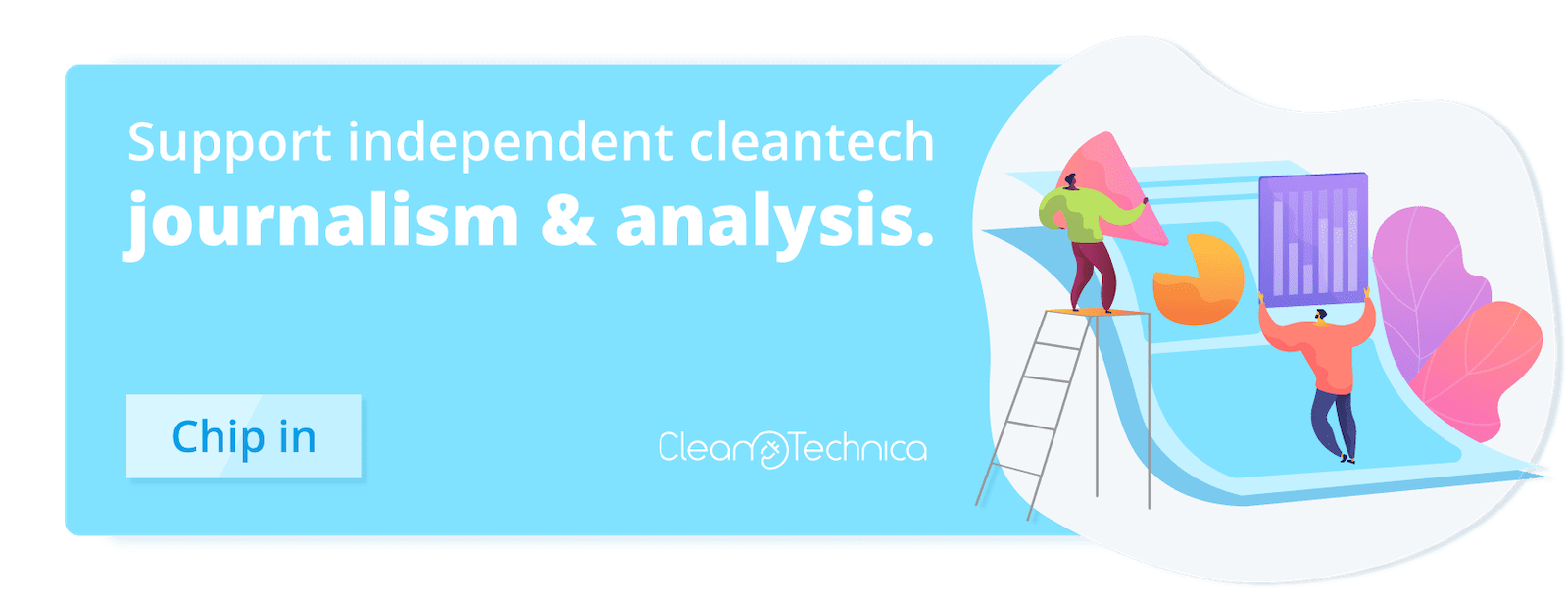
Agora Industry’s latest report, 15 Insights on the Global Steel Transformation, states that the steel making sector can play an important role in driving down greenhouse gas emissions and thus slowing climate change impacts. Every night, we watch as the weather, once the last 5 minutes of the news broadcast, becomes the news itself. Australians are watching the floods and bushfires of the northern hemisphere’s summer and asking themselves “What will it be like in a few months when our southern summer begins? Will Brisbane melt?”
You are probably familiar with Agora Energiewende, but what is Agora Industry? “Agora Industry is a division of Agora Energiewende that develops strategies and instruments for climate-neutral industrial transformation — in Germany, the EU and globally. Agora Industry works independently of economic and partisan interests. Its only commitment is to climate action.”
The major insight from Agora is that the once seen as “hard-to-abate” sector, the steel industry, now has the potential to turn into a “fast-to-abate” sector. A net-zero iron and steel industry is technically feasible by the early 2040s using a rapid rollout of direct reduced iron technology, the phaseout of metallurgic coal, and the expansion of international trade in green iron. We might just have a chance to choose a future in which we can all live.
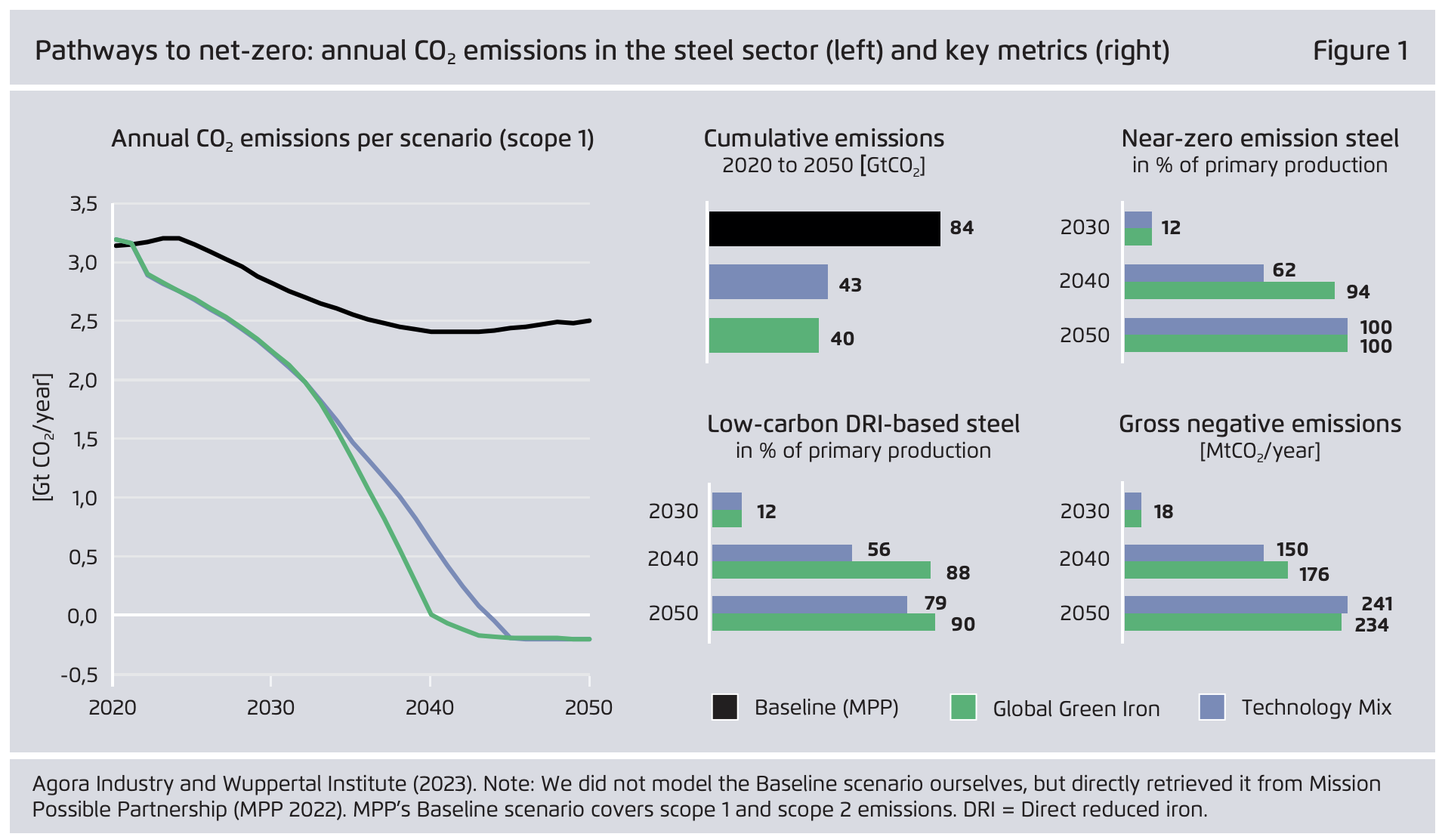
Image courtesy of Agora Industry and and Wuppertal Institute.
Agora finds that an accelerated steel transformation is possible using an increase of scrap metal input and hydrogen as an energy source for “direct reduced iron.” Transporting green hydrogen embodied in green iron is cheaper and easier than transporting hydrogen alone. Exporters can add value to their steelmaking and increase jobs in the industry. Importers, especially those with high renewable costs (or lack of access to renewable energy) can increase the competitiveness of local, low-carbon steel making. You can read about the progress of hydrogen for steelmaking here.
Agora has hope that carbon capture will have a place in the decarbonisation of the steel industry. However, this technology has proven unlikely to be able to assist. “Compared to other key technologies, steelmakers’ efforts to commercialise this technology are currently very low. If Blast Furnace-Basic Oxygen Furnace with post combustion Carbon Capture and Storage does not materialise, new coal-based steel plants face a high carbon lock-in and stranded asset risk.”
International regulatory frameworks will need to be set up and enforced.
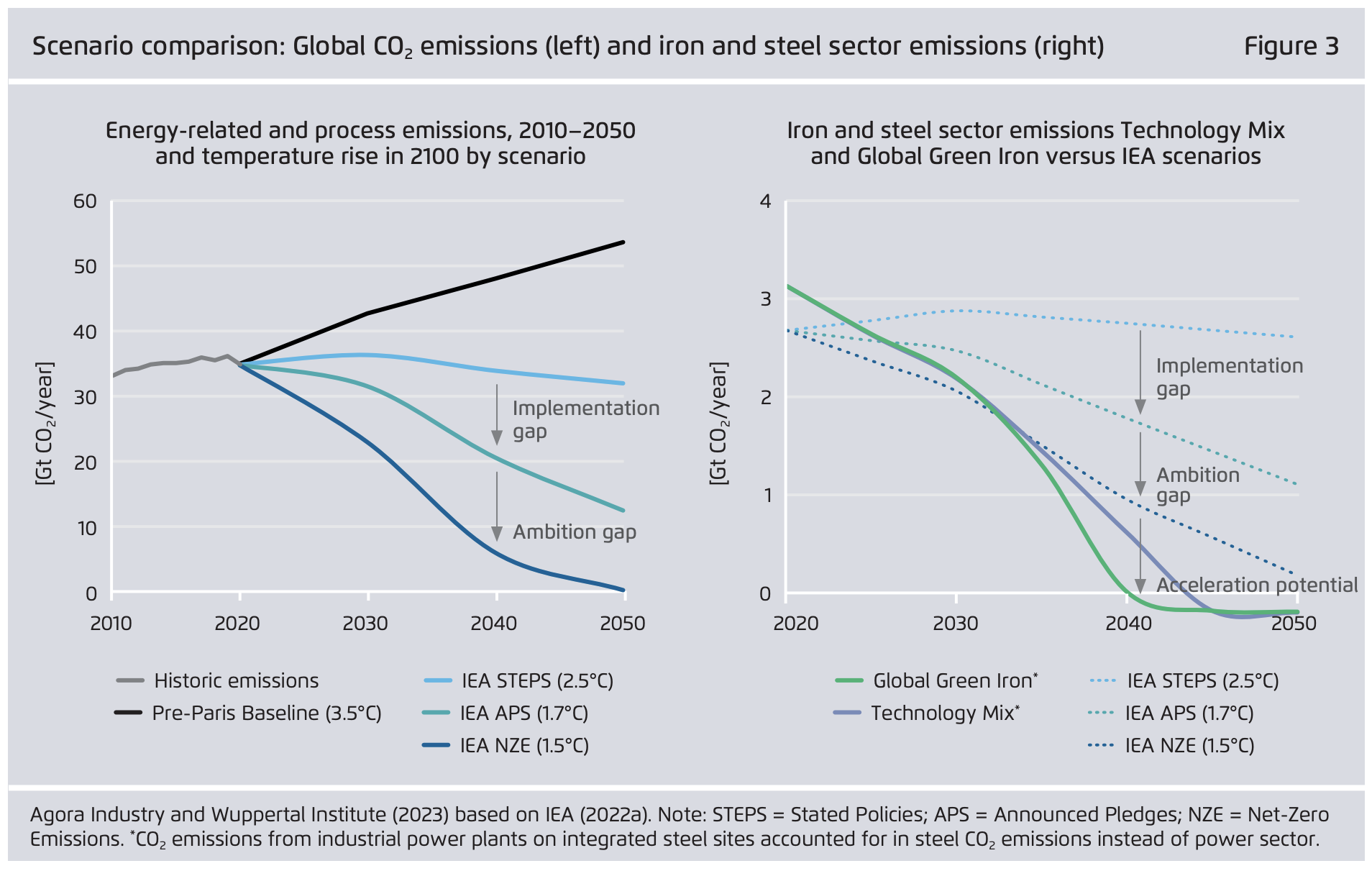
Image courtesy of Agora Industry and and Wuppertal Institute.
The old narrative about emissions reduction in the steel industry said the technology was not ready, the cost was too high, there isn’t enough renewable energy, and therefore, the steel sector will be the slowest sector to decarbonise. This narrative is being challenged by Agora’s researchers. The narrative they propose is that key technologies are available now, and new technologies are emerging. Although green steel can cost from 30–60% more to produce, the cost at end product is only 1 to 2% higher. Switching from coal to green hydrogen will provide the greatest reduction in CO2 emissions in the sector. CleanTechnica readers will be aware of the rapid buildout of green hydrogen projects. With that in mind, a zero-emissions steel sector is possible by the early 2040s.
Although many companies are working with the Science-Based Targets Initiative (SBTi) to certify that their climate targets are compatible with 1.5 degrees Celsius of change, over half of steel making companies are yet to commit or have targets too far in the future.
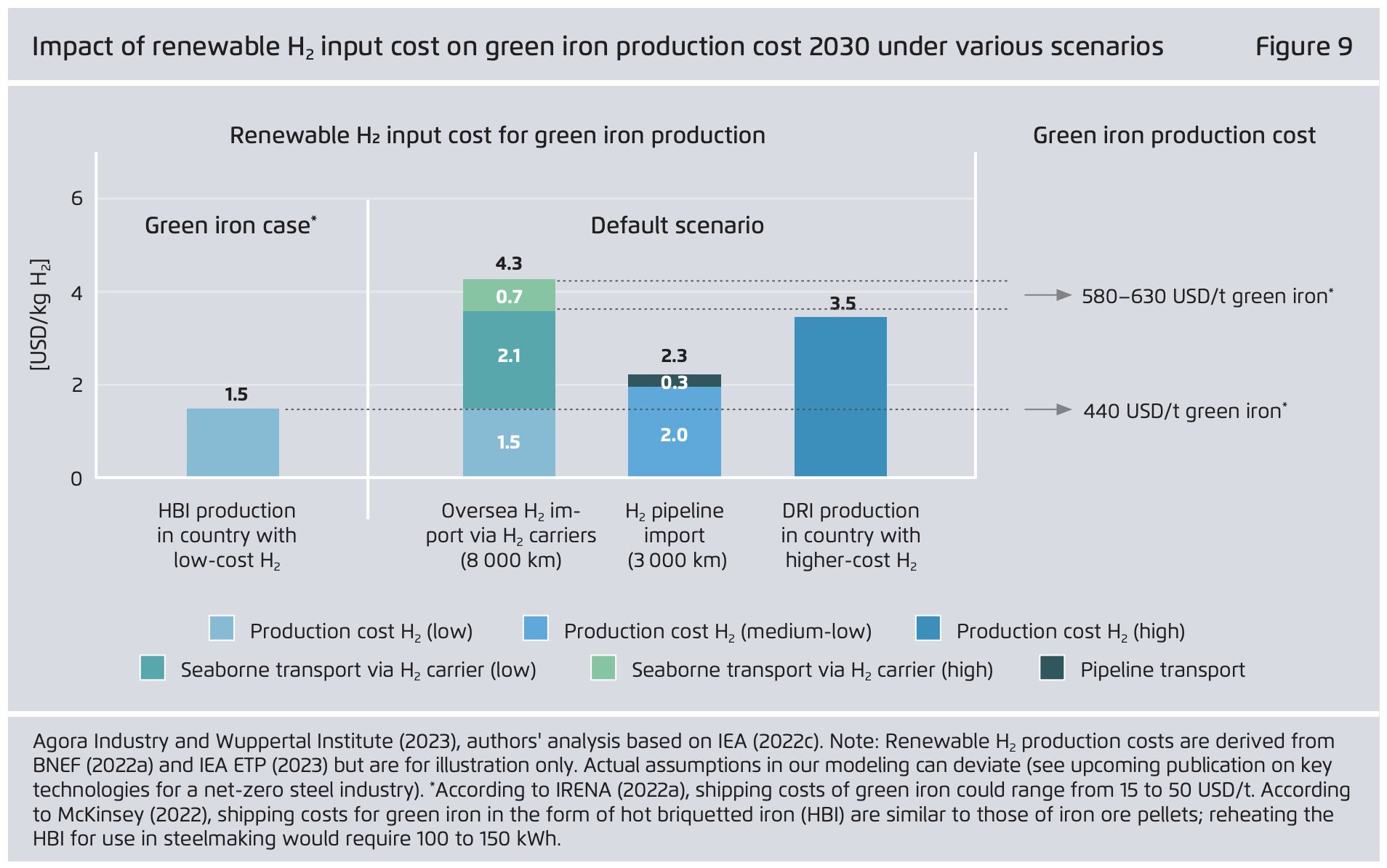
Image courtesy of Agora Industry and and Wuppertal Institute.
The report suggests that exporting countries like Australia and Brazil could export green iron with embodied green hydrogen rather than iron ore straight out of the ground (to importing steel making countries like China and Japan). This would be economically advantages to all.
“Moreover, shipping green iron instead of H2 and its derivatives will require significantly fewer process steps and less additional H2-related infrastructure. For example, compared to H2 transport by ship via ammonia which would require an ammonia plant in the exporting country, an ammonia cracking plant to reconvert to H2 in the importing country, as well as a H2 distribution pipeline to transport the H2 to the steel site, green iron transport will only require the construction of one HBI plant in the exporting country. Other than that, Hot Briquette Iron can basically use the same existing infrastructure as iron ore and can be transported by ship, inland vessel, and train. This is already happening today.
“While the case for green iron transport compared to overseas H2 transport by ship is strong from a purely economic point of view, there are further factors such as strategic autonomy, technology innovation, market power, and the benefits of hot charging the DRI in integrated steel plants that need to be accounted for when comparing green iron imports to integrated DRI production in steel plants.”
Agora posits that more than 70% of current blast furnaces will reach the end of their usable life in the coming decade. “These blast furnace operators will face a choice: relining their blast furnaces and locking in high emissions for more than a decade or substituting blast furnaces that have reached the end of their campaign life with low-carbon technologies. Ideally, all blast furnace operators should choose the latter option. But is that possible?” Will they end up as stranded assets?
“So even if a sizeable chunk of blast furnace capacity would have to be relined in the 2020s because low-carbon technologies cannot scale up quickly enough to replace all of them, due to the shorter lifetimes and the option of different retrofit measures, by 2040 more than 90% of all existing blast furnaces could be phased out without a premature shutdown. By 2043, all existing blast furnaces could be phased out without a premature shutdown. Overall, from a global perspective the stranded asset risk for existing blast furnaces is low.
“The 2020s are a crossroads for investment into new steel plants. They present a choice between a path- way that will lock-in high CO2 emissions for decades and incur a high risk of carbon lock-in and stranded assets, or alternatively, a pathway of net-zero compatible investment that provides future-proof jobs.”
Although action on climate change is taking place. “We are walking when we should be sprinting,” Chair Hoesung Lee of the Intergovernmental Panel on Climate Change (IPCC) summarises. The steel industry emits 8% of current global greenhouse gases. A fast-to-abate steel industry is crucial to keeping a livable planet. Agora assures us that this is technically feasible with the international cooperation of government. As Fatih Birol, the head of the IEA, put it, when the IEA Energy Technology Perspectives Report was launched in January 2023: “By working together, countries can be greater than the sum of their parts.”
I don’t like paywalls. You don’t like paywalls. Who likes paywalls? Here at CleanTechnica, we implemented a limited paywall for a while, but it always felt wrong — and it was always tough to decide what we should put behind there. In theory, your most exclusive and best content goes behind a paywall. But then fewer people read it! We just don’t like paywalls, and so we’ve decided to ditch ours. Unfortunately, the media business is still a tough, cut-throat business with tiny margins. It’s a never-ending Olympic challenge to stay above water or even perhaps — gasp — grow. So …
Sign up for daily news updates from CleanTechnica on email. Or follow us on Google News!
Have a tip for CleanTechnica, want to advertise, or want to suggest a guest for our CleanTech Talk podcast? Contact us here.
Former Tesla Battery Expert Leading Lyten Into New Lithium-Sulfur Battery Era:
CleanTechnica uses affiliate links. See our policy here.