Sign up for daily news updates from CleanTechnica on email. Or follow us on Google News!
As concrete month draws nearer to a close, it’s time to look at an option not previously explored, continuing to use limestone but bolting on carbon capture and paying for waste disposal in permanent sequestration sites. After fifteen years of assessing carbon capture technologies, pilots and proposals, this is one of the few use cases where it might be economically viable compared to alternatives.
For those who aren’t sick of hearing about limestone, it’s the primary raw material we make Portland cement out of. Limestone is the compressed remains of old sea beds that were covered in millions of years of the shells of mollusks and crustaceans, along with calcium carbonate that precipitated out of the water. There are two results from this. The first is that on land, we are never far from a supply of limestone, and as a sedimentary rock it comes in big, wide, thick layers that are easy to quarry. The second is that it’s chock full of the stuff we need for Portland cement, the calcium and oxygen we need to make calcium oxide (CaO) aka lime. A full 56% of limestone is lime, hence the name, and the rest is almost entirely carbon and more oxygen.
We get the lime out of the limestone by baking it in kilns at 900° Celsius. Every ton of limestone produces about 440 kilograms of carbon dioxide. While the calcination reaction only requires about 500 kWh of heat energy per ton of limestone in a perfect system, in reality limestone kilns require around 900 kWh of heat energy. While I’m using kWh, virtually no kilns use electricity because coal, natural gas, biomass and used tires are cheaper. About 140 kilograms of coal are required for that heat, and would release about 330 kg of CO2, 75% more CO2. About 85 cubic meters of natural gas would be required releasing about 164 kg of CO2, about 37% more. While cement manufacturers are claiming virtue by burning biomass and tires and are claiming much lower carbon dioxide emissions, I’m deeply skeptical about both.
However, the process heat can be electrified and the electricity can be low-carbon. Further, typically electric heat is more efficient than flames, but let’s assume the same 900 kWh is required.
Region | Cost per 140 kg of Coal (USD) | Cost per 85 m³ of Natural Gas (USD) | Cost per 900 kWh of Electricity (USD) |
---|---|---|---|
USA | $14 | $31 | $73 |
Europe | $19 | $111 | $117 |
Table of rough costs of energy for different sources per ton of limestone by author
This uses the average for heavy industrial users in Europe of around 12 euro cents per kWh, not the rate of around 20 cents truck stops will pay to charge trucks, by the way. If you’re wondering why cement plants don’t use electricity and avoid the carbon dioxide, the table above should make it clear. It’s more expensive. But will it be in the future? Remember that carbon pricing and regulation are coming for cement and concrete. The emissions from limestone kilns will increasingly be priced.
Energy Source | Kg CO₂ Per Ton of Limestone | Heat CO₂ Emissions (kg) | Total CO₂ Emissions (kg) | Carbon Price 2030 (USD) | Carbon Price 2040 (USD) |
---|---|---|---|---|---|
Coal | 440 | 305 | 745 | $186 | $223 |
Natural Gas | 440 | 181 | 621 | $155 | $186 |
Renewable Electricity | 440 | 21 | 461 | $115 | $138 |
Table of emissions for decomposing a ton of limestone by fuels with carbon price by author
As I noted last year, the EU is making clear what their target price for the emissions trading system (ETS) through their budgetary guidance for business cases. It’s fairly well aligned with the harmonized social cost of carbon in Canada and the USA. Carbon prices are expected to trend toward the social cost of carbon over time. The above table uses the USA/Canadia social cost of carbon in 2024 dollars, as with the earlier costs for coal, gas and electricity.
The above carbon emissions for electricity are based on an average of utility scale wind and solar per lifecycle carbon assessments, but as cement, steel and composites decarbonize, the emissions per kWh over their lifetime will diminish radically. There is no way to decarbonize burning natural gas or coal, however. That said, the emissions from the limestone dominate the mix.
The additional cost is effectively the budget that decarbonization solutions have to work within. As concrete month has shown, no solution is cheaper than just burning fossil fuels under limestone and using the atmosphere as an open sewer. As soon as emissions are priced, however, all bets are off.
Region | Cost of Cement per Ton (USD) | Additional Carbon Cost 2030 (USD) | Total Cost 2030 (USD) | Additional Carbon Cost 2040 (USD) | Total Cost 2040 (USD) |
---|---|---|---|---|---|
Europe | $140 | $225 | $365 | $270 | $410 |
USA | $130 | $225 | $355 | $270 | $400 |
Table of the impact of carbon pricing on a ton of cement by author
There are more costs to making cement, so let’s expand this out a bit. While limestone provides 560 kg of lime per ton of rock, cement requires 600 to 750 kg of lime for a ton of gray glue. Then there’s the clinker kiln, the large rotating drum into which lime, clay, supplementary cementitious materials and trace additives are placed for firing into granular ceramic clinker.
Real carbon pricing — and remember this is aligned with the EU’s budgetary guidance for business cases and the USA and Canada’s social cost of carbon — will triple the cost of a ton of cement made using coal for energy. We have our upper bound.
The first and most obvious thing this does is make low-carbon electricity a much more appealing option for the cement manufacturers using natural gas and coal. All of the nonsense they are spouting about electric heating being unproven and risky would go away when the alternative was paying a couple of hundred more by continuing to burn fossil fuels. The $60 to $100 gap between coal and electricity prices for heat to decompose a ton of limestone gets into the economic sweet spot, at least at the low-end.
Further, the historical coupling of natural gas and electricity rates in Europe is no longer holding up. One of the results of Russia invading Ukraine was the European energy crisis and that led to Europe pivoting away from natural gas to an extraordinary extent toward renewables, electrification and efficiency. That’s playing out now with heavy industrial electricity rates coming down. As of 2024, Germany is planning a special industrial electricity tariff ranging between US$0.06-0.10 per kilowatt-hour to enhance competitiveness. The cost of electrification of limestone kilns drops to $72 per ton of limestone, well under natural gas and only about $50 more than coal.
When basalt and other lime bearing rocks that don’t begin with the word lime came up, we found that basalt cost perhaps twice as much per ton as limestone while having a fifth of the lime, so would be result in lime that cost ten times as much. We need about 1.5 tons of limestone to make a ton of cement, and limestone costs $30 to $40 per ton. We would need 7.5 tons of basalt at $80 per ton to make a ton of cement, for a cost of $600, just for the raw materials, ignoring higher transportation costs and higher processing costs, which will add more to that. But $600 is outside of the budget, and so basalt isn’t a solution.
Geopolymers made from coal generation fly ash, blast furnace slag and aluminum manufacturing waste red mud were another point of study. My workups on the amount required and costs were for red mud, and hence higher than for fly ash and slag, which require much less processing to create polymer precursors. Fly ash is a dirt cheap resource and while the activators, sodium hydroxide and sodium silicate are more expensive, much less of them are used.
My cost workups for fly ash and slag geopolymers suggest that the cost of the amount required to replace a ton of cement should be less, but third party assessments indicate that it’s 30% more expensive to three times as expensive. As it’s barely used in the industry, it’s safe to say that my estimated costs were off and that it’s at least 30% more expensive. However, the range makes it clear that it’s in the range of the cost increases expected to be seen via direct carbon pricing or regulation, so it’s economically viable and likely to play a role.
Similarly, where there is a specific need for geopolymer concrete and a very large bauxite refinery right next to it, as in Shannon Foynes where manufacturing concrete floating wind turbine bases and masts is a very reasonable thing to consider, then it’s quite possible that red mud geopolymer will pencil out. Red mud has become a disposal problem for bauxite refineries, with the USA, Canada and Europe all banning dumping of it offshore, so refineries will be paying quite handsomely per ton to anyone offering to take it off their hands.
The carbon debt of the activators is more manageable as well. Sodium hydroxide is manufactured with electricity in the chlor-alkali process, so can be decarbonized with green electricity. Sodium silicate is manufactured in a high-heat furnace, but there’s zero requirement that it must be done with fossil fuels, so it can be decarbonized as well. Similarly, serious concrete reductions with finite element analysis, generate architecture, carbon fiber, engineered hardwood and renovating instead of demolishing will all be in the money.
But this assessment is more focused on the 440 kilograms of CO2 emitted from the limestone kiln per ton of limestone decomposed into lime. That’s about 660 kilograms per ton of cement, just from that source, the lion’s share.
How much will capturing and sequestering that CO2 cost? Surprisingly little to capture, given electrified heat and less if Sublime’s electrochemical process is proven able to scale and were used against limestone, as it produces a stream of pure, cold CO2 at 10 atmospheres of pressure, the best possible case for capturing it. Further, Sublime’s process possibly requires 50% the energy to decompose limestone, based on my benchmarking comparative energy demands of heat-based processes vs electrochemical ones, saving more money. Capturing it is in the range of $10 to $30 per ton. That cost shoots up to $50 to $100 per ton if coal is burned, so once again, electricity is the better option.
But what about sequestering it? This is trickier. Cement plants are everywhere, as concrete month has determined, because the 4.1 billion tons of it we manufacture every year are too heavy to move very far and limestone is ubiquitous. Say what you will about limestone’s other virtues, it’s terrible at keeping gases inside of it, so geographies with lots of limestone aren’t necessarily great for sequestration. For that, you need deep saline reservoirs, depleted oil or gas reservoirs, basalt formations or unmineable coal seams. Consider any numbers you see on their capacity to be 1% to 10% as big without fossil fuel extraction. They also aren’t remotely as widely spread out as limestone. Depleted oil wells and coal seams are especially dubious due to enhanced oil recovery and coal seam methane extraction. Deep saline reservoirs have a strong correlation to oil and gas producing regions, so there are talent, technology and firms to exploit.
Basalt is differently spread, occurring in regions where in geological time there was a lot of tectonic activity, and typically not offering up the opportunity to extract more fossil fuels. The fossil fuel industry is uninterested in this geological sequestration solution, and there is no industry in the region to pivot to sequestration.
In the USA, there are 103 cement plants, including 94 integrated plants and 9 grinding plants, distributed across its 50 states. Europe hosts 377 cement plants, encompassing both integrated and grinding facilities, spread across its 44 countries. India, with its 28 states and 8 union territories, has approximately 250 large cement plants, particularly concentrated in industrial states such as Andhra Pradesh and Rajasthan. China, the largest producer, boasts 3,408 cement plants, including 1,210 clinker lines and 2,198 grinding units, distributed across its 23 provinces, 5 autonomous regions, 4 municipalities, and 2 Special Administrative Regions.
Because of this mismatch of thousands of cement plants with the location of potential sequestration sites, pipelines for CO2 are required. This isn’t a technical concern. There are thousands of kilometers of CO2 pipelines in operation, albeit almost entirely in the USA for enhanced oil recovery. No, this is a liability concern related to concentrations of human beings.
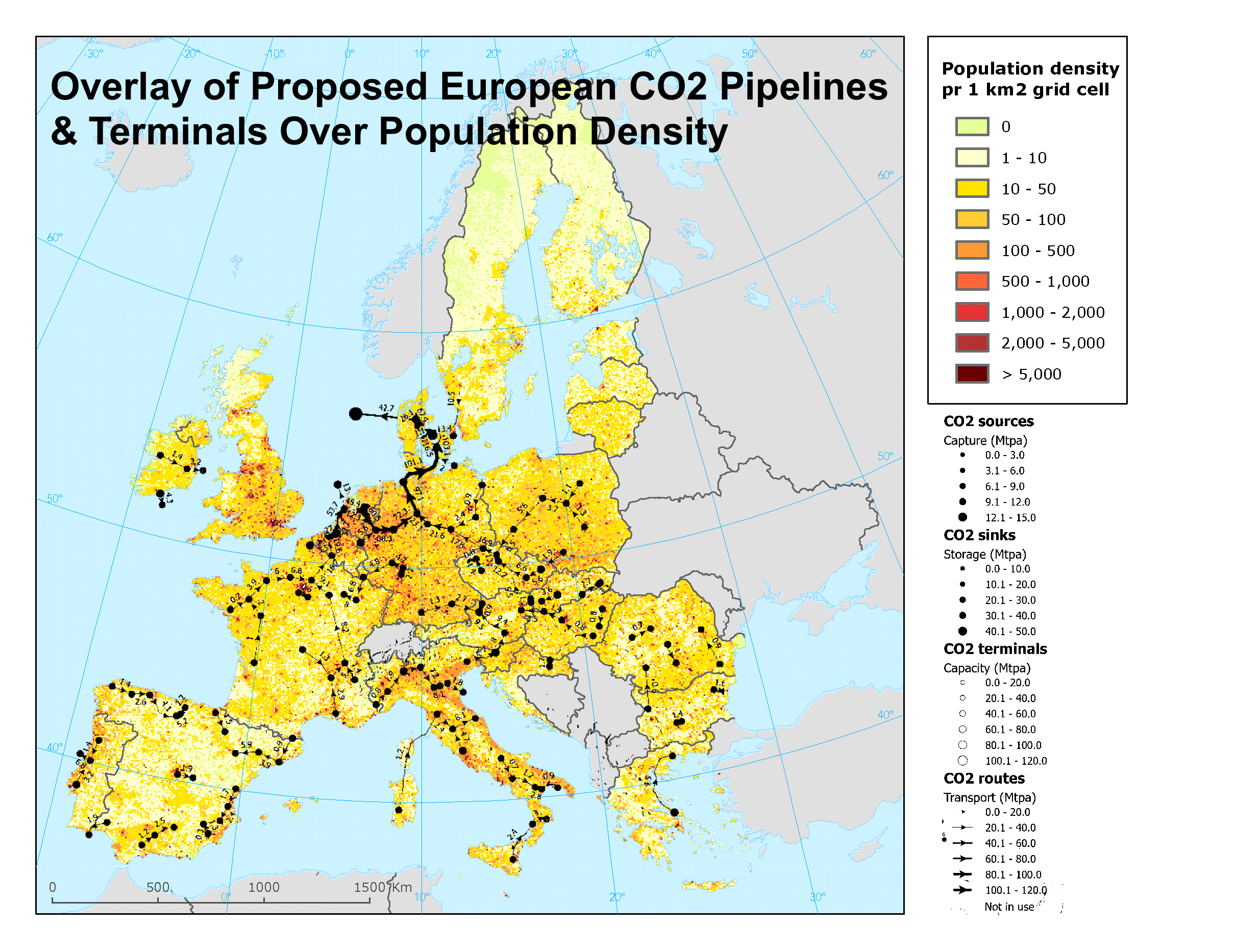
A few months ago I assembled this diagram. I overlaid the proposed CO2 pipelines in Europe with a population density map of the region. Why did I do this? Because in 2020 a tiny village of 41 residents in a sparsely populated part of western Mississippi manage to have more people hospitalized than it had in citizens due to a CO2 pipeline rupture 1.6 kilometers from the village across a highway. A couple of hundred people were evacuated. Cars wouldn’t start. Emergency vehicles couldn’t get into the region. Hours after the event, levels of CO2 in basements and some buildings’ room were sufficient to asphyxiate people.
The 377 cement plants in Europe are spread widely across the continent, but the pipelines run through population dense areas to where the CO2 can be pumped underground. What does this suggest?
Let’s start with the cost of pumping CO2 a thousand kilometers, a not unreasonable distance given the clustering of sequestration sites and the distribution of cement plants. It’s $10 to $20 per ton for liquid phase CO2, the same situation as Satartia. What does it include and exclude? The cost of CO₂ pipeline transport typically includes expenses related to compression, infrastructure, and ongoing monitoring to ensure the integrity of the pipeline. However, these costs generally exclude liability insurance for potential pipeline breaches, environmental remediation, and compensation for human fatalities resulting from accidents.
And that second sentence is the kicker. Excluding liability concerns masks the real cost of CO2 transport. In my assessment, whenever a CO2 pipeline goes through a more than sparsely populated area, it will be required to be in gaseous form. What does that cost? In the range of $30 to $50 per ton, much higher. The population density map of Europe covers 19,000 kilometers, and probably 30% of it would be costed at that rate. This is an optimistic cost simply because people will figure out that this is scary and fight it tooth and nail, proclaiming loudly that is essential, just somewhere other than where they happen to be living based on irrelevant criteria. And liability insurance is on top of that, so call it 5% on the total cost.
We’re up to $40 to $80 per ton. Then there’s the cost of sequestration, mostly subsea in Europe and deep underground in North America. That’s another $10 to $20 per ton per industry statements. So that’s $50 to $100 per ton, with 5% on top for liability insurance and unexpected costs. Oh, and everyone along this waste disposal chain has administrative costs wants to make a profit, so lets add another 10%.
End to end $60 to $115 per ton of CO2 from cement manufacturing safely sequestered back underground for all eternity, at least, we hope for all eternity. This is within the range of the additional cost of the projected carbon price in Europe at least, and not more expensive than some of the other alternatives.
Of course, this assumes that Europe actually goes ahead with this huge network of 19,000 km of increasingly expensive, governmentally backed CO2 pipelines and sequestration facilities so that cement plants have a nearby CO2 pipeline to tap into. And remember, cement plants are evenly spread, so the map above raises some questions. Does the south of France have no cement plants? What about Finland, Lithuania, Estonia and Latvia, all members of the EU for decades but with no sequestration sites or pipelines? Don’t they make cement there? Finland has two integrated plants, and Lithuania and Latvia each have one.
A reasonable size cement plant burning fossil fuels produces one to two million tons of CO2 a year. One heated by renewable electricity two thirds of that, perhaps 0.7 to 1.4 million tons annually. There are 377 cement plants in Europe as the geography runs smaller plants on average, so call it 200 million tons of CO2 even after electrification and we’ll be in the soccer pitch.
How many of the proposed 19,000 km of CO2 pipelines and related sequestration sites are in operation today? Zero. Cost estimates for the pipeline range up to EUR 23 million at the high end, and that’s much more likely than the low end of EUR 9. But that’s the cheap part.
Sequestration facilities are expensive. The EU’s Porthos project is intended to sequester CO2 under the North Sea. The bill for that one project is EUR 450 to 500 million. Surely for that amount of money, it could sequester all the cement CO2? Not even close. It’s expected to be able to manage 2.5 million tons of CO2 a year, the output of four to five of the 377 cement plants, and has a maximum capacity of only 37.5 million tons. Assuming 15% capital costs for annual operational costs, that’s EUR 30 per ton of CO2. This is above the rates above for sequestration, so there’s that. Also, the Porthos costs don’t include the cost of capital. Assuming 5% cost of capital, that turns into EUR 40 per ton. That’s over double, so add another $25 to the top end range for cement CO2 sequestration.
Add in the additional cost of electricity at sensible rates, and that’s a total of $120 to $190 extra per ton of cement, 2-2.5 times more expensive. Once again, this is in the money, assuming carbon prices and regulation combine to create the effect of the social cost of carbon. But it’s far above the cost of avoiding using cement entirely via finite element analysis, generative architecture techniques, mass timber, recycling cement and probably even fly ash and slag geopolymers.
What this analysis tells me is that carbon capture and sequestration will be a plant by plant choice, not a broad choice. Where a sequestration site is next to the cement plant and scaled sufficiently to take all of its emissions for decades, then a combination of electrification, possibly the Sublime process which produces cold, 10 bar pure CO2 and carbon capture and sequestration will be used. Finland, Sweden, Germany, France and Austria have robust, sustainable forestry industries, and as I’ve noted, pivoting from bioenergy and single use paper products to mass timber is a higher merit order use of forestry resources. Much of Europe will simply pivot to mass timber, in other words, for a lot of construction, and cement manufacturing will dwindle.
But that’s in the EU, which is taking all of this seriously. In the USA, which isn’t federally pricing carbon, but is at least pricing major emissions of methane — although people keeping pointing out the loopholes and limitations of the methane tax — there is no major national organization strategically defining what CCS might be required, where or how much. Instead, as with so many other things, it’s federal grants, loans and tax breaks for CCS, with the private sector expected to figure out all of the details.
What that means is that ExxonMobil is expanding its LaBarge enhanced oil recovery facility by 1.2 million tons a year from its current 6-7 million ton a year run rate, and that it expects to get more CO2 from natural gas extraction, not cement plants. It means that Project Bison, a direct air capture facility with nothing to do with cement plants or anything sensible, has already received about $12.5 million dollars and has its hands out for more of the $4 million in tax credits for carbon capture. It means the Summit project in North Dakota is expecting to get its CO2 from ethanol and natural-gas blue hydrogen ammonia fertilizer plants in surrounding states, not cement plants, but at least has an 8-20 million ton annual potential capacity, and possibly 30 years of storage. These have reached final investment decision (FID), but aren’t in operation and the entire thing might fall apart.
For cement, pickings are slimmer. The Lehigh Hanson cement plant in Mitchell, Indiana has reached FID on a plan to capture 1-2 million tons of CO2 annually starting around 2030. LafargeHolcim, in partnership with Svante, Total, and Occidental, is developing a CCS project at its cement plant in Florence, Colorado that aims to capture up to 725,000 metric tons of CO2, but hasn’t reached FID. Cemex USA is evaluating the implementation of CCS technology at its cement plant in Victorville, California. National Cement in California has received about $500 million from the DOE for a suite of solutions including CCS. One of 103 plants has reached FID. Three others have plans and one has funding. That’s all that I was able to find.
The large majority of US cement plant operators are simply ignoring this and hoping it will blow over it would appear. A great deal of US funding is going to calcined clay, a supplementary cementitious material which reduces the amount of Portland cement required, but which isn’t that much better than fly ash or slag at avoiding CO2 emissions in concrete and are more expensive, and so never used without federal money. A bunch of money is going to material substitution plays, with almost $190 million going to a startup that wants to use basalt, which you’ll remember will make cement about $600 more expensive, so will never be used, as well as recycled cement from concrete.
The recycled cement at least has potential, as about 300 million tons of concrete are in demolition waste streams in the country, and if 90% of the cement is recoverable, that might 25 to 30 million tons of new cement in a country which manufactures 85 to 100 million tons of cement annually. Just as with steel, the massive infrastructure and building boom from the New Deals and the period of industrialization have led to an awful lot of stuff that’s being demolished and recycled. Sublime’s electrochemical process for stripping the cement out of crushed concrete, just as it is able to work against limestone, has potential, if it can scale and be inexpensive enough. The basalt-focused firm asserts that it can use recycled concrete too, but their pitch is all basalt, diabase and dacite, rocks with vastly less lime than limestone has, effectively making them a very expensive manufacturer of supplementary cementitious materials with a sideline in very expensive cement. They are very well funded, as noted, and pretty aggressive about defending their odd story, as I know from personal experience.
The combination means that the USA is winging it, hoping that throwing some federal money at innovation and CCS will result in decarbonization. It won’t. The only thing that will lower high CO2 emissions from cement is an actual carbon price with teeth, something missing in action in the country. At present, only California’s cap and trade carbon system includes cement, and it’s only at $30 per ton of CO2. That’s enough to push finite element analysis, generative AI and some mass timber perhaps, but nothing else.
For the rest of the world, China doesn’t do the kind of drilling for oil and gas that leads to massive opportunities for carbon capture, although they have the ability to develop it just fine and have very large geological storage capacity and 100 CCS pilots of various scales, though one of the biggest ones is naturally for enhanced oil recovery. It also has a lot of newly harvestable forest from its massive tree planting program that’s been running since the 1980s, so along with a reduction in new construction, can pivot to mass timber for a lot of it. India doesn’t have much oil or gas either, so carbon capture is going to be iffy in that country as well — naturally the CCS project that’s expected to launch first is for enhanced oil recovery —, although they have already brought cement emissions down well below the world average with a decade of concerted effort and are a leader in calcined clays. They also have a robust forestry industry, so can pivot to engineered timber. As I noted when looking at solutions for avoiding cement and concrete, a great deal of the developing world has significant timber resources so mass timber is likely to accelerate.
The cement industry is toying with the idea of carbon capture and sequestration, but has no internal ability or expertise in pipelines or subsurface sequestration. Carbon capture remains a focus of the oil and gas industry which sees it as another revenue stream and a way to value their tapped out wells, less than a realistic, scaled climate solution. All in all, it’s hard to see carbon capture being a big part of cement decarbonization anywhere in the world.
Have a tip for CleanTechnica? Want to advertise? Want to suggest a guest for our CleanTech Talk podcast? Contact us here.
Latest CleanTechnica.TV Videos
CleanTechnica uses affiliate links. See our policy here.