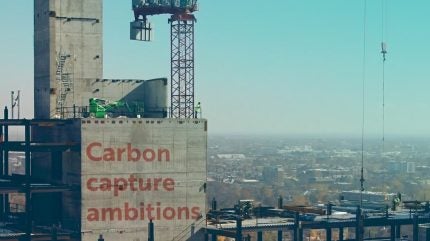
The cement industry faces a significant challenge to meet its ambitious net zero commitments. According to the Global Cement and Concrete Association, innovations such as more energy-efficient or renewably powered plants have so far only reduced industry emissions by 20%. Further steps are required for the industry to achieve net zero emissions by 2050.
Carbon capture utilisation and storage (CCUS) could remove these hard-to-abate emissions and help deliver global infrastructure within sustainable limits. However, for the cement industry, CCUS is still in the early stages.
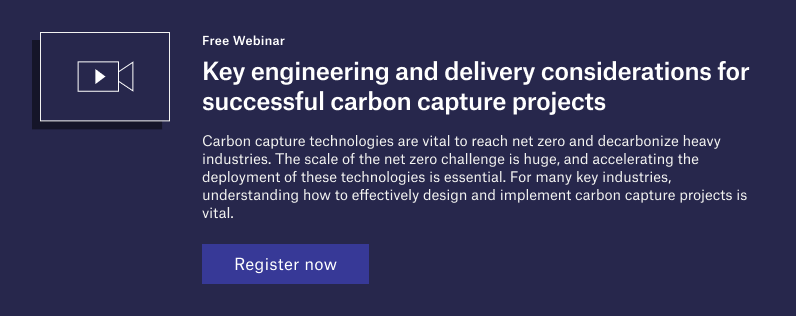
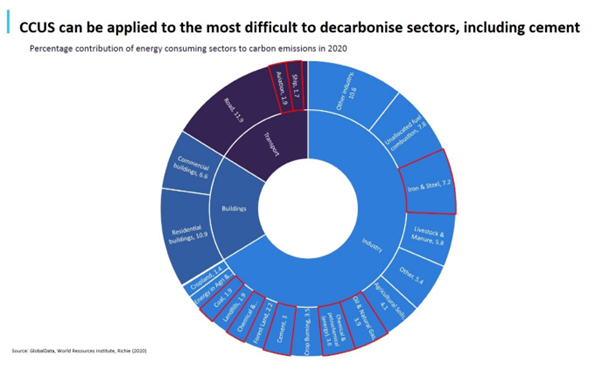
According to GlobalData, there is growing interest in capturing carbon from existing cement facilities, as well as emerging utilisation pathways such as carbon-negative concrete. Currently being pioneered through projects such as at Heidelberg Material’s Padeswood site in the UK and Edmonton site in Canada, the implementation of CCS will involve navigating the unique characteristics and constraints of cement facilities.
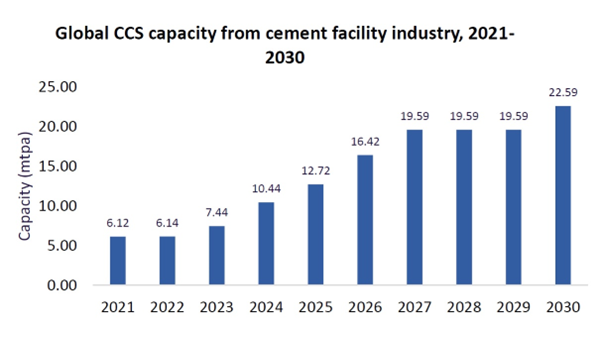
The CCUS challenge
Cement plants pose several specific challenges for CCUS that will require careful planning to overcome. Finding the necessary heat, electricity, and water sources for CCUS technologies will be difficult due to the lack of surplus steam, electricity, and water in cement production processes.
Space restrictions in brownfield plants will mean borrowing principles from other industries such as offshore energy. Complex pretreatments will be needed due to the higher concentrations of dust and particulates in cement plant flue gas.
There will also be a learning curve from first-of-a-kind applications to overcome when implementing new technologies in a legacy industry such as cement. Existing processes are deeply ingrained within cement plants and the new emphasis added by CCUS for gas processing means new approaches need to be implemented and expertise brought in from outside sectors. According to GlobalData, post-combustion capture will become the dominant CCUS technology by the end of the decade due to the advancing expertise in retrofitting existing emission sources.
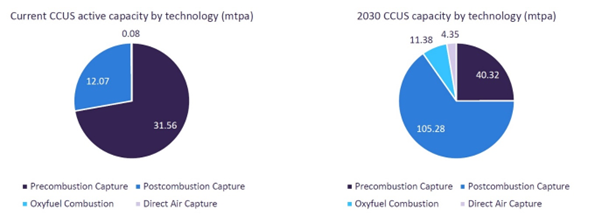
Unlike oil and gas, cement producers face tight margins that don’t hang on the price of a barrel. This means that cement CCUS solutions will need to be exceptionally cost-efficient. Perhaps most importantly, two-thirds of cement CO2 emissions come from the process chemistry itself. The higher concentration of CO2 in cement kiln flue gas will have implications for the cost and complexity of carbon capture systems.
Reducing the cost of carbon capture technologies will be critical to help producers stay cost competitive and reduce the potentially high ‘green premiums’ on sustainably produced cement.
The rollout of CCUS across the cement industry must be carefully tailored to these challenges. Planning should consider every factor from technology cost and complexity to flue gas pre-treatment, space restrictions, and utility requirements, including water balance and challenges with CO2 transport and access to storage sites.
Defining the objectives and assessing project feasibility
Planning must begin with understanding the specific goals of each cement producer that may include commercial and regulatory drivers as well as ESG targets. These range from sustainability goals such as reduced water use and decarbonisation to commercial objectives such as qualifying for carbon tax credits. According to GlobalData, ESG is one of the most important themes of the decade and is becoming increasingly crucial to construction companies.
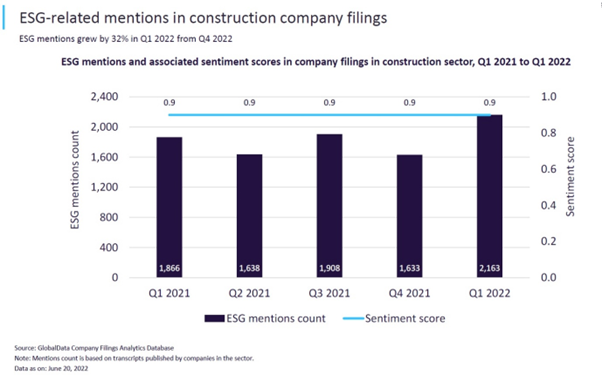
Once the decarbonisation goals are established, a full feasibility assessment can help identify the most technically, economically, and environmentally viable solutions for these goals. This begins with a comprehensive basis of design (BOD), including quantitative input and output specifications. This will then inform technology selection assessments to find the systems which fit the specific operational environment for each project’s goals across the full lifecycle, from carbon capture to end-use.
A structured method is required to ensure alignment between all the various technical, project execution, commercial, financial, and regulatory stakeholders. Multicriteria assessments should be used to balance conflicting factors from cost and commercial readiness to technology maturity and ease of adoption. For example, while amine scrubbing is the most mature technology, cryogenic systems may be easier to adopt because they do not need steam and potentially less utility demand on the system.
Technology selection assessments must factor in key limitations from electricity costs to the proximity of plants to nearby industrial hubs for transportation and storage. Crucially, technology selection should consider challenges specific to the cement industry such as relatively high concentrations of CO2 particulates, as well as sulphur and nitrogen oxides (SOx and NOx) impurities in cement flue gases. For example, baghouse upgrades or selective catalytic reduction (SCR) may be needed for the pretreatment of the flue gas.
A combination of process configuration and assessment, detailed cost estimation and comprehensive financial modelling can help prioritise the most financially attractive project options. These holistic selection processes could examine carbon lifecycles from capture to end-use, including underground CO2 storage or re-use as feedstock for green fuels.
Similarly, operators should factor in the plant’s entire future fuel mix as this may also affect the composition of flue gases and thus impact on carbon capture systems. For example, some alternative fuels produce increased levels of NOx and SOx in flue gas, which could reduce the efficiency of carbon capture systems.
Planning must include operational requirements spanning the full scope of work from inside battery limits (ISBL) focusing on the capture systems, to the outside battery limits (OSBL) encompassing all the necessary pre-treatment, utility feeds from water to electricity, and ducts from the plant to the capture system.
Project developers should also consider the full range of available decarbonisation options including hybrid solutions such as electrified calcination or alternative fuels combined with carbon capture. All this data is vital to optimise and de-risk CCUS implementation, helping smooth the path to a Final Investment Decision and implementation.
Cost estimating and financial modelling – including all aspects from carbon transportation costs to the size of potential CO2 markets – can also help rank solutions for cost competitiveness.
Overall, producers should involve technologically neutral experts to ensure they consider the full range of options for their specific constraints and criteria.
Borrowing processes from other industries
Once the technology options have been narrowed down, processes must be assessed and tailored to each plant’s constraints – such as space restrictions or proximity to heat sources and utilities. This will then inform lists of required equipment items and development of indicative plant layouts.
Expertise from other industries facing similar issues can again help deliver value and drive more efficient processes. For example, operators can use insights from similarly space-constrained sites such as offshore platforms to implement modular construction methods. Where carbon capture units are installed in prefabricated parts, or creative and compact equipment layouts.
Operators can also borrow process innovations from other industries with limited heat sources – such as integrating waste heat recovery innovations to generate steam for carbon capture.
From planning to real world application
To successfully move from design to implementation, it is crucial to align project delivery with initial considerations such as regulatory requirements and permitting processes. Establishing a clear project roadmap for the pre-front-end engineering design (Pre-FEED), FEED, and delivery stages will outline all necessary requirements. Ensuring stakeholder alignment with this roadmap is essential.
Ultimately, implementing CCUS in cement will be a complex process, navigating many industry-specific obstacles. A successful rollout will require embracing new or de-risked technologies and integrating lessons from other industries.
With cement producers facing tight margins, efforts must focus on driving down the cost per tonne of CO2 capture to achieve the necessary scale for meeting net zero targets economically.
It will also be an iterative process where new skills and processes must be tried, tested, and then reproduced across all stages of deployment. Learning by doing and then sharing these lessons across all project stages and sectors will help create first-of-a-kind CCUS deployments across the industry.