Particularly for the underground mining environment, battery-electric machines offer significant operational benefits over their diesel counterparts in terms of exhaust emissions and heat generation. However, battery-electric machine technology is still relatively new to underground mining, and miners need to stay focused on maintaining production targets, Caterpillar says.
Battery-electric loaders like the Cat® R1700 XE LHD with portable MEC500 fast charging capability represent a new way of charging and operating. When should the operator top off the battery? How can the LHD operate in the most efficient way to optimise run time between charges? Where should the battery charger be located? What are the different safety and regulatory issues with a battery-electric solution? What unknowns will surface along the way that can be resolved through collaboration?
This is where Cat Job Site Solutions and the Cat dealer bring value, according to the OEM. Cat Job Site Solutions provides battery equipment and incoming power management expertise, and leverages the dealer’s equipment maintenance and repair experience, delivering assurances on R1700 XE productivity and machine availability. “This allows miners to focus on what they need – keeping site goals aligned with corporate goals and maintaining day-to-day operation of site and staff,” the company says.
The R1700 XE site solution program manages battery and charger optimisation and provides data to efficiently operate the machine. “We are basically taking Cat Job Site Solutions’ ‘site solution’ model that has been very successful for surface operations and adapting it to manage the battery electric R1700 XE and power requirements in the underground environment,” Brandon Croegaert, New Product Introduction Manager for Caterpillar, explains.

Better together
The R1700 XE site solution model simplifies the miner’s responsibilities, making costs manageable, increasing uptime and optimising battery management, according to the company. This model alleviates the burden of in-house fleet management, as Cat Job Site Solutions and the Cat dealer assume responsibility of ownership cost, training, charging strategy and battery management, maintenance, service, parts and the supply chain.
The program also mitigates some of the uncertainty surrounding new technology and processes, Caterpillar says. The Cat Job Site Solutions team first conducts a site optimisation study to help maximise productivity through determining optimum charging locations. The portable Cat MEC500 charging station offers the advantage of minimum production loss, as it eliminates the need of travelling to a permanent, expensive charge bay. It also allows operators to take advantage of breaks and delays with quick opportunity charging.
Central to the R1700 XE site solution model is a dedicated fleet manager provided by Caterpillar. The fleet expert offers equipment, industry and applications knowledge, lifecycle planning and management experience, leverages data from sites around the world, and offers a single point of contact for the R1700 XE LHD.
“Offering complete transparency of operating data, the program’s fleet manager shares machine and productivity data gathered daily with key mine site personnel,” Caterpillar says. “Weekly status updates allow the fleet manager, mine site personnel and the dealer to review data and make any necessary adjustments to machine operation and charging site location. Plus, planned maintenance on a bi-weekly basis helps to increase machine uptime and availability.”
Croegaert added: “Some of our R1700 XE loaders are logging more than 400 hours per month. The data show these machines can demonstrate the same or better availability than the diesel fleet.”
Change management
Croegaert also mentions that change management is critical to the success of running battery-electric equipment in the underground environment. “Operators are used to running diesel machines for eight to 10 hours at a time before refueling,” he says. “However, the battery-electric models need to be charged throughout the shift.”
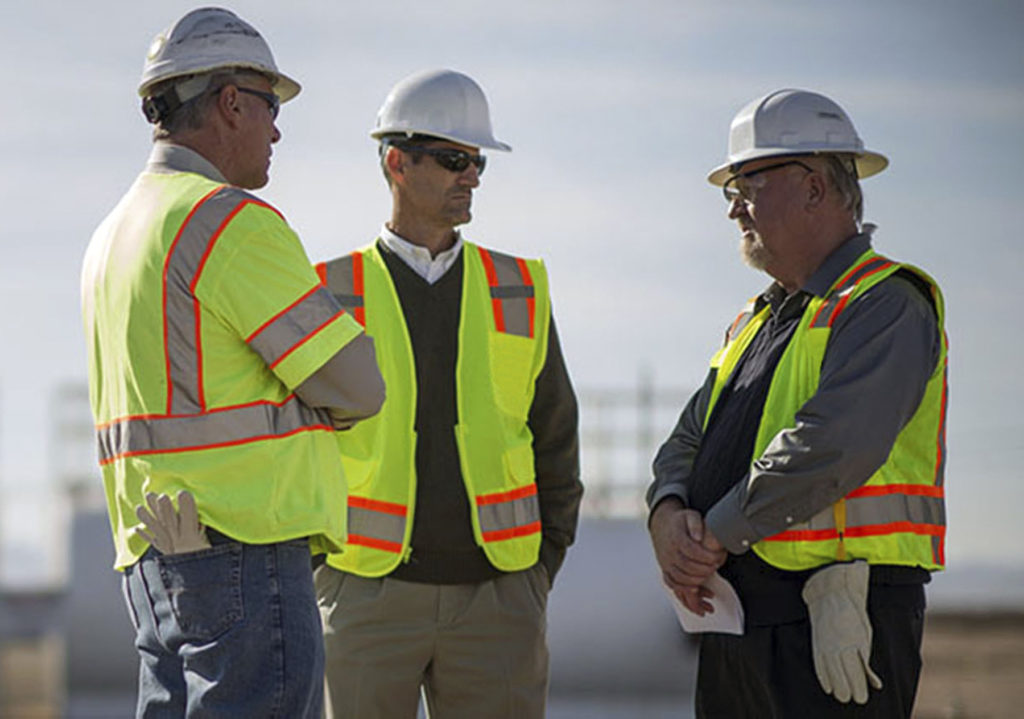
Operating efficiency is key to running battery-electric models successfully. The R1700 XE site solution model helps operators know when to come to the MEC500 for charging. They need to be aware of the schedule and take advantage of production downtime to top off the charge without impacting the production schedule. Predictive modelling using machine data also helps optimise the charging strategy.
The Cat Job Site Solutions R1700 XE site solution model is paying off for mine sites, as it is offering uptime availability guarantees for the battery-electric R1700 XE similar to that of its diesel-powered counterpart, Caterpillar says.
It added: “The fact that the machine runs with no exhaust emissions and lower heat generated is a bonus for those working near the machine. And this management model allows the mine site to focus on its core strengths while leveraging the expertise of Cat Job Site Solutions and the Cat dealer for machine management.”