Sign up for daily news updates from CleanTechnica on email. Or follow us on Google News!
One thread I’m pulling on across industrial solutions is the ability of electrochemical processes powered by green electricity to replace industrial processes powered by fossil fuels. Today someone handed me the end of a thread leading to Sublime Systems, a Massachusetts, USA, firm that’s using electrochemistry to make low-carbon cement.
It’s been a few years since I first dug into the problem that is cement. As I said in 2019, Cement’s CO2 Emissions Are Solved Technically, But Not Economically. That really hasn’t changed. As long as natural gas was cheap and electricity was expensive, the energy required cost more. Even that didn’t address the carbon dioxide that comes from the chemical process.
Making Portland cement today has a couple of major processes. The first is a limestone kiln, heated to hundreds of degrees Celsius. The limestone has calcium, oxygen, and carbon in it, and some of the calcium and oxygen become calcium oxide, referred to as quicklime or lime, while the carbon and the rest of the oxygen become carbon dioxide. (Although there are other variants of lime, whenever lime appears in this article it means quicklime.) That means that there are bunch of carbon dioxide emissions from the heat and a bunch from the chemical process. They are mixed together and when they come out of the flue they are hot, dirty, and unpressurized, not exactly perfect conditions for capturing the carbon dioxide.
The second is the horizontal rotating drum, the clinker kiln. The lime is put in the kiln with additives like silica, alumina, and iron oxide and heated with a massive jet of natural gas or coal gas, until it turns into a ceramic — clinker. It comes in chunks from 3 to 25 millimeters (0.12 to 1 inch). That’s what gets ground into the fine dust that is cement. That massive jet of gas is another source of carbon dioxide emissions from the cement process.
After that it’s bagged and shipped. Just add water and stir and the gray glue that holds our world together results. Getting the limestone to the site, crushing it for the kiln, moving lime to the clinker kiln, rotating the clinker kiln, grinding the clinker with additives like slag, fly ash, or limestone, bagging the cement, and transporting the cement to where it’s needed are all carbon emitting processes, but they are rounding errors by comparison to the emissions from burning fossil fuels and baking limestone. They are all relatively trivial to electrify.
In fact, all of the heat can be electrified too, and has been both historically and in demonstration units today. Electric heat for the limestone kiln is a relatively trivial thing to build into new kilns, although more challenging to retrofit to existing ones. And as I was discussing with one of the executives of an electric plasma technology provider recently, the big jet of flame can be replaced by an electric flame, the plasma, and already has been in places. Once again, relatively trivial to build into a new clinker kiln, but a bit more challenging to build into an existing one. All of this heat is well above heat pump levels, so while it can be electrified, there’s no magic bullet. A unit of electricity turns into a unit of heat and that’s roughly equal between burning fossil fuels and electricity. There are still efficiency gains, but they are percentages not multiples.
With an electrified limestone kiln, the flow of carbon dioxide becomes much purer, although still hot and unpressurized. It is easier to bolt on basic amine-based carbon capture to capture enough carbon dioxide of sufficient purity that it could be sequestered. It would about double the cost of cement however, and amine-carbon capture solutions globally have been radically underperforming in the real world.
Most of the big failures of carbon capture trials used this technology, including the Petra Nova project in the USA and Boundary Dam in Canada. Carbon capture advocates claim Petra Nova was a success because it managed to get up to 92% capture for a couple of months, but it required a natural gas plant be built to power the carbon capture that was bolted onto only one of eight boilers in the facility. Petra Nova cost $60 per ton of carbon dioxide just to capture it, never mind do anything with it, and every ton of coal produces about 3 tons of carbon dioxide. Just the carbon capture added $50 to $60 per MWh to the production cost, then it had to be piped somewhere to sequester it at more cost. That’s well above the cost of production of wind and solar, and in fact well above the wholesale cost of electricity from those sources by itself, hence the reason no one is building carbon capture onto coal and gas plants after wasting time and money trying it.
Without an economic reason to change, no cement plant operator is going to bother to electrify or to bolt on expensive and failure prone carbon capture solutions. In North America and Europe from about 2001 to 2022, natural gas was a low-priced, stable commodity. Heat from electricity was a lot more expensive than heat from gas, in part because natural gas was making a lot of the electricity and in the process throwing away half or more of the energy in the gas. In many jurisdictions, electricity prices are explicitly pegged to natural gas prices despite decoupling electricity from burning stuff as we add renewables. That’s a known issue and is slow to change, because it really benefits the fossil fuel industry.
Natural gas was already losing its stable low prices in 2019, of course. In North America, fracking and shale oil, the two dominant sources of supply, were proving to be much shorter lived than economic projections had assumed, leading to debt financing that couldn’t be serviced, bankruptcies, foreclosures, and even seizing of assets. That was causing spikes in natural gas prices in 2020. The Saudi-Russian price war on high priced oil extraction approaches was intended to drive many out of business so that more Russian and Saudi oil would be bought in the aftermath. That was putting pressure on North American extraction as well, although not so much that the USA didn’t become the world’s largest oil exporter, with 50% more barrels per year than Saudi Arabia.
But the Russian invasion of Ukraine triggered a global price hike on natural gas. In Europe, Russian gas became an economic weapon of Russia and then the barely operational Nord Stream 1&2 pipelines were bombed, with investigations clear only that it was likely a state actor, but without firm evidence as to which state. Fingers pointing at the USA are nonsensical, fingers pointing at Russia have much more credibility, but if there’s anything that the Ukraine has proven in the past three years, it’s that they are capable of a great deal. At some point 30 years from now, official secrets of some state or other will be unlocked and we may find out for sure.
That price on natural gas in the EU went up from €20 to €30 per MWH — the EU measuring a fossil fuel in MWh is just one of many oddities of global energy — to a peak of €280, a factor of ten. A ton of cement requires about a MWh of heat. That cement cost point of €150 per ton included €20 to €30 of natural gas, but suddenly that was €280 of natural gas.
The future economic reasons will boil down to pricing carbon, for the most part. It’s certainly the best choice, much better than having governments pay for all the carbon capture and sequestration of carbon, including the absurd amounts of infrastructure required for it and the attendant risks. If we take the EU’s budgetary guidance for business cases for the lifecycle costs of greenhouse gas emissions, the 2030 guidance is €250 at a 4% discounting rate, about €200 (US$215) in 2024 currency. At that carbon price, a ton of cement that costs €150 per ton wholesale will cost €350 per ton. In 2040, the equivalent carbon price will be €280 (US$300) and cement’s costs will rise to €430 per ton.
That’s in the same range as the peak costs for cement during the energy crisis. One of the silver linings for the EU about the energy crisis was a sudden focus on decarbonizing cement, a focus which will continue to bear fruit as carbon prices rise.
Cement is a significant portion of a 20-story commercial or residential building, hence the focus on embodied carbon in the past few years. And it’s a significant portion of its cost, from 6% to 18% of total construction costs. More than doubling the cost of cement will cause new construction to increase in cost, which is somewhat fine as it will incentivize reuse of existing building stock over tearing it down and rebuilding. But a carbon price at those levels floats all alternative cement boats. Carbon capture, which has significant drawbacks, will have to compete with the technologies that were not economically competitive in 2019.
All of these carbon dioxide emissions are multiplied by the sheer volume of cement we make annually. In 2023, the global cement production was approximately 4.1 billion metric tons. Cement consumption worldwide is expected to grow, with projections indicating it will reach around 5.28 billion metric tons by 2029. At a ton of carbon dioxide per ton of cement as a reasonable approximation, that’s around 10% of global carbon dioxide emissions. Add in the leaks from the natural gas and it’s higher, of course.
Cement is only 10% to 15% of concrete, so that’s 27 to 41 billion tons of concrete. That’s one of the few things we do globally that’s bigger than the fossil fuel industry, which extracts over 20 billion tons of coal, oil, and gas annually, mostly to burn to create carbon dioxide and waste heat, along with some useful work. Only concrete and the closely related sand and gravel industries are larger in tonnages than fossil fuels.
We use cement everywhere and should be grateful for it. It makes our bridges possible. It makes dense urban living possible. It makes hydroelectric dams and wind turbine foundations possible. It made the concrete Brutalist architecture beloved of parkour athletes and a lot of architects possible. Like steel, it’s hard to look anywhere there is something built by humans and not find it. We’re not going to get rid of cement or concrete and we’re not going to replace radical amounts of with something else because its characteristics, especially when combined with steel reinforcement, are incredibly flexible, strong and easy to use.
When I looked at cement alternatives in 2019, my chemistry was weak and my electrochemistry was weaker. That was the year I started working on my ability to do basic chemical and economic workups, starting with my case study of the dead end that is Carbon Engineering. Today my chemistry is middling and I actually understand the very basics of electrochemistry. This is to say, I now know how much more about how little I know about either subject, but can do some basic assessments. I’ve also had a lot more conversations about cement since 2019, which is part of why I’m such a sparkling conversationalist at dinner parties.
Enter Sublime Systems. It has an electrochemical approach to making lime, the useful stuff that comes out of limestone kilns. It does it with electricity, which obviously can be zero carbon. It does it at about room temperature, so the entire heat portion of lime kilns and attendant carbon dioxide emissions go away. It uses water. It uses anything that has lime in it already, including limestone, electric arc furnace slag and concrete.
Take the lime-bearing substance. Crush it into a powder. Feed it into the Sublime electrochemical process on one side. On the other side, electrolyze pH neutral water into oxygen and hydrogen and play with the pH and ionic chemistry a bit. Mix this together. The lime-bearing substance gets turned into its component elements which are attracted to different anodes and cathodes, with lime aggregating on one side and the rest of the stuff on the other or falling out of the solution.
Voila. Pure lime suitable for putting in a clinker kiln with the other stuff.
There are some provisos on this. If they start the process with limestone, the carbon dioxide and oxygen still turn into carbon dioxide. However, it’s pure and pressurized at 10 bar, so a lot easier and cheaper to capture and sequester than the amine-based approach bolted onto the limestone and clinker kilns. Still, lots of carbon dioxide from the limestone. 44% of the mass of limestone turns into carbon dioxide. Every ton of cement would still have almost 0.3 tons of carbon dioxide to do something with.
When we are talking about 4.1 billion tons of cement, that’s still 1.2 billion tons of carbon dioxide, in the range of all of aviation globally or all current emissions from hydrogen. Trying to do something with 1.2 billion tons of diffuse waste gas is a huge industrial expense.
Thankfully, Sublime can use any material that includes lime. Their test system is attached to an electric arc furnace. EAFs put crushed limestone in with the melted scrap and new steel to draw out impurities. Carbon dioxide emissions result of course, but the slag has a lot of lime in it and no oxygen. And it’s a lot of lime, 35% to 50% of the mass. Crushing it and putting it through the Sublime process results in the lime being captured and no additional carbon dioxide emitted. Effectively, EAF slag is a high assay source of lime that’s concentrated in an industrial process that creates a lot of it, and it has low value as a waste product. A bunch of it is crushed and added to cement today because it reduces emissions, but the Sublime process values it differently to create even lower carbon cement.
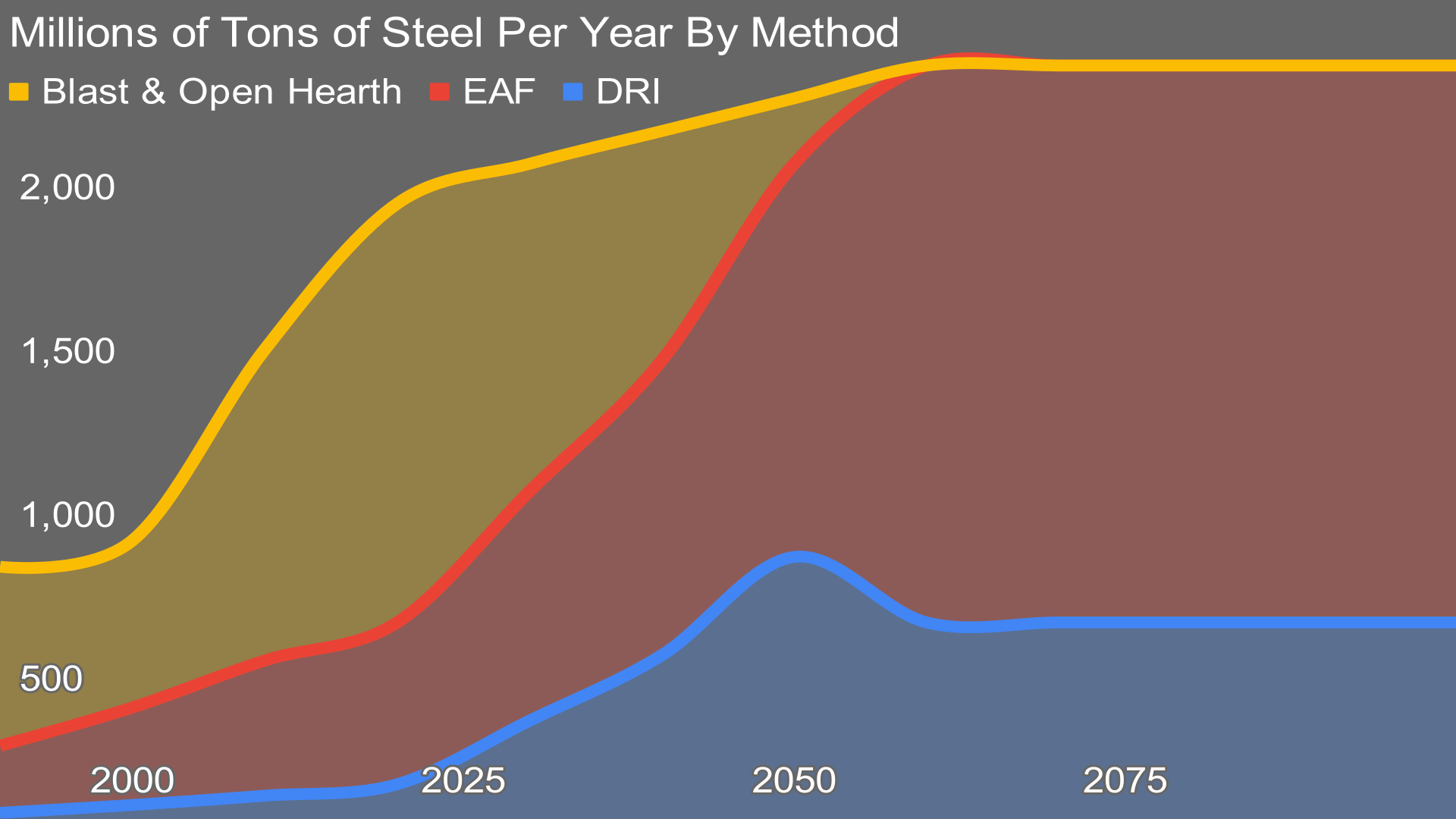
Over a year ago I finally got around to projecting the steel industry’s transformation and decarbonization. I projected that scrapping steel would grow to above US levels in the end game. That country is world-leading, with 70% of its steel demand met by scrapping steel, in part because it has a lot of old infrastructure and puts a premium on a lot of short lived consumer products containing steel.
In my projection, about 1.7 billion tons of steel will be produced this way. Assuming limestone is used, 90 to 180 kilograms are required per ton of steel, producing 30 to 60 kilograms of carbon dioxide. That’s still carbon dioxide emissions of about 80 million tons a year. But it’s also not very much lime for cement.
About 56% of the limestone turns into lime which the Sublime process can recover. Call it 230 million tons of lime available through this process per year in the end game. Assuming cement demand increases to 6 billion tons a year, with lime being 60% to 70% of cement, that’s a requirement for 3.6 to 4.2 billion tons of lime annually. 230 million tons is an order of magnitude off of demand. It’s not immaterial, but it’s insufficient, even in my EAF optimistic steel projection.
But Sublime’s process has another trick up its sleeve, concrete. 10% to 15% of concrete is lime, because all concrete is is a mixture of cement, aggregate, and water. Remember, we’re manufacturing 27 to 41 billion tons of the stuff annually, building bridges, buildings, roads, and foundations for a lot of things. And we are ripping down a lot of those things and are left with a lot of concrete and steel that’s an expensive waste problem.
Increasingly, we are crushing the concrete to get at the steel. About 90% of the steel in demolished reinforced concrete buildings is recovered in North America. The concrete is sent to landfills or used as roadfill and aggregate. Perhaps 2 billion tons of concrete are included in demolition waste streams annually today, so that’s another 200 to 300 million tons of lime that could be harvested, although the likelihood of that is lower due to the combination of existing local uses for crushed aggregate.
Still, between EAF steel and the demolition industry, there’s a potential source of 400 million tons or so of the potentially 4 billion tons of lime required. 10% isn’t bad. It’s a big lever to pull. And if the Sublime process could be used with limestone and the clinker kilns were electrified, emissions would be 30% of todays cement, and the resulting CO2 stream would be much less expensive to capture, if no less easy to get rid of safely and securely.
Will Sublime pull it off? Maybe. Aluminum is a massive industry globally, and it’s an electrochemical process as well. Only 60 million tons annually, however, two orders of magnitude off of cement. Chlor-alkali electrolysis is an electrochemical process as well, producing about 90 million tons of the chemical, used to create bleaching agents for paper, among other things. Electro-refining copper, zinc, nickel, and other metals is another few tens of millions of tons. All tonnages combined are below the levels we are talking about for the Sublime process.
That level of scale has taken decades. Building Sublime’s process up to more than the rest of that combined will take a long time too.
And that’s if it can be scaled. I now know enough about electrochemistry and industrial chemical processes to be able to see that it could be made to be a continuous process, something advantageous compared to batch processes. But a water electrolysis process with EAF slag will include a bunch of less valuable outputs, including lead and arsenic, toxic heavy metals that are bioaccumulators that build up in living organisms and cause pretty serious health impacts. That means Sublime’s waste stream will be toxic waste and have to be managed carefully.
There are multiple firms trying to separate valuable metals out of industrial slag of various types, but they are pre-commercialized endeavors. In EAF slag, useful metals are typically found in concentrations an order of magnitude lower than the ore bearing rocks they are found in naturally. Running multiple electrochemical processes on EAF slag to get out the tiny amounts per ton might never be economically viable.
Finally, can they make the entire process cheap? While electrolysis works, this does involve electrolysis of water and that’s an energy intensive process, hence the reason why green hydrogen is expensive. It’s unclear how much water they’ll require per ton of lime. It’s unclear how much electricity will be required per ton of lime. Breaking the bonds of limestone will still require energy, even if electrochemistry optimizes that significantly.
Like the chlor-alkali process, per the 2019 PNAS paper on the process, Sublime System’s process does have hydrogen as a waste product. It’s unclear if it’s in significant enough amounts to be economically viable to take advantage of in a scaled industrial process. After all, the Prince George chlor-alkali plant that is in a four-way deal to provide cleansed hydrogen to a nearby pulp and paper mill to displace natural gas for process heat is only producing 12 tons a day, below the requirements of most industrial demands for hydrogen as well as being in the wrong place. A modern ammonia plant requires 20 to 30 times that much hydrogen daily. It’s taken a decade of effort by various people to get close to using it for something.
Sublime has been coy about their current costs, understandably, as they are barely out of the lab. They have a 100 ton of cement a year plant — remember, 4.1 billion tons is the global production every year — and are in process of developing a 30,000 ton facility in Holyoke, Massachusetts. Modern cement plants produce 1 to 1.5 million tons of cement annually, and the 30,000 ton facility’s output would be produced in 6 to 10 days at that rate. The new site is still tiny, in other words, and may not be representative of fully scaled costs. It is located near a hydroelectric dam, however, so its electricity will be low carbon.
Where does this leave us? If all concrete and EAF slag in the future were diverted to Sublime’s process, it might provide about 10% of the world’s cement needs. If all limestone used today were put through the Sublime process, cement emissions would drop by 70%, but that would still leave them in the range of aviation or hydrogen.
The odds of 100% of EAF slag and construction waste being diverted are low. EAF slag is more likely to see higher use, but it’s used in an awful lot of places today already. Rail ballast — those black irregular rocks under tracks — is often EAF slag. It’s used in soil remediation in some places. It’s used as aggregate. It’s even used in some wastewater treatment processes. If it was all diverted to cement, those other use cases would go hunting for something else.
It’s not a slam dunk that high lime content EAF slag will find the most cost beneficial market in Sublime’s electrolysis process, in other words, just as it’s not sure if Sublime’s process can be scaled up to tens or hundreds of millions of tons of output annually. But it could. It will be interesting to see how this plays out.
Have a tip for CleanTechnica? Want to advertise? Want to suggest a guest for our CleanTech Talk podcast? Contact us here.
Latest CleanTechnica.TV Videos
CleanTechnica uses affiliate links. See our policy here.