumice and volcanic ash where it’s cheaply available. That put a damper on my earlier assessment of limestone calcined clay cement (LC3) and calcined clays in general. Like pumice and volcanic ash, they are a naturally occurring SCM, but require firing in a kiln to make them effective, are unevenly spread and cost more than Portland cement, never mind much cheaper fly ash and slag which we have mountains of, without moving the climate needle a lot more.
Carbon capture and storage will get its moment in the pitiless spotlight of my assessment, but today let’s turn to the sand and gravel which is mixed with cement, SCMs, and steel in various forms to make concrete. After all, it’s the heaviest mass portion of concrete, 65-85%. Given the tens of billions of tons of concrete we make and use annually, it’s safe to say that the earth moves for concrete.

I assembled the table above to get a sense of the scale of the challenge. 28 billion tons of sand and gravel is a challenge, but how much of a climate challenge is it? Unsurprisingly, China’s demand is head and shoulders above the rest of the world, but as I noted in the article on avoiding cement and concrete use, China’s infrastructure boom is ending, as the country has built the vast majority of cities, roads, railroads, bridges, and tunnels it required. China is still building enormous amounts of wind, solar, hydropower, and transmission, but the cement and concrete requirements for those uses are much lower than highways and entire cities, ones that didn’t exist or barely existed in 1980.
In a typical concrete mix, the proportions are approximately 25-30% sand and 40-45% gravel by volume. Given the total estimated usage of 28 billion tons of concrete across the major geographies, this translates to roughly 7 to 8.4 billion tons of sand and 11.2 to 12.6 billion tons of gravel.
Let’s start with sand. How do we get it, and what’s the impact? Three ways, from the beds of rivers, from coastal and nearshore sand, and by quarrying for it.
Riverbed mining involves extracting sand directly from riverbeds using mechanical equipment such as dredgers and backhoes. This method is prevalent due to the high quality of river sand, which is well-suited for construction purposes. However, riverbed mining has significant environmental impacts, including riverbank erosion, sedimentation, and the destruction of aquatic habitats. These changes can alter the river’s flow, negatively affecting local ecosystems and biodiversity. Over-extraction can also lead to reduced water quality and increased vulnerability to flooding.
Coastal and marine sand mining involves extracting sand from beaches, dunes, and the seabed. This method can have severe consequences for coastal ecosystems, leading to beach erosion, loss of habitat for coastal and marine species, and increased vulnerability of coastal areas to storm surges and sea-level rise. Marine dredging, in particular, disrupts the seabed, affecting marine life and water quality. The removal of sand from coastal areas can also undermine the structural integrity of coastal infrastructure.
Quarry mining of sand involves extracting sand from open pits, typically located inland. This method uses heavy machinery like bulldozers and front-end loaders to excavate sand deposits. While quarry mining can be more controlled compared to riverbed or coastal mining, it still poses significant environmental challenges. The excavation process leads to land degradation, deforestation, and loss of habitats. Additionally, quarry mining generates dust and noise pollution, impacting nearby communities and wildlife.
What about gravel? Unsurprisingly, there’s overlap, with quarries and water playing a role again.
Quarrying is a primary method for obtaining gravel used in concrete production. It involves identifying and extracting gravel deposits from natural rock formations. Once a suitable site is chosen, controlled blasting techniques are employed to loosen the gravel from the quarry bed. Heavy machinery such as excavators, loaders, and bulldozers are then used to gather the blasted material. The extracted gravel undergoes a series of processing steps, including crushing to break down large rocks into smaller pieces, screening to separate different sizes, and washing to remove impurities and fines. The processed gravel is transported within the quarry using conveyors and then hauled to construction sites or storage facilities via trucks.
Gravel for concrete can also be sourced from riverbeds and marine environments through dredging operations. Riverbed mining involves extracting gravel from the beds of rivers using suction dredgers. This method, while effective, is regulated to prevent excessive erosion and ecological damage to aquatic habitats. Marine dredging, on the other hand, involves specialized ships equipped with dredgers that extract gravel from the ocean floor. This process must also comply with environmental regulations to minimize the impact on marine ecosystems. Both methods require careful management to ensure sustainability, as excessive removal of gravel can lead to habitat destruction, altered water flows, and increased vulnerability to flooding.
As I was unsurprised to find in my exploration of SCMs, it’s about what’s cheapest and closest in concrete. When 28 billion tons are involved, every extra penny per ton ends up with a lot of zeros behind it.
With all of this mass being blasted, dredged, crushed, and trucked, surely the carbon debt per ton must be high? Not so much, it turns out. All of the steps described above are mechanical, with no requirement for heat or pressure for chemical reactions. That means they are pretty low energy per ton compared to cement or steel. That in turn means that they are fairly low emissions per ton, about 6.5 to 7 kilograms of carbon dioxide per ton of sand or aggregate. But as noted, that’s multiplied by 28 billion tons just for those four big geographies. It’s still around 180 to 190 million tons of carbon dioxide per year.
Is there any solution for that? Yes, a couple. When we demolish buildings and infrastructure, we break it apart and salvage the steel. Increasingly, the crushed concrete that remains is being treated as a source of gravel, both for road work and new concrete. However, as I found when looking at Sublime, which wants to take the recycled concrete and leach off the cement using electrochemistry to make new cement, we don’t demolish nearly as much stuff as we build annually, so only about 2 billion tons of concrete are available. And aggregate reuse is clustered in the west as well.
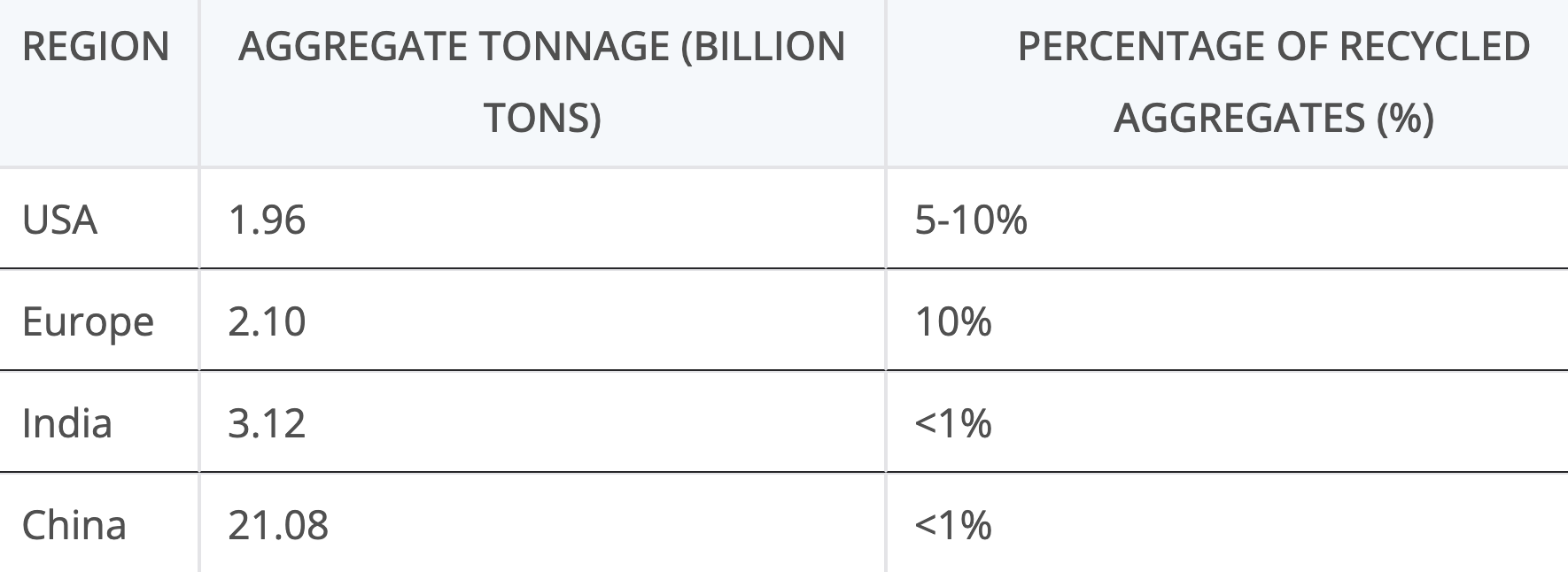
I spent some time errr… aggregating rough statistics on aggregate reuse from sources including the National Ready Mixed Concrete Association (NRMCA), the Portland Cement Association (PCA), the International Journal of Environmental Research and Public Health, the Environmental Protection Agency (EPA), and National Geographic. It’s rough and ready, but is sufficient for my purposes.
As the world moves forward, population growth ends somewhere between 2050 and 2070, and major geographies like China and India start recycling concrete more, it’s likely that a steady state of about 10% of aggregate coming from recycled concrete will become the norm. That’s good, but recycling concrete requires energy too.
Is there any solution for the energy emissions? Of course. Remember, all of this sand and gravel, regardless of natural or recycled source, just requires some chemical energy to blast it free and a bunch of mechanical energy to haul it around and crush it. Electricity is incredibly efficient at providing mechanical energy, and electricity can be decarbonized.
As sand and gravel extraction, crushing and transportation electrifies in parallel with electricity decarbonizing, this part of the concrete emissions problem will wind itself down relatively naturally. It’s not nearly the problem that cement and — foreshadowing — steel are for concrete emissions, and electrification will solve it.
Have a tip for CleanTechnica? Want to advertise? Want to suggest a guest for our CleanTech Talk podcast? Contact us here.
Latest CleanTechnica.TV Videos
CleanTechnica uses affiliate links. See our policy here.