Sign up for daily news updates from CleanTechnica on email. Or follow us on Google News!
Carbon capture and sequestration in all of its various ineffective, inefficient, and expensive forms is having another run up the hype cycle. Nothing has really changed. The problems still exist. The alternatives are still better. The potential for use is still minuscule. And so, the CCS Redux series, republishing old CCS articles with minor edits. The Carbon Engineering assessment series that this article was from was collected into a full case study with a foreword by Mark Z. Jacobson of Stanford: Chevron’s Fig Leaf: A Case Study of Carbon Engineering’s Direct Air Capture Plan.
The 5-part series on Carbon Engineering’s approach keeps bearing fruit. After the 7th and what we thought was final assessment was published, an independent energy researcher, one Leon di Marco, challenged our assessment. He’s spent a moderate amount of time publishing and talking about synthetic fuels, so we thought a follow-up article was warranted. Di Marco’s 1970s education was in electronics and solid-state physics and his career was in semiconductors and communications, but his current focus is on large-scale solar power and synthetic fuels.
If Carbon Engineering is making e-diesel, driving the same distance in a freight truck would cost at least 6.5 times as much and have 16 times the CO2 emissions as just using electricity in a Tesla Semi.
If you’ll remember from parts 6 and 7, we worked up a model where Carbon Engineering would turn CO2 captured with its natural gas-powered 2 kilometers of fans and 900 degree Celsius temperature device, and hydrogen electrolyzed from water using BC hydro electricity, then converted it into methanol or wood alcohol. We compared and contrasted that with just using electricity directly in an electric vehicle to assess how odd this situation was.
We arrived at two summary tables which highlighted the comparisons. This first was the energy, CO2, and cost workup for creation of methanol.

The second was the comparison to using the methanol as a gasoline additive or converting it to gasoline using one of several processes compared to just using the electricity in an electric vehicle.

That assessment, which was incredibly generous to Carbon Engineering’s process and ungenerous to electric vehicles, found at best its fuel would be 25x the cost and 35x the CO2 emissions of just using an electric vehicle with the same energy.
Di Marco’s assertion is that Carbon Engineering is using a Greyrock Energy Inc. patented process to transform CO2 and hydrogen directly into a synthetic diesel or a synthetic jet fuel. How he knows this is unstated, but he’s published in the space and has contacts. Carbon Engineering has been silent on this series, so we’ll take di Marco at his word, plug in what we see and find out how Carbon Engineering’s solution would stack up.
How does Carbon Engineering’s freight diesel option stack up?
Let’s look at diesel first. The Greyrock patent asserts that it has an effective process for creating a variety of heavy hydrocarbons, depending on catalysts and process, in a simpler approach than large scale refineries use. Diesel’s average chemical formula is C12H24. Comparing to methanol’s CH3OH, this potentially bodes well for Carbon Engineering as there are half the hydrogen atoms to carbon atoms required, 2:1 not 4:1. That means that given a ton of CO2, we only need about 48 kg of hydrogen to add to the 272 kg of carbon (remembering the 5% hit on hydrogen that’s lost to the process). That will save some money, energy, and CO2.
And it’s direct-to-diesel, instead of going through an intermediary, unless you count the processes related to additives. That means no losses for an extra step of conversion from an interim drop-in fuel to an actual fuel. And it’s diesel, which is a bit more energy dense than gasoline, so that bodes well too. However, there’s less hydrogen, so more of the energy is coming from burning the carbon, so the ratio of CO2 should be interesting to assess.
To be even more fair, we need to compare this to freight vehicles that use diesel for this point, rather than to passenger cars.
Chip in a few dollars a month to help support independent cleantech coverage that helps to accelerate the cleantech revolution!
Greyrock makes no economic claims in its patent except to say that this is an appropriate technology for on-site, relatively small-scale generation of diesel where shipping costs are prohibitive, and that it could scale. That’s not promising. Let’s make an assumption that its one-step process to diesel costs the same as the one-step process to methanol in the absence of other information.
How much diesel would be created by this process? Once again, that’s easy. The 272 kg of carbon will combine with roughly 46 kg of hydrogen to create 318 kg of diesel. Hmmm, that’s a lot less than the 730 kg of methanol that would be created.
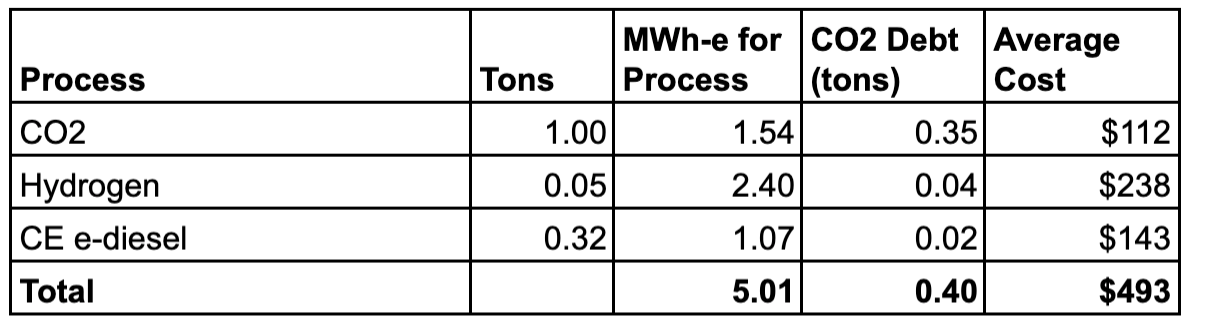
Interesting so far. You get half as much fuel for half the cost with almost the came CO2 debt, but the energy intensity is higher. How does that compare to an electric vehicle instead of a diesel vehicle? Well, let’s look at the Tesla Semi, as a large portion of diesel is used by freight trucks and similar vehicles.

318 kg of diesel is about 82.2 gallons. Freight trucks in the USA were averaging 6.4 miles per gallon in 2010 (down from 9 miles per gallon in 1949, oddly). That means a freight truck could travel about 526 miles on the e-diesel created by this process.
How would the Tesla Semi do on the 5 MWh equivalent of energy? Well, the company asserts the consumption at less than 2 kWh per kilometer, which we’ll round up to 3.2 kWh per mile. Once again, being generous to the air-to-fuel and not-so-generous to the electric vehicle, the Tesla Semi would travel 3 times as far on the same energy. And once again, it would travel further on just the electricity inputs to the process excluding the natural gas inputs than the e-diesel solution would drive a truck.

So, for the same energy inputs you could travel 3 times as far for a 5th the CO2 emissions and well under half the cost in an electric truck. If you wanted to drive the same distance, it would cost you 6.5 times as much before distribution, storage, and markup of the e-diesel, and have 16 times the CO2 emissions. The CO2 emissions are better than standard diesel but 50% of bad is still bad, and it costs at least twice as much for e-diesel from Carbon Engineering when the alternative electric Semi is a quarter the cost per mile and has a fraction of the CO2 emissions as well.
Per the American Transportation Research Institute, fuel represents about 21% of the costs of freight trucking. Tesla and other electric trucks are promising to reduce that to about 6%, while Carbon Engineering’s solution would increase it to at least 34%. Which is the freight industry going to be interested in?
Obviously, that’s not a viable market unless your strategy is continuation of the internal combustion engine. I wonder who benefits from that? Certainly not the trucking industry which has to pay for the fuel, the consumers who have to pay for more expensive shipping, or the world which has to pay for the higher than required CO2 emissions. That’s a very expensive 50% CO2 emissions reduction when a very cheap 90% reduction is available.
What about jet fuel for air travel?
So far, we’ve eliminated light trucks, cars and motorcycles, other trucks, and (urban) trains and buses from the mix. Obviously pipeline fuel and lubricants aren’t great choices for this either. That’s eliminated about 84% of the US market for Carbon Engineering’s air-to-fuel approach. But that still leaves 16%, right? Maybe there’s some gold there?
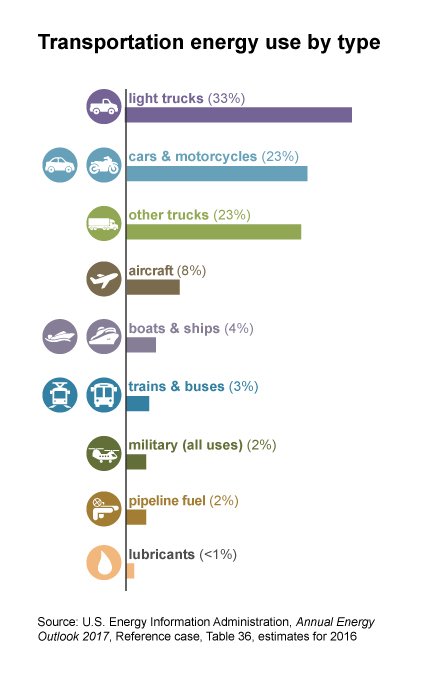
Let’s look at other use cases for petroleum transportation. Aircraft consume roughly 8% of petroleum per the US EIA, half of the remaining market. The Carbon Engineering process could be used to make an alternative aviation fuel. What do the large majority of jet and propeller planes use? Blends of kerosene which come in various flavors with carbon atoms in the 10-16 per molecule and a wide variance of hydrogen. The simplest is C10H8, but this is just the start.
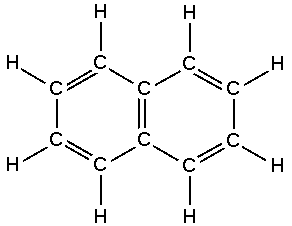
Aviation fuels aren’t defined by specific chemical compounds, but by characteristics of performance. As a result, anything Carbon Engineering could create would be feedstock for aviation fuel, not an aviation fuel in and of itself. That said, let’s work out the same comparison.
Two fewer hydrogen in the ratio means less electricity to produce the hydrogen. Let’s assume yet again that generously a variant of the Greyrock process uses the same energy to make kerosene.

Perhaps thankfully for Carbon Engineering, this isn’t a place where electrification is expected to dominate and some form of synthetic or biofuels will be required for the coming decades. There are certainly small electric planes commercially available today and most of the majors are working on hybrid electric planes for intercity routes, but significant distances are still going to require burning fuel for quite a while. That said, they are competing with low-carbon fuels that have been around for a decade.
This table is a portion of the concluding costs table from a 2016 NREL report on alternative jet fuels. These pathways have been being explored fully by many organizations for 20 years. If Carbon Engineering wants to compete, these are its competitors in this space and the likely economics. The comparable pathway to the one Carbon Engineering is on is circled.

That 307 kg of intermediate-stage kerosene that Carbon Engineering is creating represents about 84.4 gallons at a cost of about $6 per gallon. In 2016, equivalent processes based on biomass were running in the $1.9 to $2.5 per gallon range, well under 50% of the cost that this work is suggesting for Carbon Engineering’s approach. Jet fuel is running about $1.91 per gallon right now, so Carbon Engineering is doubly out of the market. It’s more expensive than existing alternatives that are already in play and at least 3 times more expensive than existing jet fuel. For our comparison, we’ll use the intermediate high-end of the range $2.5, knowing that it’s incomplete, but will at least give a sense of what’s going on.
But what about CO2? After all, this is supposed to be carbon emissions reduction technology. So far, it’s not working, but maybe in alternative jet fuels it actually has a value proposition?

Well, not really. The NREL study also does full workups on CO2 intensity of the different pathways. In exactly the same space as Carbon Engineering of creating liquid hydrocarbon fuels, but using biomass instead of capturing all the CO2 from the air with giant fans, CO2e emissions are 5% of jet fuel already, and at a price point well under 50% of Carbon Engineering’s per this workup.
For aircraft, Carbon Engineering’s solution is 3 times as expensive (at minimum) and only eliminates 50% of the emissions of petroleum-derived jet fuel. It’s 2.3 times as expensive as existing alternatives and has 10 times the CO2 emissions.
So where does this leave Carbon Engineering?
That’s another 8% of total market gone. That leaves us with 8% left, half of which are boats and ships and the rest spread across military, long-distance freight trains, and freight shipping. There’s no reason to go on. All of the same work will just show the same results.
Carbon Engineering’s approach of using natural gas to drive air carbon capture is not nearly as effective at decarbonization as alternatives, and it’s more expensive than existing alternatives with no apparent way to reduce those costs substantially. Its actual research value proposition has been completed. Its direct air capture has been prototyped at sufficient scale to robustly extrapolate costs, energy flows, and CO2-reduction value propositions. And it’s a bad approach.
It has no unique intellectual capital to bring to the table regarding either hydrogen generation or creation of synthetic fuels, but is going to bolt on technologies licensed from others, and those technologies are well understood. There is no knowledge that’s going to be gained of any significance as the company moves forward. They are trodding on paths made by others now.
Further, the assessment has shown multiple times that it’s much better to divert current resources to eliminating fossil-fuel generation of electricity and eliminating liquid fuel demand from transportation before trying to do anything with the excess of CO2 in the air. When deep in a hole you are digging, first stop digging, then start filling in the hole. Further, it’s worth pointing out that Carbon Engineering’s solution is only lower carbon when it’s on about as low-carbon a grid as exists. BC’s 15.1 g/CO2e/kWh is among the best in the world, and even utility-scale wind is 8 g/CO2e/kWh full-lifecycle. Using electricity for air carbon capture at all only makes sense in narrow niches where there is a lot of excess renewable electricity to soak up at low demand time periods.
Carbon Engineering was doing useful research for a reasonable price up until recently, and should have been wrapped up when it was concluded. But instead, it’s fighting to continue and grow. And that growth has lead directly to it being a fig leaf for Chevron, BHP, and Occidental, fossil fuel companies that don’t actually want to fix the problem.
References
Have a tip for CleanTechnica? Want to advertise? Want to suggest a guest for our CleanTech Talk podcast? Contact us here.
Latest CleanTechnica TV Video
CleanTechnica uses affiliate links. See our policy here.