German steelmaking group Salzgitter recently blew in Blast Furnace A at its Flachstahl works in Lower Saxony, allowing it to produce up to 2 million MT of pig iron. This came after the company completed a relining that lasted 100 days. On January 3, Saltzgitter noted that the reline included 3,000 metric tons of bricks and other refractory materials and carried a price tag of €100 million (almost $110 million). The group added that the reline also included modernized control technology.
Relines are cost-intensive due to normally stipulating replacing the entire furnace along with control equipment. Blast furnace linings also use specialized refractory bricks that can contain fire clay, high alumina, silica and magnesia.
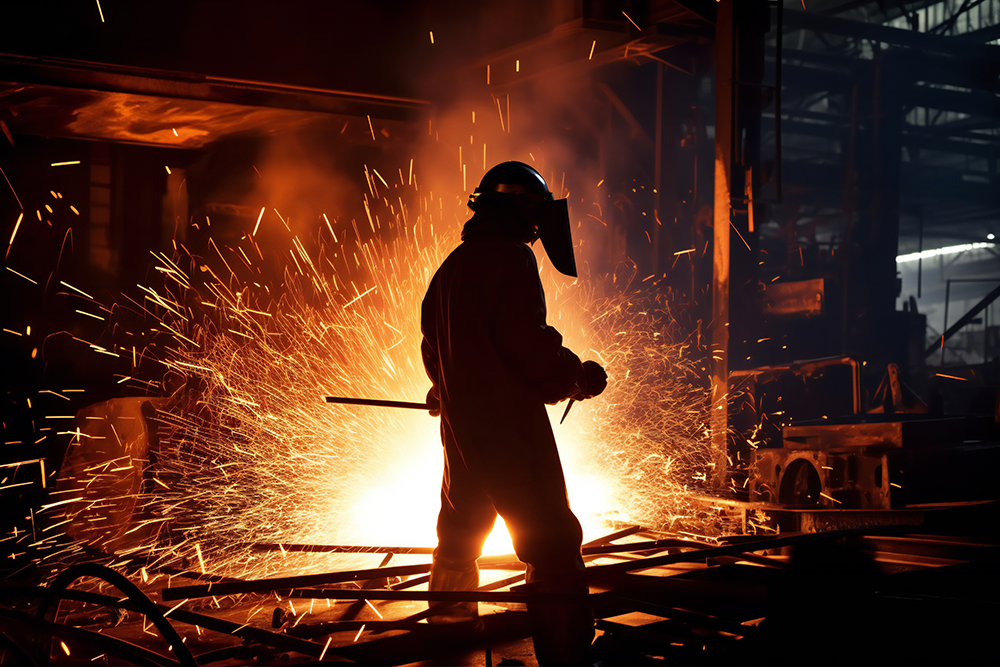
Blast furnaces are integral to the production of pig iron, which they produce through melting iron ore with charcoal and limestone under very high pressure. The composition of pig iron varies, but it typically contains 3-4% carbon along with varying amounts of sulfur, silicon, manganese, and phosphorus. Its high carbon content makes it very hard and brittle, which limits its direct use. Therefore, pig iron is typically used as an intermediate product to be further processed into steel or wrought iron.
Start custom mapping price points for your specific needs using MetalMiner Insights – your path to cost-effective sourcing. Ready to learn more?
Furnace B Challenges Industry Norms
Flachstal’s Blast Furnace A contains a hearth diameter of 10.8 meters and can produce 2 million metric tons of pig iron per year. Salzgitter noted that Blast Furnace B’s hearth diameter is 11.2 meters. Furthermore it holds an annual estimated capacity that exceeds 2 million metric tons.
In addition, the plant posesses three 220-metric-ton basic oxygen furnaces for crude production. This proves an addition to a 100-metric ton electric arc furnace at its Peiner-Träger site, roughly 30 kilometers north of the main site at Salzgitter. Flachstahl casts the crude steel into slabs via three continuous casting machines, which it then rolls into hot and cold rolled coil. The site also produces hot-dipped galvanized sheet for the auto sector.
The company also produces plate at its Ilsenburger Grobbelech site and spiral-welded pipe at its Mannesmann Grossrohr sites. Meanwhile, Peiner-Träger casts blooms, which it then rolls into beams.
Salzgitter Hopes to Recover Pig Iron Capacity for 2024
BF A’s relining was one reason Salzgitter’s Crude’s steel production declined 6.6% in the first nine months of 2023. Furthermore, information from Salzgitter’s Q3 report indicate that last year’s output came to 4.45 million metric tons. This represents a significant decline from the 4.76 million metric tons the plant poured over the same period in 2022.
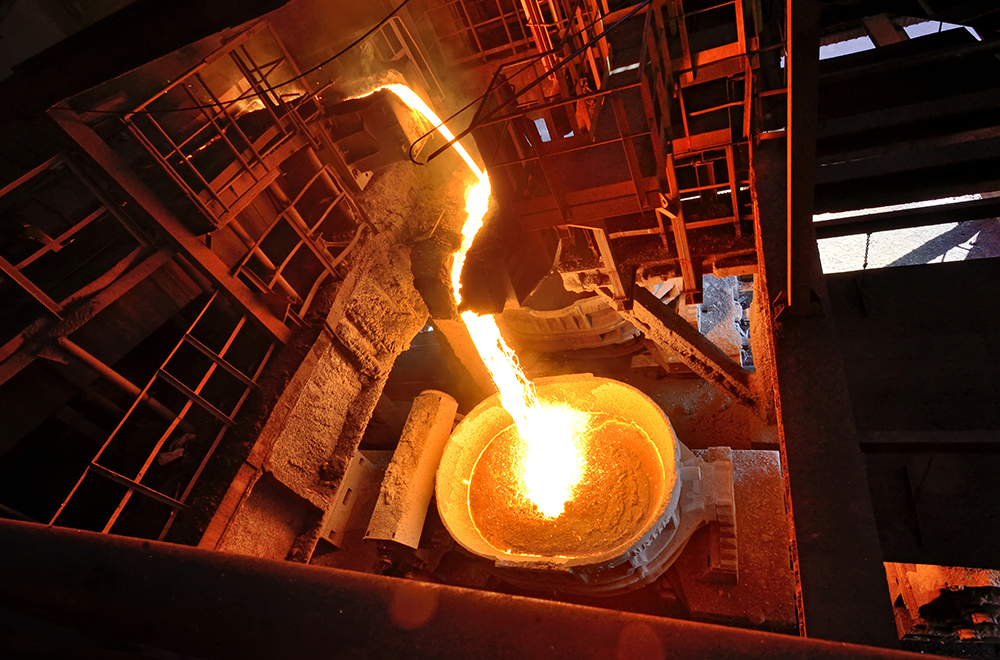
Although they started to recover, falling prices for European hot rolled coil throughout 2023 proved another reason for the lower production. “The selling prices of strip steel products stabilized only temporarily in the second quarter following the price decline at the end of 2022, before dropping further in the summer,” the group said in its report.
“Selling price levels also entered a steep decline in the sections business, resulting in a notable reduction in the business unit’s segment and external sales,” Salzgitter added.
Ten interest rate hikes by the European Central Bank from July 2022 to September, totaling 4.5%, saw offer prices for the flat rolled product in northern Europe hit a low of €605 ($660) per metric ton EXW in the latter month. By comparison, steelmakers were seeking €1,100 ($1,200) in September 2021.
Accurately report the impact of metal market volatility on your earnings to leadership and executive teams with MetalMiner’s Monthly Metals Outlook. Review a free sample report.