Sign up for daily news updates from CleanTechnica on email. Or follow us on Google News!
Under the auspices of the India Smart Grid Forum, the think tank founded as an umbrella organization over India’s 28 state utilities to provide thought leadership, share leading practices, and bring international insights to India, I’m delivering bi-weekly webinars framed by the Short List of Climate Actions That Will Work. With the glories of online recordings and AI transcription tools, it’s relatively easy to share both the transcript and the slides that I used, so I’m making a habit of it.
Most recently, I delivered a talk and held a Q&A session covering my thoughts on the decarbonization of industry, something considered hard to abate but which in reality is just somewhat expensive to abate. For those who prefer talk-talk to read-read, here’s the recorded video of the presentation and discussion:
Reji Pillai (RP): Good morning, good afternoon, good evening to all the participants from around the world and big welcome. Thank you to Michael for doing this series with the ISGF. So today’s topic is not my area of expertise. I’m not going to delve anything deep into it. You always hear about hard to abate sectors, the industrial sectors which are hard to abate from the emissions. So Michael will be talking about that. There are technologies, but at what cost? And you also hear a lot about many of the new esoteric solutions and on hydrogen particularly we will be doing a separate session during the series, so there will be about 15 of them, and this is the fifth one. And sorry about last fortnight we had to miss because I’ve been traveling and the next one will be on 4 July. So without any further delay handing over to Michael.
Michael Barnard (MB): Thank you, Reji. Thank you, ISGF. As always, I’m privileged to be given the opportunity to assist India, one of the great countries in the world to thread the intersection of increasing affluence and reducing carbon emissions. It is possible. I keep finding other areas where India is doing very well. I’ll talk about one of those today, but that doesn’t mean we can’t all do better. So this session is about industrial processes. As was mentioned, we’ve been dealing with where is the energy coming from? How is it moving around? How do we make sure we have enough of it at different times? And there are answers for all those questions in previous discussions. Please feel free to go back on those. But this one is about what’s termed hard to abate.
And it’s not really all that hard to abate. We just have to have the will and find the money. We also have to price carbon. So I’ll be talking about this. I have relatively few slides, but they’re pretty dense. So my apologies for that. Let’s go through each one of them fairly carefully, and hopefully then at the end, we’ll have a lot of time for questions.
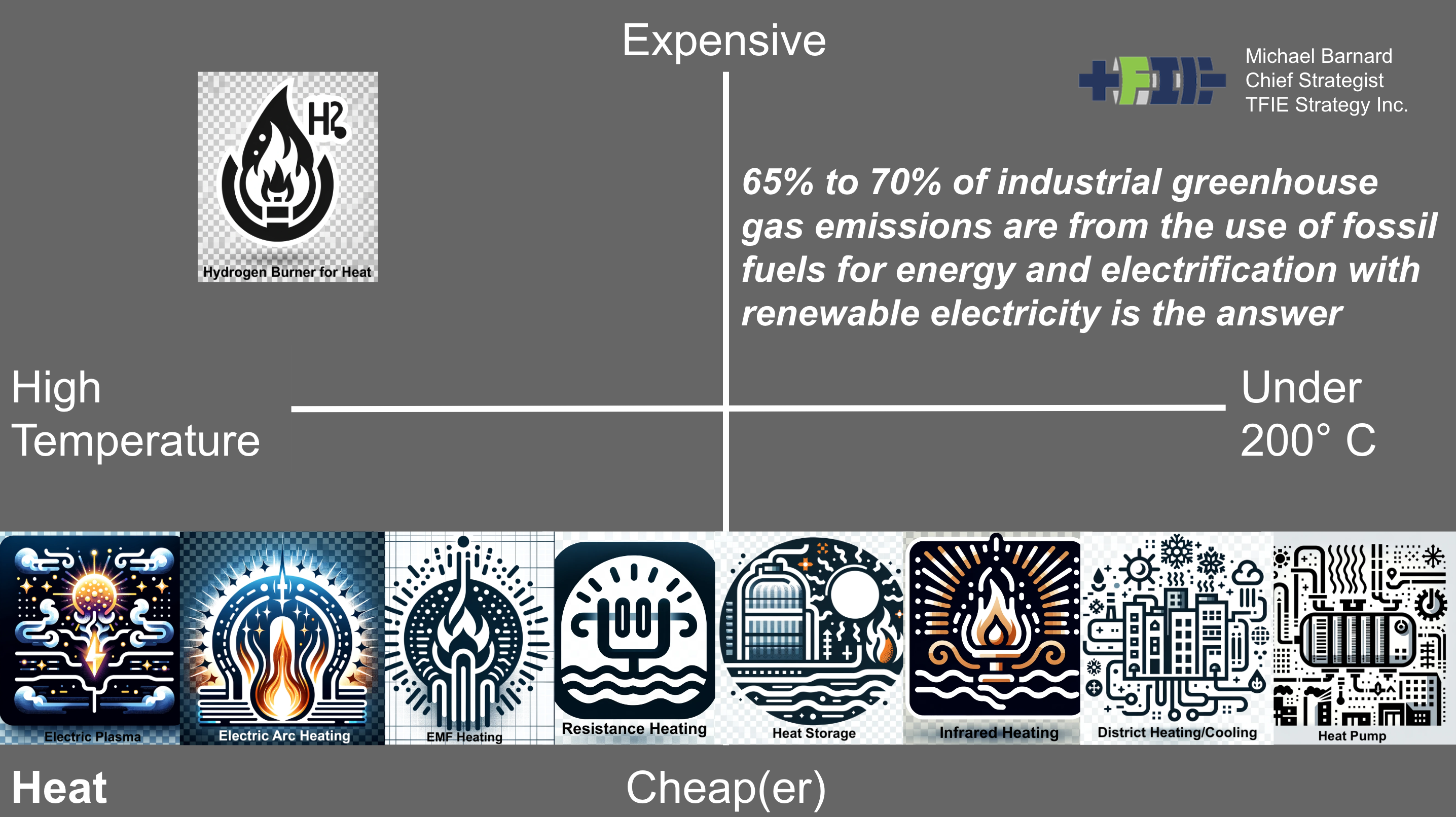
Okay, let’s start with the big hitter. In industrial emissions, most of them come from burning fossil fuels, 65% to 75%. It’s just process heat. It’s creating the heat that we require for a whole bunch of other stuff. And as we move forward, we’ve got a whole bunch of answers. One of them is just a selection of technologies across the bottom, and I’ll talk about those.
But another is where right now it’s cheapest to use a heat based process in the future. As we move away from heat, the question becomes, what other processes could we use that would actually reduce our energy requirements? One of the things I’ll say that’s not on the slide is electrochemical processes, on average, use about 50% of the energy of heat based chemistry processes. You can benchmark that with hydrogen, can benchmark that with a few other things, but that’s kind of something to keep in mind. So our energy requirements, as we shift to electrochemical solutions in many cases diminish substantially. It’s also worth noting that we’re pretty inefficient in our use of heat because fossil fuels are so dirt cheap, so we just kind of burn more fossil fuels at operational expense instead of making the processes more efficient.
This is one of Reji’s points, a place where people keep thinking hydrogen is required. One of the key pieces of inaccurate information that people seem to hold onto is that electricity isn’t good for high temperature heat, and so we’ll need hydrogen. And that’s completely false. As I look at documents around the world, one of the amusing things I find is in the same big, like, 100 page federal strategy from the United States, in one place they’ll say, and we use electric arc furnaces for steel in temperatures of 1500 to 3000 degrees. And then later on they’ll say, and we need hydrogen for anything over 200 degrees Celsius heat. It’s just very easy for people to have this odd idea that we can’t do it with electricity.
Recently, I spent some time recording a podcast with Paul Martin, a chemical process engineer with 30 odd years of building for clients globally, new modular chemical processing plants. Plants that require temperatures of all levels. And he shared with me that in his dozens of plants for over 30 years, designing them, prototyping them, building trial ones, in the test and trial phases, he had to use a flame exactly once. There was one process in over 30 years that actually needed the characteristics of a flame, and everything else was completely, adequately met by electricity.
As we kind of go through this, we now have 200 degrees is an interesting point. 40% to 45% of all industrial heat is below 200 degrees Celsius. And so that means what? Oh, heat pumps are completely fit for purpose for 40% to 45% of industrial heat requirements.
That means the efficiency of heat pumps are there as well. As a reminder, one unit of electricity into a heat pump turns into three units of heat. So for 45% of all industrial heat, our energy requirements are actually going to plummet by two thirds. That, once again, makes it much easier to build the renewables required to deliver that energy.
Infrared heating is another. It’s one of the spectrum of ways we can deliver heat for different processes. We all have seen infrared. There’s infrared saunas. But industrial processing, sometimes you need that radiant heat, and we can deliver it through electrical means.
This is actually a place where heat storage becomes very strongly viable as well. Sometimes hard to integrate into an existing plant, but very easy to build into new plants. We’ve now got multiple heat storage technologies. They’re cheap. They allow you to shift the operational expense of energy to low cost evening nights and early mornings, and then deliver that energy in the form of heat, where process heat is required during the day. During operational things, heat storage doesn’t necessarily work as well for 24 7365. Industrial processes. But for anything where there is a day shift and night diminishment of activity, you can arbitrage electricity rates for heat storage, for processes that require heat. There is one place that heat storage tends to get over its skis, and that is that heat storage is not suitable for storing electricity to be returned as electricity, just simply because the exergy losses means that if you put something into heat storage and bring it back as electricity, you’re only getting about a third of the electricity back. Not for that purpose.
However, I’ve been convinced over time by various people who designed these things that if you need 95% heat and 5% electricity, sometimes the cheapest way to provide the electricity is to use the heat store and get inefficient electricity out of it. Anybody who has any heat storage solution which leads with electrical storage for return of electricity, look at them suspiciously. But there’s lots of great ones out there. Rondo out of the United States gets it right. Sand, water bricks, carbon bricks, all sorts of technologies are there. They’re all very simple. And to be clear, you can get heat storage at hundreds of degrees as well.
Resistance heating, this is just the same stuff as you have on an electric stove that isn’t an induction stove. Electric stoves simply, they just heat up a coil like an old incandescent light bulb. We have heat technologies up to six to 700 degrees Celsius with resistance heating. Kanthal, a northern European company, provides that technology to industrial sites globally. Once again, resistance heating fit for purpose up to hundreds of degrees Celsius.
Then we get into electromagnetic frequency heating, which includes induction heating. So many of you probably have induction stoves, they’re much more common outside the west, which has about a bunch of gas and other stoves. With induction stoves, we induce magnetic currents in ferrous materials and get even higher heats of specific characters. We just have to design for them.
Next is electric arc heating, which I’ve mentioned before, up to 3000 degrees Celsius. We already use it globally for electric arc furnaces. I’ll be talking more about those later. But it’s also used for a whole bunch of other stuff. It’s just entirely possible to achieve these kinds of temperatures required.
Then finally we get to electric plasma. Now, an electric plasma is like a flame produced from electricity, if the flame is the temperature of the sun’s surface, up to 10,000 degrees Celsius, a strict cloud of very hot gas created with electricity. That’s very useful for a whole class of solutions. It can be hard to work with, so it’s not trivial to use it, but it’s entirely viable.
Sometimes we hear from industrial users and from industrial heat people, but they’re not ready commercially. And the answer there is, you have to separate commercialization into two categories. Are they technically ready? Are they available and available from commercial producers? And the answer for all of these technologies for that is, yes, these are fit for purpose industrial solutions. The second one is, are they commonly used industry at the same scale as burners of fossil fuels? And the answer is no. We are completely able to scale these technologies and deliver these technologies at the scale needed to completely electrify heat. We just haven’t yet.
That gets to the question of why? Well, because it’s much cheaper to burn fossil fuels when we can use the atmosphere as an open sewer. As soon as we change that dynamic through some combination of carbon pricing and regulation, so that it becomes more expensive to use heat from fossil fuels, then these all become cost competitive. In many cases, the cost competitiveness is quite easy to achieve. I mentioned the heat pumps. If you’re using a third of the energy to create the same amount of heat with heat pumps, then that’s a low hanging fruit situation for industry. You know, that they’re not doing. It is simply reticence to adopt stuff that’s new.
There are challenges. To be clear, some of those challenges are capital expenditure. Changing your process means you have to spend a bunch of money on new equipment to get this working. Then there’s operational expenses, dirt cheap fossil fuels, versus typically more expensive electricity. That requires changes.
Then there’s the cognitive ones. A lot of people in industry, what happens is they say, okay, I have to decarbonize my industrial processes, and they turn to their supplier of gases or solid fuels, and they say, hey, Sid, tell me, Sid, what are you going to give me to burn that is low carbon, and that’s not the right frame. The right frame is, hey, Sid, and all other suppliers, including electricity, what is going to provide decarbonized energy that I require for my industrial processes? It’s easy for people to get stuck in that space where they think they need something to burn, when in actuality they don’t.
There are assertions from industry that these aren’t ready for prime time, that they’re not suitable for their process. That’s false. But it’s easy for them to hear from their suppliers, like Sid, who sells natural gas to industrial processes, oh, well, we’ve got you covered with blue hydrogen or renewable natural gas, you’re covered. It’ll be great and it’ll be cheap. None of those things are true. Renewable natural gas will be more expensive, hydrogen will be a lot more expensive. Hydrogen brings its own complete set of capital and operational expense problems with it, as well as, you know, increased risks and stuff like that. So as I look across this space, I’ve been looking for years for any place where I couldn’t use electricity to solve an industrial heat problem, and I’ve not found one. As I said back to Paul Martin, 30 plus years of experience building chemical processing plants, once he had to use a flame.
This is not a hard problem to solve, and that’s 65% to 75% of industrial emissions. Now, to be clear, that’s a lot of power to deliver and a lot of energy to deliver to industry. In some cases, where industry is located now is because it’s convenient to get fossil fuels. In the future, new industrial sectors will end up being set up where it’s easy to get cheap electricity from renewables. The outback of Australia, where you’ve got lots of wind and lots of sun, and it’s easy to set that up. Some processes are going to start evolving into different locations based upon where there’s lots of wind and solar, but that’s a transformational thing over time. And some industries can’t move like you can’t move cement. Cement is so big and heavy that you have to make it very local to where you need it, so you’re not going to move that around. But I have answers for cement. Okay, enough on heat.
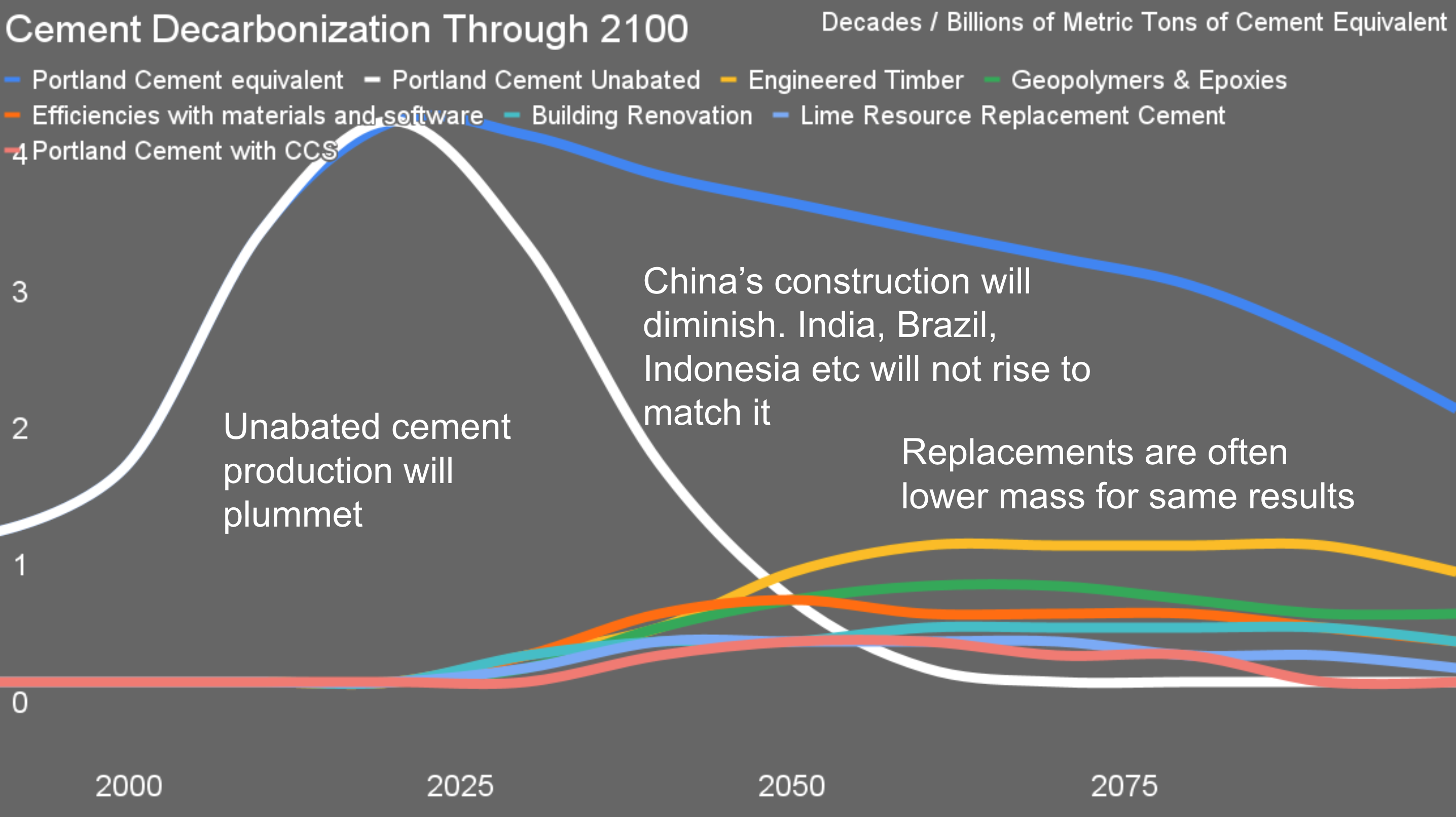
I mentioned cement. So this is a chart of cement manufacturing from 1990 through the present. About 4.1 billion tons of cement were manufactured last year, and that’s about the same as 2020. By the way, the curve is incredibly steep. That curve is one we’ve seen with steel, it’s one we’ve seen with a whole bunch of other stuff. Since 1990, we’ve started manufacturing four times as much cement globally. And cement’s a big climate problem. Every ton of cement comes with almost a ton of carbon dioxide. Because of manufacturing, most of that comes from decomposing limestone into quick lime (calcium oxide) and carbon dioxide.
The nice thing about decomposing that in a kiln is the waste is carbon dioxide and it just goes up and it disappears into the atmosphere. Obviously not a great solution now that we understand the problem. But it’s also hard to get around as we think about limestone. It’s old seabeds, basically. All the shellfish shells drifted down to the bottom over millennia. In millions of years, some calcium carbonates, bicarbonates precipitated out of the water and drifted down to the bottom. And then that was compressed and then was lifted up. Because it’s old seabeds, limestone is available pretty much everywhere on earth, pretty conveniently, in layers potentially hundreds of meters thick and tens or hundreds of kilometers long and wide.
It’s under a lot of the ground on every continent, which means that if we need it it’s easy to find because it’s a sedimentary rock. It’s not that hard, so it’s fairly easy to quarry. Because it is a rock the quarry’s walls stay upright, which is nice. You don’t have to shore up the walls particularly. And then decomposing it requires 900 degrees Celsius heat. Back to the heat problem. Now, this cement decarbonization is interesting because this is a place where the emissions from the process heat are overwhelmed by process emissions from limestone. Remember, limestone turns into lime and carbon dioxide. That carbon dioxide is a lot. It’s very hard to get around that.
Manufacturing cement is probably eight to 10% of global carbon dioxide emissions. More if you count the use of natural gas with its methane leakage, which we’ve been focusing on a lot recently. You’ll notice this blue curve here. This curve is my projection of the equivalent of that billions of tons, metric tons of cement. When I say the equivalent, I mean we are going to replace cement with other solutions. In many cases, those solutions are lower mass for the same result. What that means is this is not going to have to add up to billions of tons in the same way.
The second thing that’s important is this is diminishing. The question to ask is why is this curve diminishing in my perspective, and it’s for a few reasons. Most of this growth from 1990 to 2020 was China. China manufactured 2.1 billion tons of the 4.1 billion tons of cement manufactured globally last year. But China is approaching the end of building all of the infrastructure and cities it requires for its 1.4 billion people. And its population is flat. Its ghost cities are now filling up, but they’re not full. It has substantially urbanized its population. It’s built 45,000 kilometers of high speed rail, 177,000 highways, cities for the majority of the inhabitants who will end up in their spaces. It’s at 59% of shipbuilding globally, which means all the shipyards, those massive shipyards, are built. It built the Three Gorges Dam and many other dams. It has one major dam up in the mountains under construction that dwarfs the Three Gorges.
The rapidity of growth that’s tailing off. China will start moving into a country that is not building nearly as much infrastructure internally, so its cement demand and other demands will diminish. At the same time, India, Brazil, Indonesia, and the rest of the developing world are going to increase their demand, but not at the rate that China did between 1990 and 2020, and not to the same degree. They’ll pull a lot more of the levers for reducing and replacing stuff. So this curve is the equivalent. But you’ll notice how rapidly actual Portland cement (the white line), the primary problem, the stuff made from limestone, declines while these things, these curves at the bottom, increase slowly over time.
You’re actually the first people, audience to see this. I finished this projection yesterday, and so this is the first time I’ve spoken to it, but it’s been a long time in the making. I spent the last month on concrete.
This curve is engineered timber. Engineered timber basically cross laminates thin sheets of ply a few millimeters thick with epoxy, and turns them into engineered beams, hardwood floors, and fully load bearing floors, and full walls. In buildings, you can actually do a full mass timber construction and replace most of the concrete, only requiring the foundation to be made with concrete. It’s permitted up to twelve stories in Canada and in Sweden they have no limit as long as the buildings are structurally sound.
They engineer timber beams to replace the load bearing structures of reinforced concrete, and they do it with a fifth the mass, because engineered timber is so much stronger than reinforced concrete. You actually replace five times as much cement and concrete with just the engineered timber load bearing structures. That’s why this is a big replacement for all of this. And it’s available in most parts of the world right now. We extract 3.5 billion wood products globally, and we waste a lot of it on single use paper products, which are better in some ways than single use plastic products, but not as good as multi use products. My projection is we’ll end up displacing hundreds of millions of tons of current timber extraction and shift to more sustainable timber extraction, and that will in turn displace five times as much cement and concrete.
One other thing about engineered timber, you can use it in hybrid buildings where the load bearing structures are reinforced concrete, and all of the walls and floors are mass timber. With that, you’re still getting 50% concrete and cement savings. With a full mass timber solution, you’re getting 70% to 80% concrete and cement savings, because the foundation is still reinforced concrete.
For now, geopolymers and epoxies are my next big lever. Geopolymers, basically we take right now coal generation fly ash and blast furnace slag. We grind them up and we mix them with alkaline substances and silicate substances. Potassium hydroxide and potassium silicates is one of them, and sodium hydroxide and sodium silicates are another. You mix them together and they turn into a long chain polymer, which in turn is stronger and better than cement in many ways. You just take the aggregate and you take these geopolymer precursors, mix it all together, you add the alkaline substances and the silicate substances, and it turns into this very solid thing with no cement. There’s no limestone involved in this process. And because we can actually use biomass ash, I have become more bullish on this right now. We’ve got a lot of fly ash from coal plants globally. We’re still generating a lot of it. We have a lot of blast furnace slag and we’re still generating more of it. Less in, you know, the west, more in the developing world. I’ll talk about equity in a minute.
But then there’s also copper slag, there’s also red mud from aluminum, and then there’s also biomass. One thing that India is doing, which is very interesting, is rice hulk ash. India is a leader in using biomass from agricultural waste, from rice production, from the paddies, to burn it underneath clay brick kilns. And so then you end up with this rice hulk ash, which can be used in geopolymers. Rice hulk ash is high in the silicates that are necessary for the creation of the long chain polymers that come with geopolymers.
Epoxies are made from oil. They’re a petrochemical, they’re more expensive. But once again, you know, using petrochemicals is fine as long as you’re not burning them. And if we turn some oil into some glue and use that to displace cement, that’s a much more virtuous cycle than others.
So these, by the way, the engineered timber, tremendous amount of that available in the developing world. More in the developing world in many cases, than in the developed world. Geopolymers and epoxies, tremendously available resources between waste from blast furnaces and coal plants, and rice hulk ash. As noted, it’s strongly available in the developing world as well.
Next is efficiencies of materials and software. One of the key things is if we take, for example, carbon fiber and use that with Portland cement instead of, or in a slight addition to the reinforced steel, what we can do is get a much stronger concrete process with a lot less concrete and cement reinforced. So carbon fiber reinforced concrete is actually much lighter and thinner for the same structural properties. And that’s actually something that can be designed in.
Similarly, we’ve got replacements for steel mesh in concrete. Reinforced concrete slabs with fiberglass, and fiberglass and carbon fiber are things that can be decarbonized. They enable us to do certain classes of things with concrete that are easier and cheaper in process perspectives.
The software is software that everybody in the developed world can use. It’s all available stuff. Finite element analysis and generative architecture. As I say, there are no flies on the engineers and architects in the developing world. They have the tools to do stuff a lot better and more efficiently than the United States and China did from 1990 to 2020. So, as the ramp up occurs in the developing world of infrastructure, the materials use will be much more efficient because of the software tools that are available, and many more high tech materials will be used to reduce the overall infrastructure build.
Building renovation is the next one, as we have built so many buildings. Let’s take China as an example. As they built so many buildings and they are not increasing their population, the question becomes, do they tear down and replace a building, or do they just repurpose it in the first world, right now, just look at Calgary, for example. Calgary is the capital of the oil sands in Canada, and they built a lot of buildings for a whole bunch of firms that were oil sands extraction firms. Well, and now that industry is compressing and consolidating. And so there’s all these office buildings that are untenanted. In Calgary, last time I had a count, there were 19 office buildings. There were often 20 and 30 stories that had nobody in them because there were only a handful of head offices left after the consolidation. And they’d automated so much stuff, not doing nearly as much exploration.
So now Calgary is turning them into housing. It’s converting an existing building into condos and apartments. That becomes a reuse process in the building renovation and reuse universe. They say the lowest carbon building is the one that’s already built. We’ll be doing a lot more of that over the coming decades instead of tearing down stuff and building new stuff. That’ll help.
Then there’s lime resource replacement cement. There’s kind of two aspects to this. One is there are processes out there that can take existing concrete and get the cement out of them that’s already emitted all of its CO2 and then reactivate it in a similar way to the way that limestone is processed, and then return new cement from recycled concrete. So I expect that one to do so.
And then there’s lime bearing rocks like basalt, dacite and diabase, which have a lot less lime than limestone. Limestone beginning with lime is kind of a clue as to the ratio. It’s 56% lime, 44% CO2. But for some cases we’re going to be able to say, oh, in this case it’s cheapest, not many cases, to use basalt because we have a big source of basalt here and a big quarry, and we’ll just accept that we’re going to get a lot more waste rock, which we’ll find some uses for in some cases, and some more expensive cement. But it’ll be low carbon because basalt diabase and dacite site don’t have carbon. So as they decompose into lime, which is useful for cement, and some silicate rocks, which we can use in some ways for supplementary cementitious material.
Finally down at the bottom here, carbon capture and sequestration. I just finished the assessment of carbon capture a few days ago, which will be necessary to be able to do this in perhaps 5%. It will make economic sense to electrify the heat or cement and then capture the relatively pure CO2 stream carbon dioxide stream from the cement kiln and put it somewhere. Not for the entire thing, though, because we don’t really have infrastructure to put away 4 billion tons of carbon dioxide. When a cement plant, on the other hand, is right beside a sequestration site, an electric heat is used. So it’s pretty pure carbon dioxide that’s coming out, it will probably make sense to shove the carbon dioxide as long as the sequestration site is good for decades of output of the cement plant. In that case, it’ll probably pencil out.
But otherwise, all these other options, avoiding cement entirely with engineered hardwood moving, avoiding cement with geopolymers and epoxies. Avoiding cement with new materials and software tools. Avoiding cement by reusing buildings we’re already using, and avoiding new cement by lime replacements. Those all make better economic sense. And so that’s kind of the story for cement decarbonization. This line is indicative of the decarbonization curve. So it’s a good news story. This is entirely viable with technologies we have in hand today.
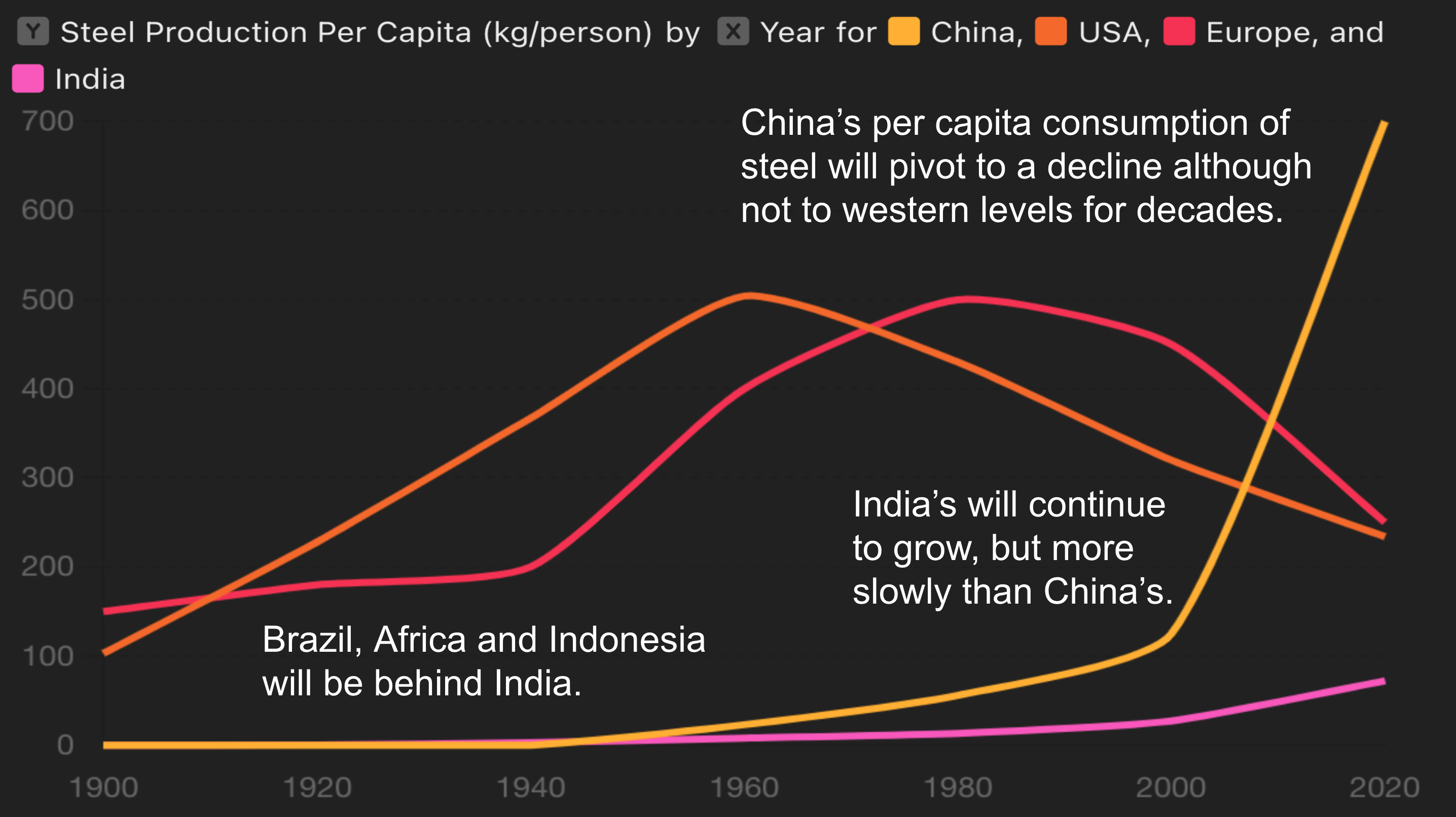
This is another chart I just developed recently. This is about steel, because we’re pivoting to another major industrial topic. This one just says, look at the West, United States and Europe, and their massive decades long steel manufacturing, and then the decline. This curve is China since 2000 and India at the bottom. Now China is going to pivot. One of the big equity questions is, how can the west say to the developing world, don’t do what we did? And from 1980 to 2020, China has made itself incredibly affluent. India is making itself quite remarkably affluent without nearly as much steel as China. About 90 kilograms per capita right now, still well below the west. Well, all those things I talked about, the decline, reduce the amount of cement we require, will also reduce the amount of steel that’s required.
And so a lot of the replacements now with modern technologies, which are easier to decarbonize, and decarbonization of steel itself, make this equity chart a much more palatable story for how to avoid doing this big hump in the middle and how to avoid doing what China ended up doing. For the most part, India is going to develop more. China is going to pivot because it’s finished with its infrastructure, which is a huge consumer of steel. It’s still going to be building lots of ships, cars and stuff. So it needs steel for that, but a lot less. And then India is not an export economy. It’s much more of a domestic manufacturing economy.
Brazil, Africa and Indonesia will be behind India and aren’t going to be building the same degree, the same scale of infrastructure as quickly and will not be building the manufacturing capacity that China built because it’s unnecessary in a world where population peaks between 2050 and 2070. So there’s a good news stories in terms of some of this stuff, but people in the west don’t really love this chart because it’s a century of us emitting carbon.
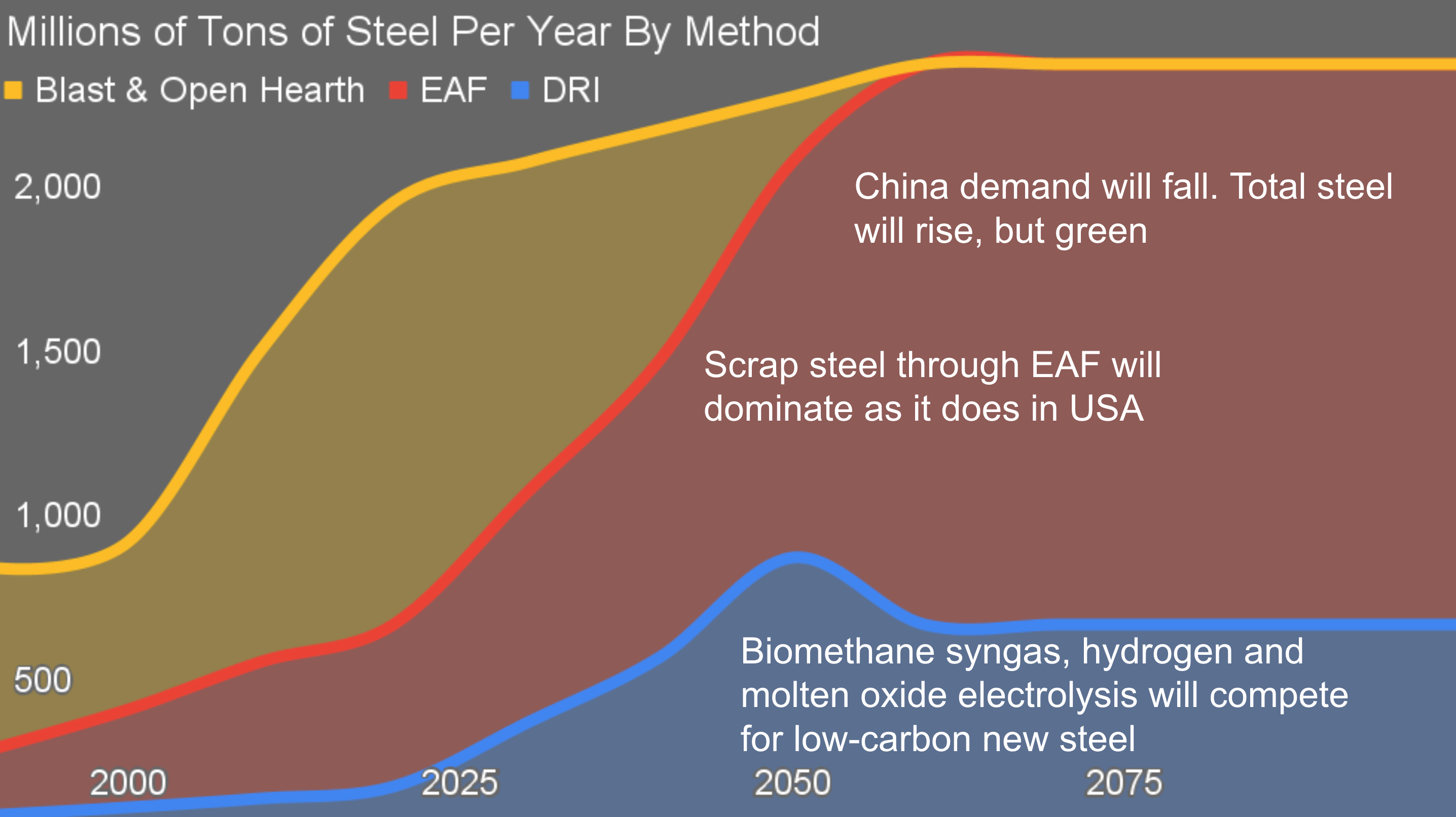
Okay, so this is the steel story. This one I did a year and a half, two years ago, I think my first version. So there’s another great news story. So this is how many? 2 billion tons of steel. 1990, we’re under a billion tons. So we’ve doubled it in that period of time. Once again, that steep curve was mostly China. China right now once again produces half the steel manufactured in the world. In 1980, the United States and Japan were the two biggest manufacturers and consumers of steel. Now they’re third and fourth. India is now the second biggest manufacturer of steel, after China. India is only manufacturing a 10th of the steel that China is. So that peak that’s going to slow substantially because a lot of that steel is going to infrastructure.
As noted, India, Indonesia, Brazil, Africa will be accelerating their steel demand. But we have some tools there as well. It’s a much simpler story, thankfully, than cement. As we look at this, I’ll just start with there’s new steel and then there’s scrap steel. Now, right now, the United States has 71% of its steel demand met by scrapping steel in electric arc furnaces. They’re not perfect, they use natural gas from preheating. But that’s electrifiable. And that is likely to be where the range that everybody moves into over time. As we get to the end game, I expect 75% of demand will be met as we scrap steel, appliances, cars, pipelines, refineries, oil tankers, and turn that into products, which are infrastructure products and consumer products, and then feed that cycle, which still means we need 25% new steel.
And note that 25% is not that much below total demand in 1980. But we have multiple technologies for that as well. This is all blast furnace and open hearth furnace. But down here in the direct reduction stuff, we already have Midrex and ArcelorMittal syngas DRI technologies, where biomethane synthetic gases can be used to reduce iron into iron ore or reduce iron ore into iron, basically de rusting it. We can do that with biological sources of methane. That’s also amenable to that hydrogen process that Hybrit has been doing. There’s also the molten oxide electrolysis process. So we have three different decarbonization technologies. For steel, biomethane syngas is commercialized and available today. It’s just a bit more expensive. Hydrogen is commercialized and available today. Molten oxide electrolysis is the only one that isn’t a commercial product yet. But there’s multiple people working on it, and the provenance is very strong. I’m not sure which one of these will dominate. It’s going to be interesting to see which one will dominate, but I’m comfortable that steel is actually a very solvable problem. Once again, process heat from electricity. And we’re talking about what will be used for the chemical process of reduction of iron ore to iron, not the heat requirement. Okay, Reji mentioned hydrogen.
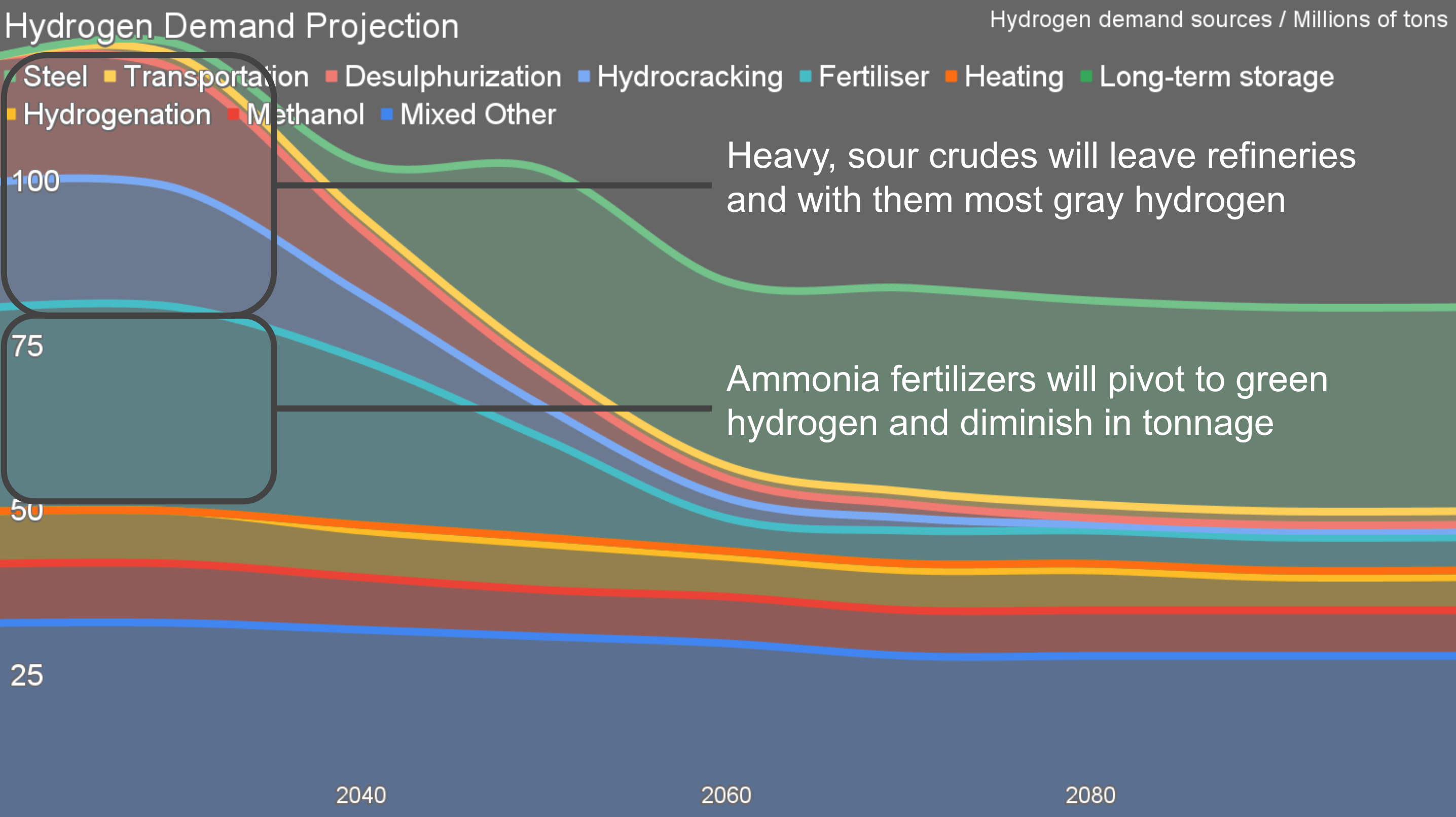
I’ll just mention some industrial places that are big sources of emissions today. So this box is all the use of hydrogen in refining crude oil. It’s used for hydro cracking, which is turning heavy oils into lighter variants. And it’s used for hydro treating, desulfurization, which takes impurities out of the crude oils, like sulfur. Alberta’s and Venezuela’s products are heavy sour crudes. They have lots of bitumen, lots of sulfur. That’s where most hydrogen is used. As we move forward with the reduction with peak oil demand, which is during this decade, according to the International Energy Agency, the first crudes that will be off the market will be the heavy sour crudes.
It’s not good news for the industries and governments of Venezuela and Canada in terms of that portion of their economy, but why would people pay more when the world is awash with light sweet oil that’s close to water and cheap to get? So as we move forward, the heavy sour cruise will be off. And the hydrogen demand, which is a full third of hydrogen demand today, will go away. And all the emissions from that hydrogen demand will go away.
Similarly for ammonia fertilizers, right now we make them from coal gas and natural gas. We strip the hydrogen out and we put the hydrogen into the Haber-Bosch process to make ammonia, which we combine with various things to make fertilizer, which is necessary. But we have a lot of levers, which I won’t talk about at length to reduce this. Precision agriculture, low tillage agriculture, some biological processes. My projection has us diminishing the amount of fertilizer we require.
And of course, we’re going to be providing hydrogen for that with green electricity. All very simple technologies. all very well commercialized today. This is not rocket science. It’s just a bit more expensive, and some of it is a lot less expensive. Using drone based seeding and spraying is a lot cheaper with better crop outputs.
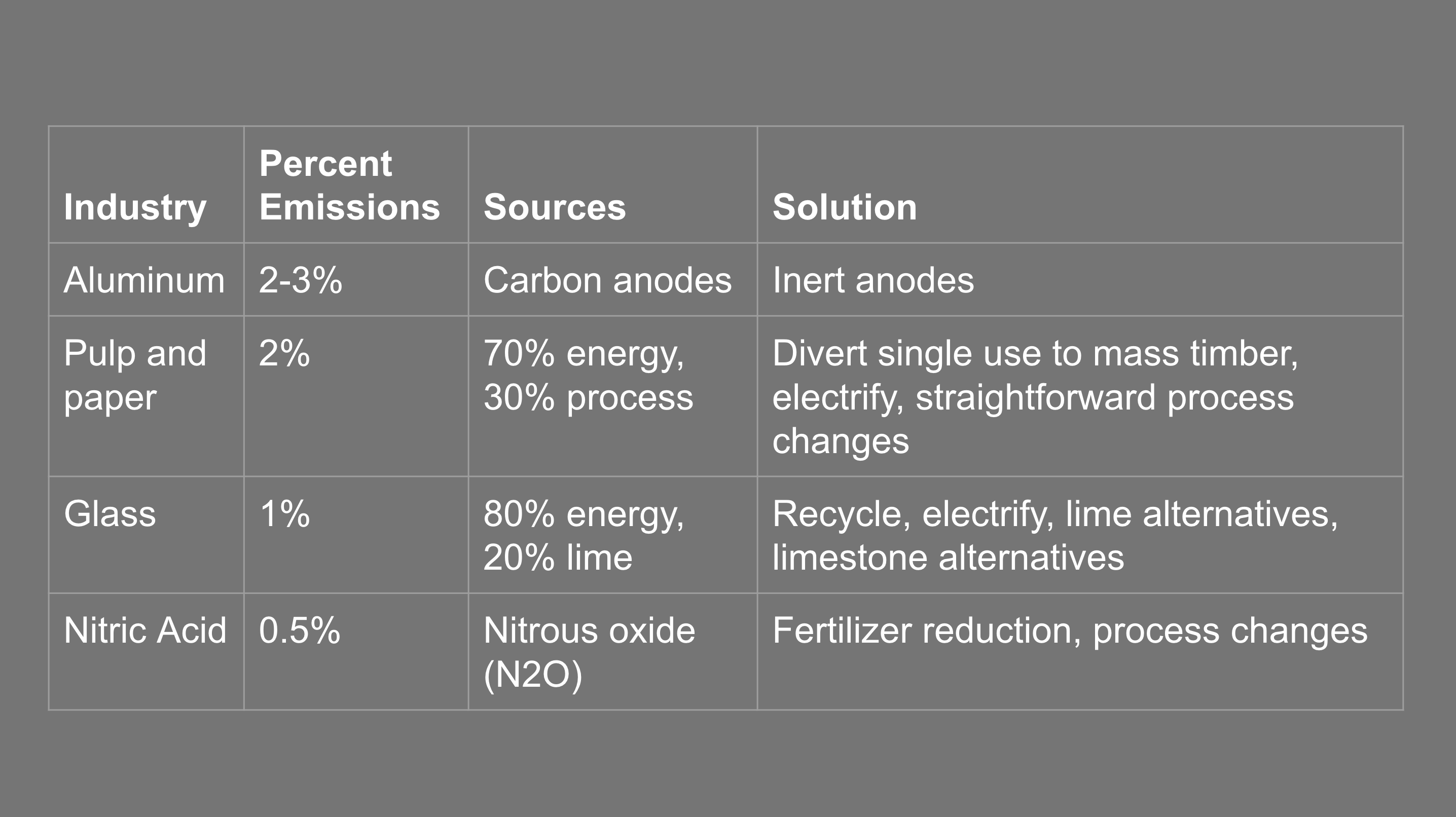
Okay, last slide. Other industries. So aluminum, two to 3% of global emissions. That’s because we use carbon anodes, which get consumed and turn into carbon dioxide. When we use that electrochemical process with aluminum, with bauxite ore and other things, the alumina that comes from bauxite ore, that we turn into aluminum, and we’ve got inert anodes that don’t get consumed or that if they do get consumed, don’t turn into carbon dioxide. We’ve got a solution for this. This is not rocket science.
It’s just once again a bit more expensive because right now we make carbon anodes, in many cases from resid, the stuff that is in asphalt on roads, and the stuff we used to burn in marine shipping engines is just another waste stream they pushed over to here. Most of that resid comes from those heavy sour crudes which are going away. So we’re going to have that variance.
Pulp and paper, that’s 70% energy. So 70% energy, obviously electrification, but we’re also going to once again divert single use to mass timber. So that means we end up with a virtuous thing. Oh, something I forgot to mention about mass timber. Every ton of mass timber is much lower emissions than concrete, obviously, but it also, every ton of mass timber also sequesters a ton of carbon dioxide drawn from the atmosphere for decades. And then at end of life we have multiple, I’ve counted five ways so far to permanently sequester that. So we divert single use to mass timber that takes carbon that was in the atmosphere, sequesters it for decades, and then we permanently sequester it after that. It makes buildings carbon negative.
For glass electrification in the big requirement, and then there’s a handful of straightforward process changes we already know for the process emissions. We’re not doing them today because once again we’re treating the atmosphere as an open sewer and it’s unpriced. 80% of that is energy, and recycling and electrification are huge about that.
A bunch of lime is used there, and there are alternatives to limes like magnesium oxides and aluminum oxides, which means we don’t have to use limestone for that. It’s just cheap right now. And then we have limestone alternatives. This is place possibly where basalt diabase and dacite might be used more.
There’s nitric acid, which is used in fertilizer. It produces a lot of nitrous oxide. Nitrous oxide, N2O, has 273 times the global warming potential of carbon dioxide. It’s a big deal. As we reduce our use of ammonia based fertilizers, we reduce our requirement for nitric acid for them. And then there’s a handful of existing process changes already known to deal with that. This is a solvable problem.
We have the technologies and solutions. It’s actually not that hard to abate. We just have to price carbon and produce the amount of energy required and change some of our processes.
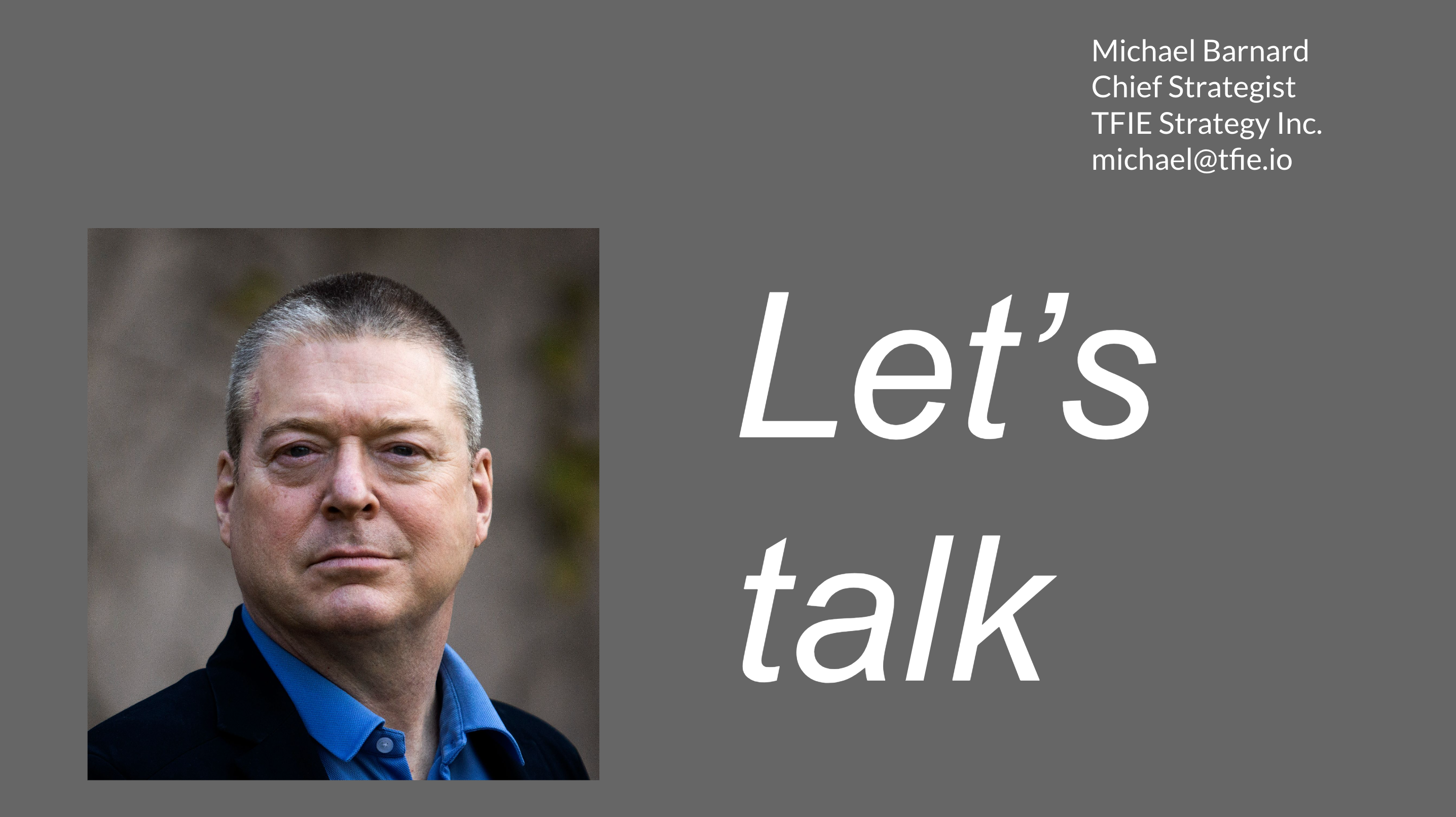
That’s kind of the end of my discussion. We did end up taking a little longer there. I’m not surprised, because I said the slides were dense, and one of them was the first time I spoke to it. So we have time for questions.
RP: The audience, those who go through it. Anyone has any questions, please post it on the group in the chat box. There is one question from our friend Rish, which is on the screen. Over to you, Michael. But strictly speaking, data centers don’t come under the international processes. This is still under the buildings group. But anyway, this is a very fast growing area, which is consuming tens of thousands of megawatts every year in many places.
MB: I will answer this because I’ve been irritated by this current round of hysteria about data center energy use. I did the math for the United States. If we take transportation and industry, data centers are 1.3% of the energy requirements of transportation and industry. And data centers are almost very strong buyers of green electricity. The energy for transportation and industry is all fossil fuels, which are creating the climate problem. And the very big data center use is electricity. We have to electrify everything.
And one of the big answers for climate solutions is digitalization as we consider some of these things. I did a 151 page report, an assessment globally in machine learning and all the ways it’s being applied in clean technologies in 2020. (Reach out to me if you want a copy of it.) If we take material science for solar panels. Now, most material science is using machine learning to find high efficiency intersection points within complex material spaces to enable us to do much less testing to get higher efficiency and results. Pretty much all material science nowadays includes a big stream of machine learning and AI, and that’s decarbonizing great swaths of our industry.
People worry about this. I did the math because I use ChatGPT and DALL-E from OpenAI to generate images. I determined that it was around 0.4 grams of carbon dioxide per image between all the learning and the actual execution of the thing. So 0.4 grams, that’s about 21 grams for a cup of coffee.
The second piece of context is that was with the old chips. NVIDIA just released a chip that is a graphic processing unit upon which all this stuff operates, which is 25 times more power efficient. So take that 0.4 grams and divide by 25. Data centers have been a strong demand sector for green electricity, creating markets for renewables. They signed power purchase agreements in all the developed world, and in much of the developing world as well, for the energy they require.
The hysteria is misplaced. The scale of the problem is much lower. They are not the problem. And so I always ask the question on this one. Who benefits by pointing fingers at data centers? Could it be transportation industry and the fossil fuel industry which supplies all of their energy? I don’t know.
It just seemed a little obvious to me. I do know that I’ve been tracking this hysteria for decades. It first emerged in the 1980s with email use. At one point, people were claiming that emails had enormous carbon debts. And then in the mid nineties, it was data centers part one. And then in the late nineties, it was something else. And then in late, in mid to late two thousands, it was AI part one. The first hysteria about training AI models occurred. Then in late 2020, there was another burst of it because an MIT study came up. It was quite remarkable. This is just the latest round of it. It’s a distraction. Getting worried about data center demand for electricity is a distraction from the real problems. It’s mostly a regional problem.
In terms of the Pacific Northwest, United States, they aren’t building enough transmission, storage and electrical generation. And so increases there are taking electricity away from other places. But that’s because they’re not doing their job of building lots of electricity, building a lot of transmission, building a lot of storage.
RP: Utilities, electric utilities love data centers because it’s a constant load, almost 24 7365 days constant load. So they just love them. It’s a great source of revenue. There is another question Raj is asking how to avoid industries adopting green energy for their energy demand. This is truly decarbonize the industry as the emission still remains as high as it would have been. While it depends on the green energy they use, if it is renewable energy, it is not. No emission. It depends what are they replacing the fossil fuel with? So if it is some of the fuels which are produced by consuming renewable energy, but it is several times more than the regular energy, then its question mark. Over to you, Michael, you may like to take that.
MB: Yeah. 65% to 70% of the emissions from industry are for energy from burning fossil fuels. So by converting to electricity or in some cases renewable natural gas, which is a bit shaky in terms of an energy source for a variety of reasons, they are reducing their emissions. Now for cement, most of the emissions come from the limestone, not from the energy. And so that’s a case where if they’re just electrifying the limestone kiln and doing nothing else, they’re not achieving majority carbon dioxide reduction. But I’ve just gone through all the solution spaces, all the process problems have solutions. All of the energy spaces can electrify with renewables. This is not actually hard to abate. We’re just refusing to do the work because it’s a bit more expensive. So we have to push for that.
Carbon pricing is a big one and a big lever that is going to dominate this space. Europe, 13 states in the United States, Canada and China all have carbon prices. I’ll assert again, India is not in that list and should be. So reassert that. India should start putting a price in carbon because it’s a big easy way to move the needle on a bunch of these things.
Have a tip for CleanTechnica? Want to advertise? Want to suggest a guest for our CleanTech Talk podcast? Contact us here.
Latest CleanTechnica.TV Videos
CleanTechnica uses affiliate links. See our policy here.