Sign up for daily news updates from CleanTechnica on email. Or follow us on Google News!
During what has become concrete month, I’ve explored the full range of actual and purported solutions to the climate problem that is the cement, steel, and concrete used in construction. The industry’s emissions are high, with every ton of reinforced concrete having a carbon debt of 0.3-0.4 tons of carbon dioxide between cement, steel, aggregate, and additives.
That doesn’t sound like much, but we use perhaps 50 billion tons of concrete annually, suggesting about 15 billion tons of our greenhouse gas problem come from the stuff we build. Fixing this is a requirement in order to fix climate change, but anyone reading along will realize that it’s not trivial.
We’ve looked at the creation of Portland cement, and the geographical, chemical, and cost issues that have ensured it dominates the space despite high emissions per ton due to baking the lime out of limestone. We’ve looked at steel, used as reinforcement in 70% to 80% of all concrete used, either as a mesh or as rebar. We’ve dug through the sand and gravel that make up the bulk of concrete, and the straightforward use of whatever is cheapest and closest — often limestone again.
We’ve dug through the world of supplementary cementitious materials (SCMs), finding that cheap blast furnace slag and coal fly ash from generation plants dominate this space not because they make the concrete better, although they do in some ways, but because they are cheaper than Portland cement and we have a lot of them lying around everywhere. Calcined clays, with or without the LC3 designation, aren’t as widely distributed and will cost more, so will be used only where there is no slag or fly ash available, and there is a lot of kaolin clay. Further, the clays don’t save that much carbon dioxide emission compared to slag or fly ash because they have higher emissions of their own during processing and transportation that offsets their slightly higher cement replacement.
And, of course, we looked at proposed alternative approaches to manufacturing cement. Some, which propose using basalt, ignore the very low percentages of lime-forming calcium and oxygen in the rock and the multiplying effect of the higher cost per ton, a fatal combination that leads to both 10 times more expensive cement (in the best case) and 9 times as much solid waste, whose only value proposition is as an expensive SCM. Others propose leaching the lime out of existing concrete waste from demolition and reactivating it, but we only have about 2 billion tons of waste concrete in the world, so only about 200 million tons of recycled cement are possible.
We’ve look at all of the ways that electric arc furnace (EAF) steel processes are being considered as levers for manufacturing cement directly, or for SCMs, or to recycle concrete, noting that EAF operators must be getting tired of cement dust being tracked around their facilities. That came with a good news story that we’ll be running a lot more lower-emissions EAFs to satisfy steel demand in the future.
And finally (so far), we’ve looked at complete replacements for cement, the polymers in epoxy and geopolymers. The first, made from oil, has challenges of cost and noxious fumes, but is widely used in offshore and other settings which require high chemical resistance. The latter, made from blast furnace slag, coal plant fly ash, or even aluminum’s bauxite refining waste — red mud — use the same wastes as SCMs, have similar chemical resistance characteristics to epoxy, concerns about caustic activators and, once again, are more expensive.
A theme running through this analysis was the cost point of cement and concrete. It’s really cheap for what it does, using broadly available materials found close to demand centers. All of the replacements that aren’t already being fully exploited, such as slag and fly ash, are more expensive.
But there was good news as well. Concrete demand is likely to drop radically. The first reason for this is that China is coming to the end of the most rapid, complete, and wide-scale infrastructure build-out in the history of the world, including 177,000 km of highways, 45,000 km of high-speed electrified rail, huge new cities with subways, massive solar, battery, wind turbine, and EV factories, and a shipbuilding industry that took a full 59% of all new build orders globally in 2023. It now has modern housing and transportation for the vast majority of its citizens, its often derided ghost cities filling up as expected. China has been consuming more than half the global cement, steel, and concrete in that construction blitz. As China’s demand declines, the world’s demand declines. The Belt & Road Initiative and the growth of more service and resource-oriented economies in India, Indonesia, and Brazil will not consume nearly as much construction material nearly as quickly.
Software has a place in the good news story was well. Emerging technologies in generative architecture and Finite Element Analysis (FEA) are transforming the construction industry by optimizing concrete use in building designs. By employing advanced algorithms, generative architecture explores numerous design possibilities to find the most efficient configurations, reducing material usage without compromising structural integrity. FEA simulates and analyzes designs, ensuring every cubic meter of concrete is used effectively. Practical applications have shown that these tools can reduce concrete volumes by up to 20%, leading to significant cost savings and lower carbon footprints.
And there was more good news. Engineered hardwood — cross-laminated sheets of wood held together with epoxy and coming in the form of load-bearing beams, walls, and floors — can be used to build entire buildings, up to 16 stories in Sweden and 12 in Canada, with only the foundations requiring concrete. Those foundations require less concrete as well, because engineered hardwood is much stronger than reinforced concrete, so all components weigh 20% of what their concrete equivalents would. A building made entirely of engineered hardwood would use 20% to 30% of the concrete, and hence have 20% to 30% of the carbon dioxide emissions embodied in it. Hybrid structures can be any height, with reinforced concrete used for load-bearing structures and the walls and floors made of engineered hardwood. This can cut building emissions by 50%.
There’s good news for the construction process with engineered hardwood as well. When buildings are built with engineered hardwood, the building information management specifications for all components are created in industry standard Revit and shared with the factory which manufactures the engineered hardwood components and the construction contractors. They are manufactured and delivered to job sites on trucks as massive LEGO pieces in order of construction from the ground up. Because they don’t require pouring, spreading, or setting time, construction can be faster and de-risked.
There’s one last very good news piece regarding engineered hardwood. Trees breathe in carbon dioxide, break it apart, keep the carbon to build their wooden bones, and breathe the oxygen back out. The result is that every ton of engineered hardwood has about a ton of atmospheric carbon dioxide sequestered in it. It’s actually possible to build carbon-negative buildings, in other words. That comes with the requirement that when the building is demolished in 40 or 100 years, that we either repurpose the wooden components or dispose of them in a way that permanently sequesters the carbon, including options such as sinking them into the ocean’s depths, burying them deep underground, or using thermolysis to produce biocrude for biofuels and biochar, which can be disposed of reasonably easily.
Unfortunately, all of that goodness doesn’t come for free. While over 60 years, various factors mean that the lifecycle cost of a building would be slightly lower with engineered hardwood, initial costs are in the range of 20% more. Further, while engineered hardwood is 20% of the weight of reinforced concrete, it is still bulky and heavy, so will tend to be constrained to regions with lots of sustainably harvestable trees or good ports to receive shipments. It’s possible that engineered hardwood shipping will make up for some of the loss of bulk shipping, as the 40% of bulks that are coal, oil, and gas dwindle in the coming decades.
As another note on China’s shift away from concrete, China has planted more trees than the rest of the world combined since the 1980s when it committed to reforestation and aforestation to recover from the devastation caused by Mao’s various excesses and purges. They had planted an area larger than the size of France with new trees by 2019, have accelerated tree planting efforts, and committed to planting 70 billion trees to support the trillion trees initiative. Among other things, this has meant that in 2023, the revenue from China’s forestry and grassland industry reached approximately 9.28 trillion yuan (about US$1.31 trillion) or about 7.7% of the country’s GDP. They are fully capable of pivoting to engineered hardwood with domestic sources, having mature trees from the 1980s and 1990s that they can harvest sustainably, and increasingly they are doing just that.
Of course, we have a lot of buildings, and as the saying goes, the lowest emissions building we can construct is one that is already standing. Demolition will increase as China starts demolishing and replacing older structures, but will decrease as more buildings are valued for their existing embodied carbon that avoids even more emissions from building anew. Renovations will increase as a ratio of building over the coming decades as a result, so developers which are currently focused on putting new divisions on fresh grassland or farmland will face lean times.
And so, back to the fundamental problem of cost. While many of the solutions outlined above have significant emissions saving value, they cost more. What is going to make developers pay that extra cost for a building? And how will they get customers to pay for it? This is not just in luxury or premium developments where eco-conscious is waved as a marketing flag and hence a green premium is justifiable, but in all buildings and infrastructure.
There are two answers. The first is purely regulatory and the second is a market mechanism, so clearly should be the desired one for fiscal conservatives (hint: it’s not, so they aren’t actually fiscal conservatives).
Globally, regulations are increasingly focusing on the sustainability of construction materials by setting maximum allowable carbon emissions. In Europe, the RE2020 regulation in France mandates developers to measure and report the carbon impact of construction materials throughout their lifecycle, from raw material procurement to building operations and disposal. By 2025, the targets for reducing the construction carbon impact will become stricter, necessitating significant reductions by 2028 and even more stringent limits by 2031. This regulation encourages the use of low-carbon materials, particularly bio-based materials like wood, which have the potential to store carbon over their lifespan.
In the United States, New York City’s Local Law 97 sets specific carbon emissions limits for buildings larger than 25,000 square feet, including penalties for exceeding these limits. Starting in 2024, buildings that surpass their CO2e intensity limits will incur a tax of $268 per metric ton of CO2e. This law is part of the city’s broader Climate Mobilization Act, aiming to reduce greenhouse gas emissions by 40% by 2030 and 80% by 2050. Additionally, various US states have implemented “Buy Clean” policies, requiring the use of materials with lower embodied carbon for public infrastructure projects, further driving the adoption of sustainable construction practices.
Toronto, Canada has implemented stringent regulations to reduce the embodied carbon in construction materials, as part of its broader strategy to achieve net-zero emissions. The Toronto Green Standard (TGS) Version 4, effective since May 2022, requires new buildings to conduct an upfront embodied emissions assessment for their structure and envelope. The regulation mandates that the carbon emissions intensity of these materials must not exceed 350 kg CO2e/m² for low embodied emissions materials or 250 kg CO2e/m² for extra low embodied emissions materials. Note that this by usable floor space, not carbon intensity of construction meter per cubic meter, so it’s more stringent than it might seem.
This initiative encourages the use of sustainable building materials and promotes design choices that significantly reduce the carbon footprint of new constructions. As part of a comprehensive suite of policies adopted by Toronto City Council, these measures aim to ensure that new buildings are near-zero emissions by 2030 and that the entire city achieves net-zero emissions by 2050. Financial incentives are also provided for projects that meet higher performance standards, further driving the adoption of sustainable construction practices.
These are pockets of the future, and will spread globally as one of the key levers for pushing high emissions materials out of markets, so all developers are working on a level playing field.
But then there is the market mechanism — carbon pricing. The EU Emissions Trading System (EU ETS), the world’s largest carbon market, currently prices carbon at approximately €80 per ton of CO2 equivalent, or around US$88 when converted at recent exchange rates. This price is forecasted to range between €80.8 and €95.50 per ton in 2024, with an average expectation of €89.60 (approximately US$98.56) per ton. Despite economic slowdowns and reduced industrial activity, the EU ETS remains a cornerstone of the EU’s climate policy, aiming to cut emissions by 55% by 2030 compared to 1990 levels. The system covers major industries, including power generation, steel, and cement, driving significant investments in emissions reduction technologies. Their budgetary guidance, however, is much higher, around US$200 this year and US$300 in 2040.
In China, the national Emissions Trading System (ETS), launched in 2021, primarily targets the power sector, with plans to expand to other high-emission industries such as cement and steel. Regional pilot programs have seen carbon prices in the range of US$8 to US$12 per ton of CO2 equivalent. While these prices are relatively low compared to the EU, China’s ETS is expected to play a crucial role in achieving the country’s goal of peaking carbon emissions by 2030 and reaching carbon neutrality by 2060. The phased expansion and increasing stringency of the ETS are anticipated to drive more substantial emissions reductions in the coming years.
Canada’s federal carbon pricing system, which includes a carbon levy and an Output-Based Pricing System (OBPS) for large emitters, currently sets the price at CA$65 per ton of CO2 equivalent for 2024, translating to approximately US$48.75. This dual approach ensures that industries such as cement, steel, and concrete are both directly charged for fossil fuel emissions and incentivized to improve emissions intensity. The carbon price is set to rise annually, reaching CA$170 per ton by 2030.
Across the United States, a diverse array of carbon pricing systems reflects the varied approaches a subset of states are taking to combat climate change. California leads with its comprehensive cap-and-trade program, pricing carbon at about $30 per ton and covering a broad spectrum of economic sectors, from power generation to manufacturing, and including cement and steel. Washington has recently implemented a similar cap-and-invest program aimed at reducing emissions through a market-based mechanism. In the Northeast, the Regional Greenhouse Gas Initiative (RGGI) unites eleven states, including New York and Massachusetts, in a cap-and-trade system primarily targeting the power sector, with carbon prices around $13.50 per ton. Massachusetts also operates a separate state-specific program to complement its participation in RGGI. New York is developing an economy-wide cap-and-invest program, set to launch in 2025, which may either supplement or replace its RGGI involvement. Oregon, too, is working on reestablishing a carbon pricing program that places a declining cap on emissions from fossil fuel combustion. Coverage of cement, concrete and steel is patchy, but increasing.
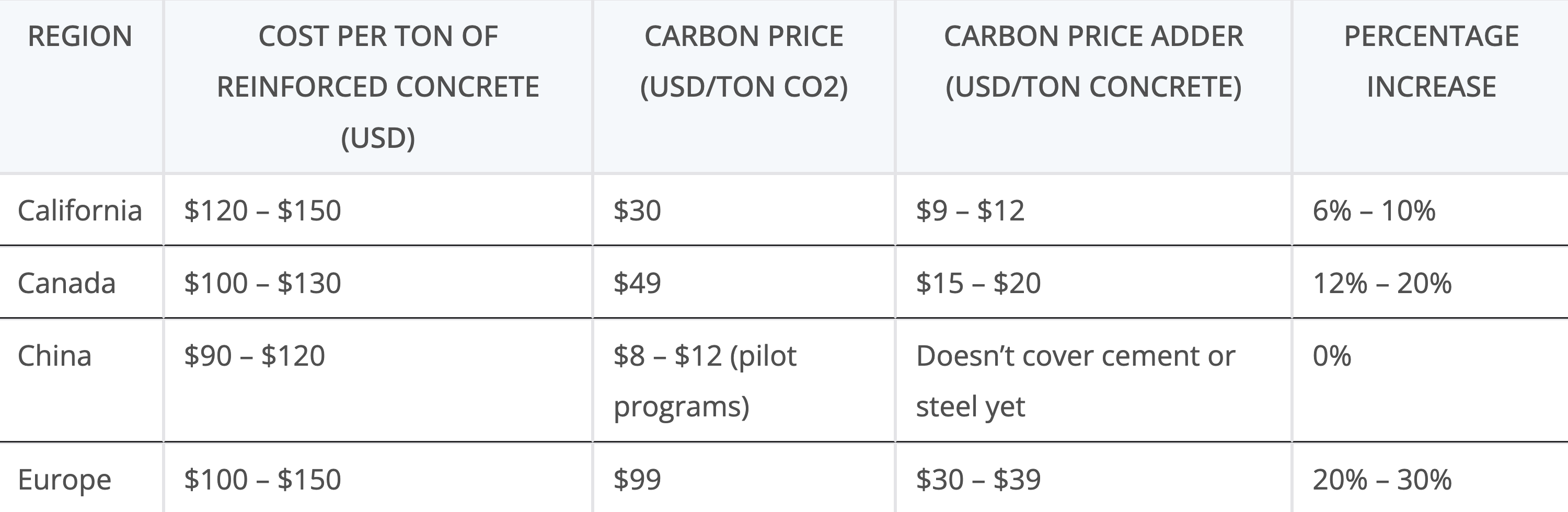
In Canada and Europe, the carbon price is already in the range where the premium on engineered hardwood starts being economical. Similarly, it’s in the range where the cost premium for fiberglass and even carbon fiber starts being economically attractive. Given the low cost of finite element analysis with modern building and infrastructure design tools, it’s already sufficient to drive greater use of these tools to cut concrete use. This also floats a lot of boats in alternative binders such as epoxies and geopolymers, making them cost competitive.
The combination is a very good news story for construction industry emissions, but it’s going to take a while to play out. Regulatory headwinds and industry conservativeness will slow adoption. But in the industry, money talks and the increasing carbon prices are a loudspeaker.
Have a tip for CleanTechnica? Want to advertise? Want to suggest a guest for our CleanTech Talk podcast? Contact us here.
Latest CleanTechnica.TV Videos
CleanTechnica uses affiliate links. See our policy here.