
ANDRITZ SEPARATION provides state-of-the-art solutions for solid / liquid separation to the mining and minerals industry. Whether an operation produces gold, coal, iron ore, potash or aluminum, ANDRITZ SEPARATION aims to help improve products, boost throughput, and reduce operating costs.
ANDRITZ SEPARATION provides a 360º range of separation expertise with more than 150 years of experience, thousands of references worldwide, a 24,000-strong group and long-term investment in research and development. The ANDRITZ Group currently has 220 production sites, service and sales companies in 40 countries, almost all major mining regions.
Pressure filtration and vacuum technology
ANDRITZ SEPARATION offers a comprehensive product range for the mining and minerals industry. Leading pressure filtration technology ranges from advanced hyperbaric filtration solutions, to the latest vacuum technologies, including belt, disc and drum filtration, as well as belt and filter presses. ANDRITZ SEPARATION’s engineering capabilities, modular equipment and state-of-the-art technologies offers solutions that have a major impact on production performance and quality, as well as a portfolio that optimises the total cost of ownership.
Separation expertise for coal beneficiation
ANDRITZ SEPARATION is the world’s leading supplier of advanced, fine coal technology, including small and large-scale centrifuges, specifically designed filter presses, disc or drum vacuum filters, high-efficiency hyperbaric filters and tailor-made thickeners.
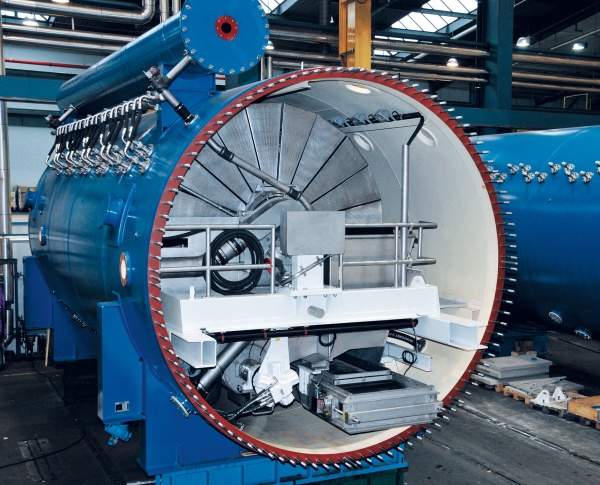
A fully assembled 120m² hyperbaric filter with filtration unit constructed entirely of stainless-steel.
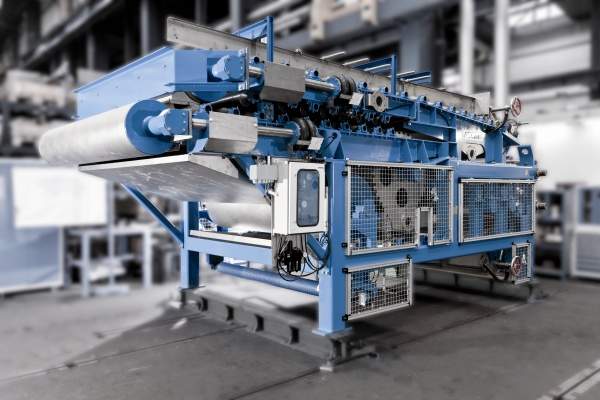
ANDRITZ SEPARATION belt presses are specially designed for the extreme wear and tear of mining environments, where the highest availability and lowest maintenance are essential.
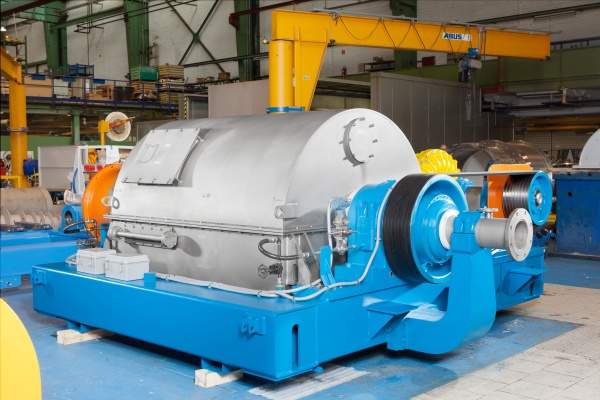
The unique conical screen bowl centrifuge delivers higher throughput, smoother operation while handling fluctuating feed solids concentration, and up to 15% less energy consumption than traditional units.
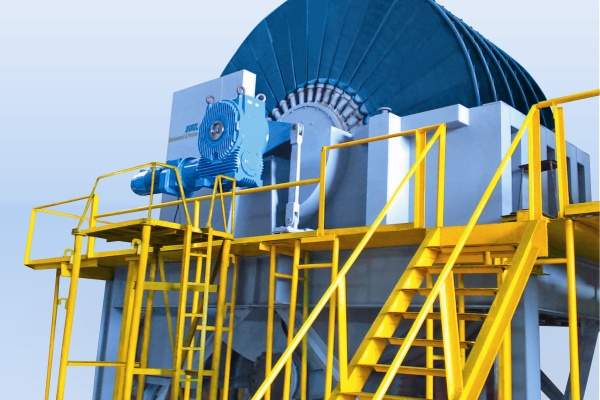
ANDRITZ SEPARATION vacuum disc filters such as this specialised filter for aluminium hydrate, ensure maximum surface area with minimal machine space.
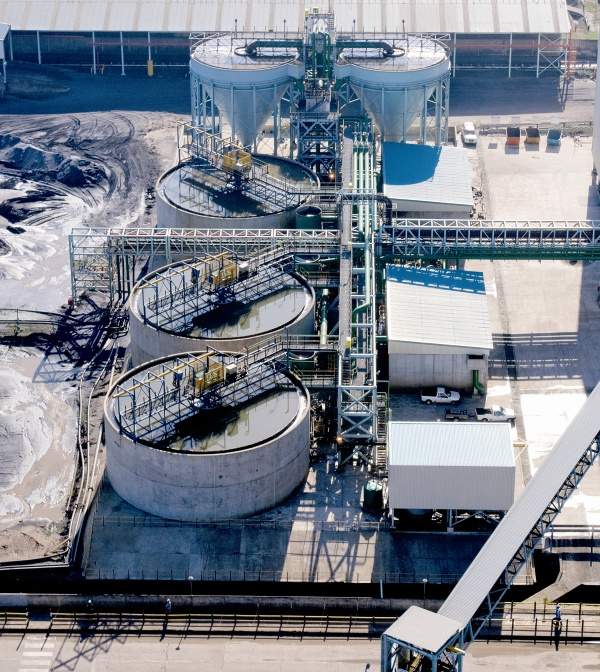
Thickeners with CCD technology ensure optimal inter-stage mixing, maximising soluble recovery.
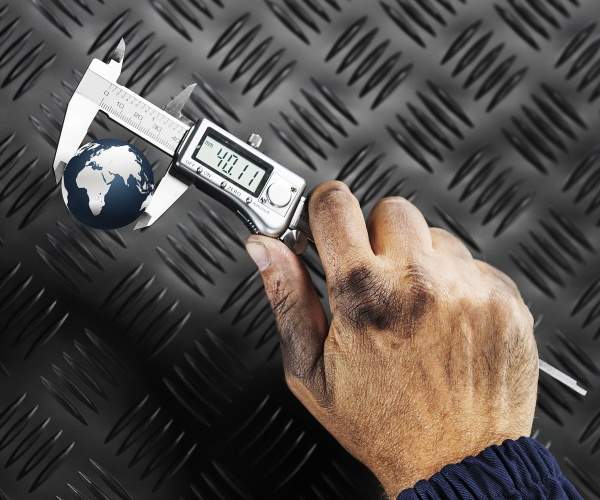
Whether you need spare parts, rentals, local service, repairs, upgrades, or modernization of your equipment, ANDRITZ SEPARATION is a 360° service partner.
To meet the greatest demands in the coal beneficiation process, significant effort has gone into the unique, efficient design and optimisation of the hyperbaric disc filter (HBF) for the filtration of ultra-fine particles. ANDRITZ SEPARATION also offers an extensive portfolio of superior washing and handling processes, even for the finest of coal particles.
High-capacity separation solutions for iron ore beneficiation
ANDRITZ SEPARATION offers specially designed solutions for high throughputs in the filtration process of an iron ore beneficiation plant. Hyperbaric filters, high-capacity filter presses and state-of-the-art vacuum filter technologies for disc, drum and horizontal belt filters are designed precisely to meet the different material parameters needed to efficiently produce metallic iron. In addition to the standard equipment for vacuum filtration and 100m diameter thickeners, ANDRITZ SEPARATION provides mining-specific filter presses and hyperbaric filtration. These meet the strict requirements for the finest iron ore used in pellet production.
Potash and brine refining
ANDRITZ SEPARATION supplies a comprehensive range of mechanical separation equipment and thermal drying systems for potash production, including centrifuges, thickeners, specific filters, filter presses and fluidised bed dryers / coolers. The company’s expertise in brine refining covers complete systems for the flotation process, hot and cold leach crystallisation, solution mining and solar evaporation, as well as detailed working knowledge to support demanding requirements.
The company offers its innovative approaches, such as the fractional dewatering process, conical screen bowl centrifuges and patented feed system for pusher centrifuges, which make it possible to achieve significantly lower moisture content, higher rates of recovery, higher capacities and reduced energy consumption.
Complete separation solutions for aluminum production
The dewatering and Bayer processes require numerous steps, so ANDRITZ SEPARATION offers a complete portfolio of leading vacuum and pressure filtering technologies, including disc, drum and hyperbaric filters, as well as state-of-the-art thickening solutions.
These solutions for aluminum production help to achieve maximum throughput and minimal residual moisture, for highly efficient vacuum drum filters. ANDRITZ SEPARATION vacuum disc filters feature an optimised ratio of filter surface to required machine space of six, making it possible to minimise investments in hydrate filtering building space.
Lifecycle solutions in non-ferrous dewatering
ANDRITZ SEPARATION has 50 years of experience in the non-ferrous industry, which has resulted in dewatering solutions for the complete plant lifecycle, from the latest filtration technologies to thickening solutions.
Vacuum belt filters with a filter surface of up to 200m² ensure high levels of throughput and extraction efficiency, while optimising energy and water consumption. For all counter-current decantation plants, the new and efficient inter-stage mixing and dilution system for counter current decantation (CCD) circuits helps reduce investment in space and, consequently, operation’s costs.
ANDRITZ SEPARATION’s innovative paste thickener provides additional savings in water recovery and tailing pond disposal.
OEM for solid / liquid separation equipment
With ANDRITZ SEPARATION, customers also gain access to one of the world’s largest OEM manufacturers for solid/liquid separation equipment, including such well-known names as Bird, KHD, Netzsch Filtration, Guinard, and many more.
From initial consulting to service agreements, plant optimisation, automation, spare parts, and training programmes, the company is always looking for new ways to help minimise downtime and increase predictability while raising production efficiency. Wherever you operate, the company’s network of 550 service specialists and global service centres ensure that ANDRITZ SEPARATION will always be there to support you for many life cycles to come.