Sign up for daily news updates from CleanTechnica on email. Or follow us on Google News!
What is ammonia and how does it fit into a decarbonized future?
Ammonia (NH3), in its role as a key ingredient in nitrogen fertilizers, is essential to feeding the world. It is also a solution for the decarbonization of hard-to-abate sectors as an energy carrier for hydrogen and a clean fuel for maritime shipping.
In 2021, around 180 million tons of ammonia were manufactured globally, 70 percent of which went into creating nitrogen fertilizers, with the remaining share used as an industrial chemical for pharmaceuticals, textile manufacturing, and mining. Soon, ammonia will play an even larger and more consequential role in food and energy systems worldwide.
The colors of ammonia and what they mean
Today, ammonia manufacturing depends on fossil fuels, creating an emissions profile that accounts for over 1 percent of annual global greenhouse gas (GHG) emissions. Through an industrial technique called the Haber-Bosch process, nitrogen and hydrogen are directly combined to form NH3. Currently, hydrogen is almost exclusively produced from natural gas and coal. As a result, ammonia production is heavily concentrated in low-cost coal and natural gas regions, such as the US Gulf, China, and Russia.
RMI analysis suggests that ammonia produced from natural gas generates 2.3 tons of carbon dioxide (CO2) emissions per ton of NH3, even more so with coal which can reach up to 3.9 tons of CO2 emissions per ton of NH3. Like hydrogen, ammonia is popularly categorized in colors: black, brown, gray, blue, and green. The color distinction is used to indicate the ammonia’s production pathway.
This simple color categorization is not necessarily a determinant of carbon intensity, but it is rather a useful shorthand. Ammonia produced from coal-derived hydrogen is generally referred to as “black or “brown”, and ammonia produced from natural gas-based hydrogen is considered “gray” because of its high carbon intensity.
As of 2021, all ammonia produced in the United States is derived from fossil fuels, 92 percent from natural gas, and only one operating commercial “blue” ammonia facility in North Dakota. As with hydrogen, “blue” simply implies the use of carbon capture technology. While adding a carbon capture system to existing production facilities can be a pathway to minimize ammonia-related emissions in the short term, gray-to-blue retrofitting is not always feasible due to specific plant-level limitations and shorter timeframe for return on investments.
Carbon capture technology is commercially mature, but operational system efficiencies are often lower than advertised. The captured carbon, if not stored, can be utilized in other manufacturing processes. However, while a blue ammonia process can mitigate some emissions, it does not eliminate process emissions entirely nor does it mitigate upstream emissions.
Reaching carbon neutrality with ammonia production is not only possible but quite straightforward from a technological perspective. It requires switching the hydrogen production to a zero-carbon process and operating the ammonia synthesis unit with clean electricity (such as wind and solar) — which brings us to the final color in the ammonia rainbow, green.
Green ammonia is best suited to reduce emissions from the production process to nearly zero. Green ammonia implies that “green” hydrogen was used to create the NH3. To make green hydrogen, an electrolyzer uses renewable electricity to split the molecules of water (H2O) into hydrogen and oxygen. When green hydrogen is combined with nitrogen in the Haber-Bosch process, powered by renewable energy, the resulting ammonia is virtually carbon-free. Although not yet widespread for ammonia applications, electrolyzer technology is well established and the production cost for green ammonia can be competitive with other low-carbon alternatives in regions with abundant solar and wind resources, such as in Western Australia, Northern Brazil, and the US Midwest.
The future of ammonia
With hydrogen’s potential as an economically viable fuel, feedstock, and energy storage solution in the future, its chemical derivatives, including ammonia, will take on a new role. Ammonia has the potential to become an important zero-carbon fuel for maritime shipping, as well as an energy and transport carrier given its higher volumetric energy density compared to hydrogen.
RMI forecasts ammonia production in the United States to increase by 113 percent of today’s levels by 2030, and diversify across these end uses (see Exhibit 1). Expectations are nonetheless highly variable and contingent on rate of adoption and cost decline curves for low-carbon ammonia.
Exhibit 1: Potential US Ammonia Market Size in 2030
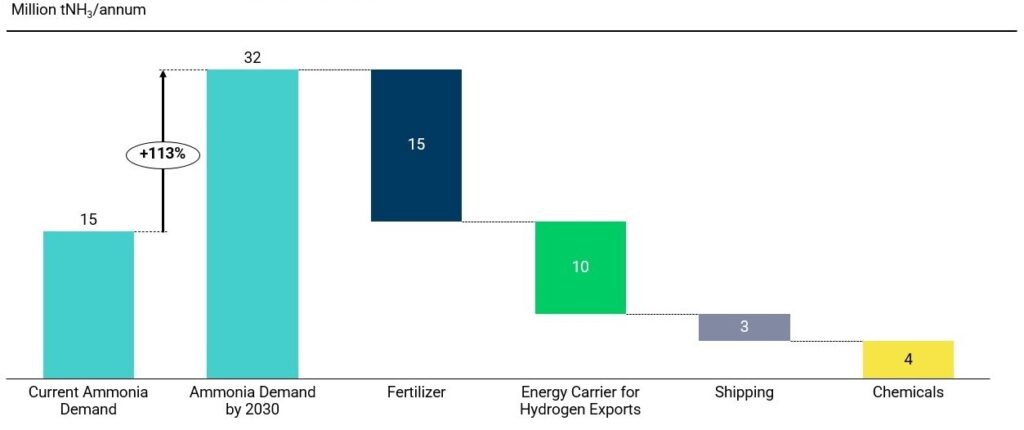
Hydrogen exports are projected to be the next largest sector for ammonia utilization behind fertilizers. Ammonia’s volumetric energy density is 1.5 times higher than hydrogen, which means that ammonia, when stored in a liquid state, contains more energy than liquid hydrogen at the same volume. Liquefying ammonia is also more cost-effective than liquefying hydrogen, making it preferable for transportation and enabling the chemical to act as an energy carrier. Additionally, unlike liquid hydrogen, ammonia is already traded via tanker ships for its use as a fertilizer.
New developments in ammonia technologies are paving the way for ammonia “cracking”, or converting ammonia back into hydrogen, such that the process of synthesizing ammonia from hydrogen, transporting the ammonia, and then cracking the ammonia back into hydrogen may become a cost-effective way to transport and receive hydrogen over long distances. RMI anticipates that the EU will drive 10 million tons per annum (Mtpa) of US ammonia demand, with Europe poised to become the largest global importer of hydrogen in 2030.
Ammonia is also projected to be among the most scalable and cost-effective low-carbon fuels for the maritime industry, which has recently set a net-zero by 2050 target. Ammonia applications in the maritime industry have yet to reach full maturity for ammonia-powered vessels: technical challenges need to be addressed, and effective safety regulations must be introduced. However, pioneering companies such as Fortescue and HD Hyundai are rapidly manufacturing ammonia-powered vessels, which might accelerate ammonia’s rate of commercial adoption in the shipping sector. Although carbon-free, ammonia combustion can produce nitrogen oxide (NOx = NO + NO2) and nitrous oxide (N2O) emissions. NOxemissions can be mitigated by selective catalytic reduction (SCR) technology, which can reduce them by more than 95 percent.
These emissions are generally considered indirect GHGs but can negatively impact human and animal health and should be closely monitored. N2O, however, is about 300 times more potent as a GHG than CO2; yet, with combustion tuning and after treatment, these emissions would be practically zero. Therefore, stringent mitigation tools should be in place to ensure that ammonia fuels can actually be low-emissions. Given the requirements that need to be met in the short-term, RMI estimates 3 Mtpa of NH3 will be required for use by the US shipping sector by 2030.
Getting to green
Green ammonia is essential to both removing a major source of carbon pollution and driving forward new fuel technologies, and we urgently need solutions to favor rapid, large-scale deployment. Financial tools to reduce the capital-intensiveness of green ammonia plants, faster permitting to access renewable electricity, demand aggregation initiatives to help suppliers get to final investment decision, and policy support to reach cost competitiveness should be introduced to advance green ammonia for fertilizers, maritime shipping fuels, and hydrogen exports.
By Sheran Munasinghe and Elina Rodriguez © 2024 RMI. Published with permission. Courtesy of RMI.
Have a tip for CleanTechnica? Want to advertise? Want to suggest a guest for our CleanTech Talk podcast? Contact us here.
Latest CleanTechnica.TV Videos
CleanTechnica uses affiliate links. See our policy here.
CleanTechnica’s Comment Policy