Sign up for daily news updates from CleanTechnica on email. Or follow us on Google News!
Batteries for electric cars need to be compact enough to fit within the chassis. They need to be energy-dense to provide enough power to accelerate quickly. They have to be able to charge rapidly to satisfy the needs of drivers, but not so heavy that they make us feel like we are driving tanks. To satisfy all those criteria, batteries for electric cars almost always rely on some form of lithium-ion chemistry. Batteries for grid-scale energy storage don’t need to meet any of those criteria, however. Size and weight are relatively unimportant, as are energy density and fast discharge rates. That means they can use any number of chemistries that are not suitable for automotive purposes
“I think the market for longer duration storage is just now emerging,” Mark Higgins, president of Redflow, told Ars Technica recently. “We have a lot of… very rapid scale-up in the types of projects that we’re working on and the size of projects that we’re working on. We’ve deployed about 270 projects around the world. Most of them have been small off grid or remote grid systems. What we’re seeing today is much more grid connected types of projects.” Giovanni Damato, president of CMBlu Energy, added “Demand… seems to be increasing every day. We’re really excited about the opportunity to… just be able to play in that space and provide as much capacity as possible.”
New industrial markets are also becoming active. Chemical plants, steel plants, and metal processing plants have not been able to deploy renewable energy well so far due to batteries’ fire hazards, said Mukesh Chatter, CEO of Alsym Energy. “When you already are generating a lot of heat in these plants and there’s a risk of fire to begin with, you don’t want to deploy any battery that is flammable.”
Zinc-Bromine Batteries
Redflow has been manufacturing zinc-bromine flow batteries since 2010, Mark Higgins said. They do not require the critical minerals that lithium-ion batteries need, which are sometimes from parts of the world that have unsafe labor practices or geopolitical risks. The minerals for zinc-bromine batteries are affordable and easy to obtain. Flow batteries contain liquid or gaseous electrolytes that flow through cells from tanks. According to the International Flow Battery Forum, “The inter-conversion of energy between electrical and stored chemical energy takes place in the electrochemical cell. This consists of two half cells separated by a porous or an ion-exchange membrane. The battery can be constructed of low cost and readily available materials such as thermoplastics and carbon based materials. Many parts of the battery can be recycled. Electrolytes can be recovered and reused, leading to low cost of ownership.”
Flow batteries are manufactured differently than lithium-ion batteries. “I would say that our manufacturing process is much more akin to… an automotive manufacturing process than to [an] electronics manufacturing process,” Higgins said. “Essentially, it is assembling batteries that are made out of plastic tanks, pumps, fans, [and] tubing. It’s a flow battery, so it’s a liquid that flows through the system that goes through an electrical stack that has cells in it, which is where most of Redflow’s intellectual property resides. The rest of the battery is all… parts that we can obtain just about anywhere.”
The charging and discharging happen inside an electrical stack. In the stack, zinc is plated onto a carbon surface during the charging process. It is then dissolved into the liquid during the discharging process, Higgins said. The zinc-bromine electrolyte is derived from an industrial chemical that has been used in the oil and gas sector for a long time, he added. The battery cannot catch fire and all its parts are recyclable. “You don’t have any of the toxic materials that you do in a lithium-ion battery.” The electrolyte liquid can be reused in other batteries. If it’s contaminated, it can be used by the oil and gas industry. If the battery leaks, the contents can be neutralized quickly and are subsequently not hazardous.
“Right now, we manufacture our batteries in Thailand,” Higgins said. “The process and wages are all fair wages and we follow all relevant environmental and labor standards.” The largest sources of bromine come from the Dead Sea or within the United States. The zinc comes from Northern Europe, the United States, or Canada. The flow batteries typically undergo an annual maintenance program to replace components that wear out or fail, something that’s not possible with many other battery types. Higgins estimated that two to four years down the road, this technology will be “completely competitive with lithium-ion” from a cost perspective.
Redox Flow Batteries
CMBlu Energy is beginning to take commercial orders for its Organic SolidFlow batteries, Giovanni Damato said. It has already deployed several smaller systems in Europe, and recently announced a partnership with Argonne National Laboratory and Idaho National Laboratory to study how these batteries can be used in microgrids. Organic SolidFlow batteries are redox flow batteries with a twist, he said. They have stationary solids in their tanks, which increases their energy storage capacity compared to conventional flow batteries. They use organic polymers that hold and transfer charge. The polymers can be sourced from anywhere, which means they do not need materials that come from conflict countries that have unsafe working conditions. That means cobalt.
The batteries are designed in modular units that are about the same size of a standing desk, with four battery stacks connected in series. Each cell in the stack has a membrane that separates its two electrodes. The number of cells in a stack can be customized. A module weighs around two tons and supplies power for 5 to 10 hours. Thermal runaway is not an issue with this redox flow battery because of its inherent chemistry and the fact that it uses an aqueous solution, Damato said.
For maintenance, CMBlu Energy recommends regular visual inspections, including checking the pumps and valves and looking for leaks. The maintenance requirements are relatively minimal. Some of the performance monitoring for leaks is automated, as is data collection on pressure and temperature. The electrolyte needs to be rejuvenated approximately every 10 years, depending on the environmental conditions of the installation. Since the batteries are made of plastic, they can be recycled similarly to other plastics. Damato said this is cost effective. The support structures and copper wiring are also recyclable, as are the solid and liquid electrolytes.
Sulfur Sodium Batteries
BASF SES is selling a sulfur sodium battery made by Japanese manufacturer NGK Insulators. That battery has sulfur as the positive electrode and sodium as the negative one. The electrolyte is a beta-alumina ceramic tube. While the battery discharges, the sulfur is reduced to polysulfide, and the sodium is oxidized. The process is reversed during charging. When the battery is in use, it runs at around 300° C, with both the sodium and the sulfur in their liquid state. Justin Williams, senior account executive at Trevi Communications, told Ars Technica, “Beta-alumina solid electrolyte (BASE) is sodium polyaluminate. The material has a specific crystal structure [that] enables very fast ion transport. It is used as an ion conductor with high selectivity.”
The batteries are packaged in 20-foot-long shipping containers that have six modules inside. Each container provides 1.45 MWh of storage and the containers are usually used arranged in groups of four. The technology does not make use of any of the critical minerals that are problematic in lithium-ion batteries. In addition to sodium and sulfur, NGK Insulators uses oxygen, steel, carbon, and silica-based materials, all of which are inexpensive and widely available.
The safety tests for the NAS Battery included short-circuiting the modules, putting the modules in fires, and submerging them, none of which caused leakage or fires. Lighting an individual cell on fire resulted in similarly safe results. A drop test showed that only the enclosure was damaged, and no fire or leaks occurred. “When we’re talking about climate resiliency, the battery can withstand a great deal,” Brannock said. She mentioned that it tolerates heat and cold as well as high salinity environments. The container also gives it a layer of protection.
The Takeaway
All of these alternatives to traditional lithium-ion batteries are bulky and heavy, but they also only use materials that are readily available and inexpensive. As a group, they have a low risk of fire and environmental damage if breached. Inexpensive long-duration energy storage will be critical to making the transition to renewable energy, especially for industries that operate 24 hours a day. Today, the last resort for making electricity during off-peak hours is usually methane-fired generating plants. Long-term battery storage systems will finally allow us to shut those facilities forever.
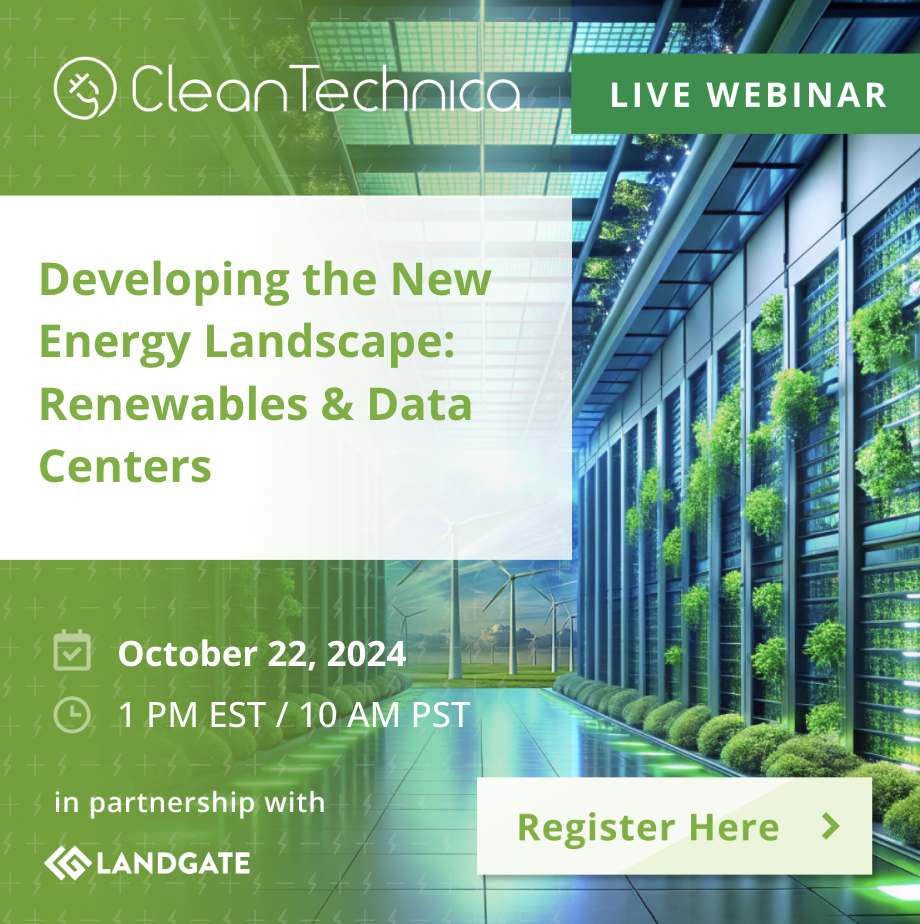
Have a tip for CleanTechnica? Want to advertise? Want to suggest a guest for our CleanTech Talk podcast? Contact us here.
Latest CleanTechnica.TV Videos
CleanTechnica uses affiliate links. See our policy here.
CleanTechnica’s Comment Policy